Download in PDF format [553 Kb]
- Looking at the Big Picture
- MotorMaster+, EPAct and NEMA Premium™
- Software Finds the Hot Spots
- Improved Design Guide
- Significant Savings
- Understand the Nameplate
- Working with Your Motor Service Shop
- Using Motors Correctly
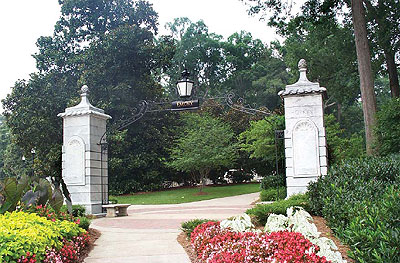
Electric motors account for about 60% of the power used in U.S. industrial buildings. The figure is closer to 50% in commercial structures and somewhat lower still in homes, where lighting and other loads dominate consumption. But what about schools and universities? Are motors the heavy power hogs in academia?
They certainly are at Emory University, the prestigious 166-year old Atlanta institution (Top Image). Emory is now home to some 11,000 students and 2,500 faculty members, plus researchers and support staff engaged in fields ranging from theology and molecular biology to law and international studies. Their interests and goals may be diverse, but they share at least one common need: to work, study and live in comfort.
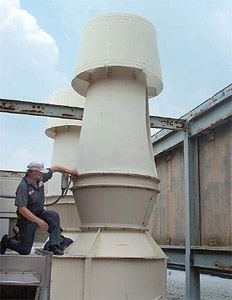
Atlanta's average temperatures remain at or above 79F (26C) between May and September, and to keep its students and faculty cool, Emory operates a large heating, ventilating air-conditioning and refrigeration (HVACr) system. Emory's centralized chiller plants make up a total of more than 27,000 tons of air-conditioning capacity, and there also are many stand-alone chillers plus more than 400 air handlers on campus (Figure 1). An HVACr system of that size demands a lot of electrical energy.
Just ask L.D. Kicak, RIAQM, manager of HVACr operations/ refrigerant compliance manager in the University's Facilities Management Division. Our centrifugal chillers alone account for about $2.5 million of Emory's annual energy costs, he says, or more than 25% of our total power bill. The motors that drive our chillers and air handlers make up the largest electrical loads on campus. In total, Emory operates thousands of motors, although many of them are smaller than 5 hp. It's the large chiller motors we're mainly concerned with.
Kicak's responsibility is making sure that Emory's HVACr department operates reliably and efficiently, but he also has to keep the University's energy bill within budget and see to it that the department spends wisely on HVACr equipment. Those responsibilities, plus compliance with the University's high environmental standards, focus his attention on efficiency. Because our chillers use so much power, he says, we want to make certain they operate as efficiently as they were designed to be. When we purchase a new chiller, we always want to know which is the most efficient chiller for the application. The chiller may cost us more initially, but we're interested in payback, reliability and maintenance issues.
Motors are the key to high efficiency, he emphasizes. Our OEM suppliers know we understand that, so we haven't had to demand high-efficiency motors in new equipment because they're already there. Reliability is also very important. We have a lot of various types of research being conducted here at the University, and we have to maintain exacting conditions set by the researchers and the equipment that supports them. Premium-efficiency motors play a key role in reliability. We maintain our systems to make sure they operate reliably and within design standards. We now employ a Demand Based Maintenance Program which routinely checks things like bearing lubrication, drive belt tension, heat exchanger tubes, water treatment chemicals and other items that affect our chillers and air handlers. All that maintenance helps keep both reliability and efficiency high, but high-efficiency motors are only one of the keys to our electrical energy efficiency.
Back to TopLooking at the Big Picture
When Kicak joined Emory, keeping chillers operating efficiently was a less-than-exact science. No one had ever collected the necessary data or analyzed it, he recalls, even though it was there all the time. I found that we needed to look at the big picture and ask some questions we hadn't considered before: Is the equipment operating as it was designed? What factors should we be watching? What can we improve? Are we buying the right equipment and maintaining it as we should?
There had been a lot of Band-aiding back then, but very little real data collection and implementation, and equipment was repaired when it broke down. The system kept running, but Kicak knew the situation could be improved. Subsequently, Kicak presented his Demand Based Maintenance Program, which is based on much of the information contained in this case history, at the 26th World Energy Engineering Congress held in Atlanta.
We rebuilt our motors or replaced them in kind, based on age and condition, Kicak says. Upgrading to higher-efficiency models wasn't an issue. Now, we work with an experienced motor service center whose owner understands the connections among reliability, efficiency and cost. He's helped us upgrade our motors, and that has saved us money and kept our reliability high. We also have some new tools that make our job easier.
Back to TopMotorMaster+, EPAct and NEMA Premium™
One of those tools is MotorMaster+, software developed by the U.S. Department of Energy (DOE). It helps users select efficient, cost-effective motors. It contains a large database of integral-horsepower motors sold in the USA, including motors that fall under the Energy Policy Act of 1992 (EPAct) and many older models that do not. Using a built-in spreadsheet, users can compare a motor's costs based on operating conditions, utility rates, demand charges and other factors. The software then compares the cost, in kWh and dollars, of buying a new, more efficient motor vs. rebuilding an existing one. The program even calculates the payback period for the new motor's cost premium, if any. MotorMaster+ software is available by request at AMO Tools Help Desk.1
MotorMaster's database also lists motors that meet or exceed NEMA Premium efficiency ratings. The ratings, published by the National Electrical Manufacturers Association, are nominally one to two percentage points higher than those stipulated under EPAct. Motors that meet NEMA Premium standards are among the most efficient units currently available. NEMA Premium standards extend to motors through 500 hp.2
Back to TopSoftware Finds the Hot Spots
Mr. Kicak's second energy-saving tool is a sophisticated data-logging and analytical program called ChillerCheck. The software was developed by Larry Seigel, founder and president of Chillergy Systems LLC, an Atlanta-based application service provider. Emory beta-tested the software for Chillergy and now uses it full-time.
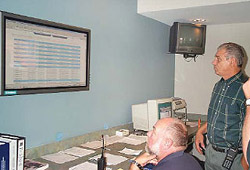
When efficiency loss drops more than 5% from the nameplate rating that's the action limit we recommend the operator can switch chillers and dispatch a maintenance crew to the underperforming unit. The source of the efficiency loss and the way efficiency changes (abruptly or gradually, for example) tells an experienced operator more about the problem, be it a loose drive belt, fouled heat exchanger tubes, a malfunctioning valve or a failing motor.
ChillerCheck can also detect certain power problems, such as phase imbalance, that can lead to decreased efficiency (and sometimes damage) even in a high-efficiency motor. The objective is to miminize system-wide energy use. To date, Emory estimates they've realized chiller energy efficiency savings in excess of $300,000.
Back to TopImproved Design Guide
Another energy-saving tool is an updated version of the university's Design Guide, the standard for electrical and mechanical work. The current design guide addresses certain energy conservation issues, like calling for the installation of high-efficiency motors wherever possible. It also contains such important power quality provisions as requiring all-copper wiring (Figure 3a), proper electrical grounding and lightning protection (Figure 3b).
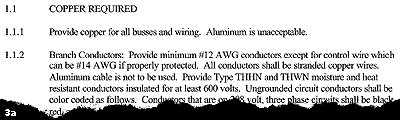
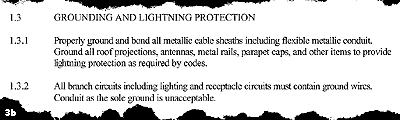
Working with the university's energy engineer, Kicak is strengthening the guide to include, among other things, a standardized motor repair/replacement policy and higher efficiency requirements for motors. Kicak already replaces failed motors smaller than 25 hp with high-efficiency motors. Failed motors larger than 25 hp are also replaced with highefficiency models, although old motors in this size range are rewound and stored for use as emergency back-up units because, as Kicak points out, he can't afford to wait for a replacement when a chiller motor fails. The new Design Guide will formalize this policy.
A number of premium-efficiency motors are installed in Emory's HVACr system. One example is a 40-hp NEMA Premium pump motor installed at one of the system's many cooling towers (Figure 4). This motor carries the NEMA Premium label, and its nameplate calls out the required NEMA nominal efficiency of 94.1% as well as a guaranteed minimum efficiency of 93.0%. The motor replaced a standard- efficiency model.
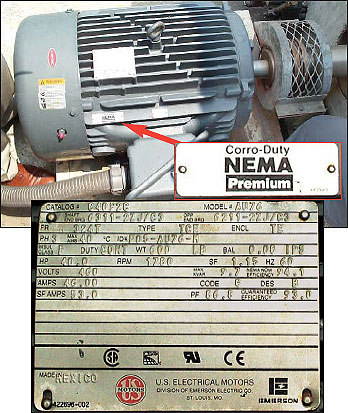
Figure 5 shows another example. The three motors originally installed on a set of condenser water pumps were standard- efficiency models. One high-efficiency motor was installed as a replacement several years ago (Figure 5, center). More recently, a premium-efficiency motor was installed when another one of the original units failed. The motors' nameplates and labels are informative.
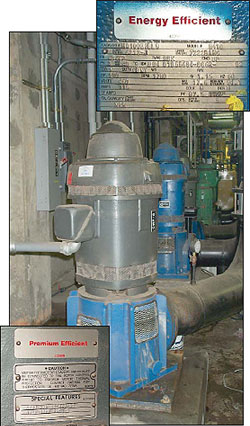
The motor labeled Premium Efficiency claims a nominal efficiency of 95.0%. That's a substantial improvement over the 92.3% industry average for standard-efficiency motors of this size, although it falls slightly short of the 95.4% nominal efficiency required to meet the NEMA Premium standard (which was published in mid-2001).3 The motor labeled Energy Efficient claims a 94.1% nominal efficiency. The same manufacturer made both of these replacement motors, as well as the NEMA Premium-rated motor shown in Figure 4. The lesson: read the nameplate and understand what it (and any manufacturer's label) means. Prior to introduction of the NEMA Premium label, the term energy efficient or premium efficiency had no common definition.
Significant Savings
MotorMaster+4.0 shows how much energy and money the improved motor in Figure 4 saves. Operating continuously for 8,000 h/y at 75% of rated load, the 40-hp NEMA Premium cooling tower motor consumes 189,340 kWh/y costing $6,627 annually at $0.035/kWh, Emory's current utility rate. A rewound, standard-efficiency motor of the same size would consume 200,224 kWh/y at a cost of $7,008. The annual energy savings generated by the NEMA Premium motor, therefore, totals $381 when compared with the cost of operating the standard-efficiency motor it replaced. At 50% discount from list price, the payback period for the new motor's additional $659 cost over rewinding the old is only 1.73 years.
It is also interesting to note that Emory negotiates a utility rate of only $0.035/kWh, substantially lower than the average rate paid by industrial users nationwide. Users faced with higher rates would see proportionally larger savings by installing high-efficiency motors. And, in some areas, local utilities offer cost-sharing incentives to customers who install the improved motors.
Back to TopUnderstand the Nameplate
The motors shown in Figure 5 illustrate the importance of understanding motor labels. The 100-hp inverter-duty motor in the foreground is clearly labeled Premium Efficient. The label should not be confused with one reading NEMA Premium. The motor's efficiency, while it is quite high at 95.0%, falls just short of the 95.4% nominal rating required by the NEMA Premium standard for motors of this size. (Recognize that the motor was installed at least a year before the NEMA Premium designation was published. Also, the NEMA Premium designation doesn't apply to verticalshaft, inverter-duty motors like this one.)
The somewhat older, blue 100-hp motor seen at the rear is simply labeled Energy Efficient. Its nameplate lists minimum efficiency at 94.1%. That value does exceed the minimum needed to meet EPAct requirements for motors of this size even though EPAct doesn't apply to motors of this type. But, obviously, the motor doesn't meet NEMA Premium standards. These examples point out the need to read the nameplate data, and compare the efficiency quoted to the NEMA Premium minimums, irrespective of the descriptive label.
Back to TopWorking with Your Motor Service Shop
Kicak has cut Emory's power bill for chillers by 10% so far, and he thinks he can double that in the future. He credits high-efficiency motors and his use of ChillerCheck for most of his savings to date. Motors will become increasingly important cost-cutters in the coming years, as older motors now in the system reach the end of their service lives.
Having the right relationship with your motor service center is critical when it comes to motor decisions, says Kicak, who has selected one supplier, McCullough Electric Motor Service, Atlanta, for much of his chiller-related motor repair and replacement.
Sam McCullough is the service center's owner and chief technical specialist. McCullough has seen motor replacement take on new importance, especially at Emory. We've worked with Kicak for a little more than three years now, says McCullough, although we'd been selling and servicing motors at the University since my father founded our shop more than 50 years ago. Sixty percent of our business used to be in rewinds and 40% in new sales, but now it's just the opposite. A lot of that change has to do with more calls for higher-efficiency motors. Rewinding won't improve efficiency above what it was when the motor was new, so if operating costs are important, we recommend premium-efficiency motors wherever they can be used.
Back to TopUsing Motors Correctly
No question, high- and premium-efficiency motors can save many times their purchase price over their service lives, but their selection must be based on solid engineering analysis if high savings are to be realized. For example, some highefficiency motors operate with less slip than conventional motors, and therefore they run a bit faster. The power required to drive certain centrifugal loads, such as air handlers, is proportional to the cube of rotational speed, and a high-efficiency motor that drives such loads at higher speed may actually consume more power than a slower, lower-efficiency model. This problem can be averted through the appropriate choice of motors or by installing speed-reducing pulleys or variable-frequency drives (VFDs).4 Emory University's Design Guide takes those factors into account, calling for coordination regarding motor selection and equipment requirements and specifying high-efficiency variable speed drives.
Energy savings, cost savings, high reliability and cool customers: they're all in a day's work for L.D. Kicak and his team. Service is number one. Everyone outside this office is my customer. Good thinking . . . and a good energy program at one of the country's top universities.
Back to TopThe Principals
L.D. Kicak, RIAQM, is the manager of HVACr operations/refrigerant compliance manager, in the Facilities Management Department at Emory University. He has been involved in the HVACr industry since the mid-60s. He is a member of many organizations which include Environmental Education Foundation, Association For Facilities Engineering, RSES and others. He has written several papers and presented articles at local, national and international events. Mr. Kicak can be reached at 404- 727-2721 and at LD.kicak@emory.edu.
Sam McCullough is owner of McCullough Electric Motor Service, Atlanta, Georgia, a full-service motor and equipment sales and repair shop in business since 1952. McCullough is a member of the Electrical Apparatus Service Association, Inc. (EASA), and adheres to their high quality standards, or better, when servicing electric motors. A highly experienced professional in the field of motor selection and installation, Mr. McCullough can be reached at 404-525-0821, FAX 404-522-5291.
Larry Seigel is president of Chillergy Systems LLC, an Atlanta-based application service provider. Among other services, Chillergy supplies ChillerCheck software to commercial, institutional and industrial clients worldwide. Mr. Seigel can be reached at 678-762-0340 and at Lseigel@bellsouth.net.
Footnotes
USA addresses only.
EPAct is a federal law that sets minimum efficiency ratings for certain motors sold in the USA after 1997. Efficiencies for EPAct-compliant motors are between one and four percentage points higher than those of older "standard-efficiency" motors. EPAct addresses only general purpose motors between 1 hp and 200 hp, T-frame, single-speed, squirrel-cage, induction type, 230/460V, NEMA Designs A or B, continuous rated, 60Hz, 2-, 4- and 6-pole (3600-, 1800- and 1200-rpm), open and enclosed.
Motors meeting NEMA Premium standards are not always identified as such because use of the NEMA Premium term and label is voluntary, even among NEMA members. Lack of a NEMA Premium label does not necessarily mean that a particular motor does not meet the standard. Check a particular motor's nameplate efficiency against NEMA Premium minimums published by NEMA, CDA and others. The data on NEMA Premium motor efficiencies are available on our site. Minimum efficiency ratings listed in the standard conform to NEMA MG 1-1998 (Revision 3), Tables 12-12 and 12-13.Average efficiency of standard-efficiency motors as reported in MotorMaster+.
Premium-efficiency motors may have characteristics different from standard- or EPAct-efficiency motors, such as starting current, torque, speed, etc. All engineering parameters must be taken into account when considering replacement.