Download in PDF format [1.69Mb]
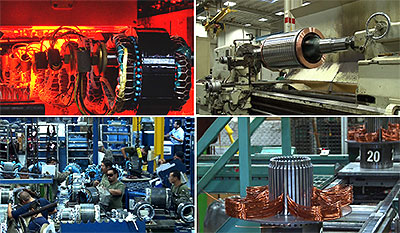
Introduction
When it comes to developing new motor technologies, copper continues to be integral to constant improvements in motor efficiency. The standard induction motor achieved significant gains in efficiency through more copper in the windings, a higher-grade steel core, improved bearings and insulation, and improved cooling fan design.
As the search for ever increasing efficiency brings the advent of new motor technologies and designs beyond the induction motor, copper will continue to be integral to the efficiency and longevity of these new technologies: from switched reluctance motors, permanent magnet motors and copper motor rotors.
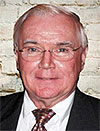
E.F. ‘Ned’ Brush, Ph.D. of BFF Associates
According to E.F. ‘Ned’ Brush, Ph.D. of BFF Associates and expert in the area of motor technology, “The traditional major motor technology has been the induction motor. More recently, there is the permanent magnet motor, which has higher efficiency ratings and the switched reluctance motor with improved efficiency for specific application. Each has its place. The induction motor has been the workhorse in the industry for over 100 years. Although the induction motor has been around for that long, there are exciting developments in the motor design itself, achieving improved efficiency. One of those innovations is the development of the copper rotor motor, which can reduce motor losses by as much as 12 to 15%.”
This publication focuses on copper's role in energy efficiency improvements in new motor technologies. Industry experts share their first-hand knowledge as they discuss the applications, advantages, and disadvantages of each type of motor. Each has a special place, or niche, in the marketplace. Having a better working knowledge of new types of motors will be of value to the plant engineer, facility manager, and anyone working with or purchasing motors for industrial applications.
Back to TopPermanent Magnet Motors
Technology
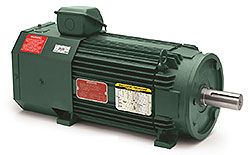
Long used in servo motor applications, Permanent Magnet Synchronous Motors (PM) are gaining increased use in industrial motor driven systems. The PM motor technology replaces the aluminum bars in the rotor with powerful permanent magnets created using rare earth elements; these are either surface mounted (SPM) or internally mounted (IPM). According to John Malinowski, Senior Product Manager, Baldor Electric Company, Ft. Smith, Arkansas, “The basic stator in a permanent magnet motor is very similar to that of a traditional copper wound induction motor; only the rotor in these motors is unique, using permanent magnets either glued to the surface of the rotor or bar magnets embedded in the rotor laminations.”
Motor manufacturers have demonstrated that permanent magnet designs offer efficiency gains as high as three NEMA bands higher (1.5 – 2%) than a Premium Efficient AC induction motor. However, in most cases these gains cannot be achieved without pairing the PM motor with a variable speed drive (VSD). Despite the fact that there is less copper in the permanent magnet motor than in a similarly rated AC induction motor, it still relies on copper in its operation to make it more efficient.
Mr. Malinowski points out, “The permanent magnet motor is very power dense, that is, how much horsepower, how much torque, the motor can produce compared to its physical size.” Thus, frame adapters are now required to compensate for the change in shaft height.” Manufacturers meet this challenge by making permanent magnet motors in the same NEMA and IEC AC induction motor frame sizes in order to enable easier retrofits.
In common use today, the permanent magnet motors drive both hybrid and full electric vehicles, such as the Toyota Prius and the Chevy Volt. Compressor manufacturers are starting to incorporate permanent magnet motors because the motors can operate at very high speeds without the use of speed increasing gearing, which is inefficient.”
Permanent Magnet Motor Advantages
- Excellent torque-speed curve
- Excellent dynamic response
- High efficiency and reliability
- Low maintenance
- Longer lifetime
- Low acoustical noise
- High-speed capability
- High torque/volume ratio or high power density
Permanent Magnet Motor Disadvantages
- High cost
- Need for a variable speed drive (VSD)
- Rare-earth material availability
Permanent Magnet Motor Applications
- Cordless tools
- Maglev Trains
- Wind turbines
- Hybrid vehicles
- Air conditioning units
- Washing machines
- Medical equipment (MRI’s)
- Industrial motors
Switched Reluctance Motors
Technology
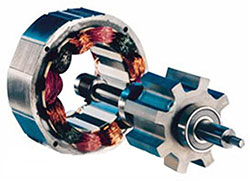
Graphic Courtesy of NIDEC Motors
A switched reluctance motor (SRM) is a brushless DC electric motor that provides continuous torque. The SRM electronic drive is characterized (paired) to the motor; together, they form a very capable, closely matched system. The SRM is a viable replacement and improvement to induction motors in variable speed applications. Mr. Rob Boteler, Manager of Government Relations NIDEC Motor Corporation, St. Louis Missouri, notes that, "The switched reluctance technology has been around since the 1800s. What has occurred to bring this technology into the forefront of today's advanced motors is the advent of power electronics and computing capability that allows commercially viable implementation." Along with permanent magnet technology, NEMA’s Motor Generator (MG-1) Section expects to develop a standard for switched reluctance motor technology in the future.
Mr. Helmuth Glatt, VP of engineering, NIDEC Motor Corporation believes that the SRM has some distinct advantages over conventional motors. "One of the biggest differences that we have for a SR system is that it can operate with one of its phases missing or shorted out – an instantaneous stop-mode for a permanent magnet or induction motor system.”
The quantity and type of copper wire are very important in the design of a switched reluctance motor. Each turn of the coil nests together to help fill the large stator slot allowed by the SRM design. As Mr. Glatt explains, “Copper is a key component to our coils. We usually use 100% copper to wind our electric motors because it has much lower electrical resistance than alternative materials such as aluminum. Low winding resistance translates directly to less waste heat, thus improving energy efficiency and advantageously reducing the motors operating temperature”. When necessary the SRM uses a coil made of roped copper wire or Litz wire; the wire is made out of many smaller strands of copper wire twisted into the shape of a rope which is formed into a rectangular geometry. Using this type of wire transposes the conductors reducing skin effect, a phenomenon that results in the current migrating to the outside of that conductor, effectively increasing the resistance of the conductor. “
SR systems manufactured today are well suited for industrial application and are viable alternatives to other variable speed systems.
Switched Reluctance Motor Advantages
- High efficiency, especially over a wide load range
- High torque and speed
- Exceptional constant-power speed range capability
- High reliability and long lifetime
- Simple and robust construction
- High power density
- Presently a standard product in NEMA specifications from 15 hp to 525 hp
Switched Reluctance Motor Disadvantages
- Ripple torque
- High vibration level
- VSD necessary
- Acoustical noise1
- Slightly less peak efficiency than PM motor
Switched Reluctance Motor Applications
- Washing machines
- Centrifugal machines: compressors and pumps
- Vacuum cleaners
- HVAC
- VSD systems
- Automation
- Machine tools
- Traction
- Rock crushers
Copper Rotor Motors
Technology
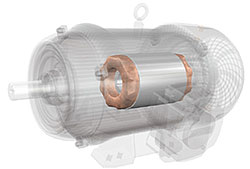
The innovation of the copper rotor motor technology was born out of the need to meet the low voltage motor market demands for greater energy efficiency; a demand not met by the traditional die cast aluminum rotor design. John Caroff, Marketing Manager, Low-Voltage Motors, Siemens Industry, Inc., Norwood, Ohio, stated that, "The goal was to gain efficiency using new copper rotor technology but retain the same footprint as the traditional aluminum rotor design; this is important, not only for new applications, but also for retrofit applications. Commercial high-temperature rotor casting machines were non-existent. To develop this new technology, we worked with the Copper Development Association (CDA) to design the rotor, and even more important – to design and develop the complicated rotor casting process.”
The significant investment in design and development of the CRM was justified by the efficiency gains over the conventional aluminum rotor designs. According to Mr. Caroff, "The initial purchase price of a copper rotor motor is slightly higher than the aluminum rotor motor making the payback justification a factor. However, payback is relatively short and generally not an issue given the typical 20 year design life of the motor. The die casting of a solid copper rotor yielded greater efficiency in the same size motor as a traditional energy efficient motor, utilizing die cast aluminum technology.”
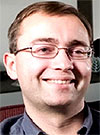
J. Balcerzak, In Plant Sales and Motor Product Manager, KJ Electric, Syracuse, NY
Designed in the US to exceed the stringent NEMA efficiency table standards (MG1 Table 12-12) and exceeding the efficiency compliance with the 2010 EISA legislation, the CRM also gained the performance advantage in the European 50 Hz IEC motor. The use of copper rotor motors as replacement motors for European equipment in the US is a great opportunity for end-users to increase revenue while meeting legislation. Copper is an amazing material. By using the copper rotor in our IEC motors we not only achieved the new efficiency requirements in Europe (IE 2, IE3) and USA (MG1 Table 12-12), but we were also able to reduce, in many cases, the length of the motor, making it more compact, and in others, achieving higher horsepower, both in the same footprint.”
Motor distributors in the US are seeing an increase in sales of the copper rotor motor, especially with the intensified focus on energy efficiency, according to Jake Balcerzak, In-Plant Sales and Motor Product Manager for KJ Electric in Syracuse, New York. Mr. Balcerzak says that CRM's are a significant part of their motor sales, and growing year-over-year.
In addition to standard induction motor applications, the CRM drives electric vehicles, from sport cars to military vehicles such as the 300 horsepower 100-pound engine in the Tesla Roadster, to the multiple CRMs used in the design of the US Army’s HEMITT A3 heavy expanded mobility tactical truck.
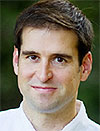
JB Straubel, Chief Technical Officer, Tesla Motors.
JB Straubel, Chief Technical Officer for Tesla Motors sees the CRM as an excellent choice for electric motor driven vehicles because of their horsepower to weight ratio. "To us, it is a huge advantage to have a basic material structure for the motor that we can procure locally, and not be dependent on other regions or other countries that might limit or curtail supplies of these materials. We can actually spin that copper rotor up to 14,000 RPM, so we get a lot of horsepower in a very tight package, by spinning those high RPMs with very precision balance – it's quite a machine.”
Rich Schafer, Marketing Manager at Baldor Electric Company, a member of the ABB Group, Greenville, SC, echoes this same enthusiasm for the Copper Rotor Motor. "Copper Rotor Motors are unique from the standpoint that they allow us to make motors that are very efficient, and a motor that is more efficient runs cooler. You're going to be able to spin that rotor faster, so you can get a lot more horsepower into a smaller package and then gear it down accordingly."
Copper Rotor Motor Advantages
- Efficiencies higher than NEMA MG1 Table 12-12 and EISA 2007 requirements
- Inverter duty capable
- High reliability
- Constant torque capability
- Cool running
- Lower maintenance cost
- lower cost of ownership (power costs)
- Lower vibration with precise and better-balanced rotor
- Mostly the same product lines as the standard induction motor
Copper Rotor Motor Disadvantages
- Higher initial purchase price
- High volume, stocked motors are limited to 20-hp or below for cast rotor
- Limited availability of casting machinery
- Cost of copper somewhat higher that other materials
- More complex processing procedure
Copper Rotor Motor Applications
- All standard induction motor applications : light to severe duty
- Consumer and Military Electric Vehicles
- Petrochemical, paper processing, and refining
Summary
Each of these motor technologies, permanent magnet, switched reluctance and copper rotor induction motor, in their own unique way rely on copper in their design to produce motors that are more efficient, and more reliable. The PM motor with powerful permanent magnets in its rotor, the SRM with power electronic switching and its copper dense stator and rotor, and the CRM with the current-resistance-reducing cool running rotor, all provide options to accomplish energy reduction objectives and improve performance. Through the innovative use of copper, switching technologies and permanent magnets, customers today have more choices to achieve their efficiency and application specific requirements.
Back to TopThe Principals
CDA acknowledges and thanks these motor manufacturing experts in the creation of this case study. We cited the following individuals in this publication:
Rob Boteler, Manager of Government Relations Nidec Motor Corp, St. Louis Missouri, rob.boteler@nidec-motor.com.
John Caroff, Marketing Manager, Low-Voltage Motors, Siemens Industry, Inc. Norwood, Ohio, john.caroff@siemens.com.
Helmuth Glatt, Vice President of Engineering, NIDEC Motor Corporation, Industrial Motors and Systems Division, St, Louis Missouri, helmuth.glatt@nidec-motors.com.
John Malinowski, General Product Manager, General Purpose & Severe Duty AC Motors, Baldor Electric Company, a member of the ABB Group, Fort Smith, AR., john.malinowski@baldor.abb.com.
Oscar Palafox, USA Product Manager Low Voltage IEC Motors, Siemens Industry, Inc., oscar.palafox@siemens.com.
Rich Schafer, Marketing Manager, Baldor Electric Company, a member of the ABB Group, Greenville, SC., rrschafer@baldor.com.
Footnotes
-
The Acoustical noise can be an issue with SR products, but minimization of noise is possible through careful design of the motor and its control algorithms, together with careful mechanical integration in the target application. Understanding the application in general and especially the motors duty cycle and load characteristics is important to SR applications.