Download PDF Version [1.55 Mb]
- Introduction
- Motor Repair Specifications
- Motor Service Centers
- Preventive and Predictive Maintenance
- Preventive Maintenance
- Bearing Considerations
- Predictive Maintenance
- Performance Trending
- Summary: Motor Repair and Maintenance
This three-part series focuses on reducing energy cost and downtime by instituting a motor management plan. Part III, the last in the three part series, addresses repair specifications and preventive and predictive maintenance. Part I addressed creating a motor inventory, and repair/replace guidelines. Part II addressed the establishment of a motor failure policy and the development of a purchasing specification.
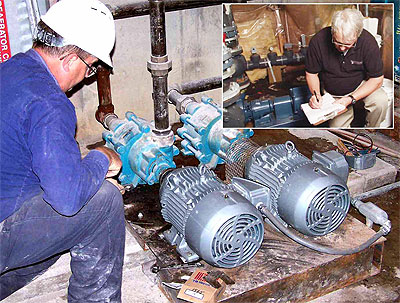
Introduction
This three-part series on motor management best practices focuses on the importance of instituting a motor management plan as a necessity in effectively administering the electric motors in a facility. The goal of a motor management plan is to take advantage of opportunities for energy savings and increased productivity using energy efficient, reliable motors such as NEMA Premium® efficiency motors, herein referred to as "premium efficiency" motors.
Part I of this series addressed conducting a motor assessment for a specific facility, which is a key step in instituting a motor management plan; the steps for conducting a motor inventory; and the motor repair/replace guidelines. Part I also covered how to gain management buy-in through demonstration of the financial gains available through good motor management.
Part II demonstrated the importance of developing a motor failure policy enabling definitive actions that minimize the impact of costly downtime and business interruptions when a motor failure occurs; and the need for a motor purchasing specification as the blueprint for facilitating the process of purchasing new motors. It covered new technologies such as the ultra-efficient copper rotor motor; tools to help identify commonly used motors in your facility and how many to stock; and tools to use to assess which motors are most efficient at yielding the highest energy savings and shortest time to payback.
Here, Part III addresses proper motor repair specifications and preventive and predictive maintenance plans.
Back to TopMotor Repair Specifications
Four major standards cover the design and manufacture of electric motors; these same sources and standards serve as the sources and references for motor repair specifications and guidelines.
- Electrical Apparatus Service Association: EASA Standard AR 100-2010 Recommended Practices for the Repair of Rotating Electrical Apparatus
- The European Standard, International Electrotechnical Commission: IEC 60034 Rotating Electrical Machines
- National Electrical Manufacturers Association (USA): NEMA MG 1 Motors and Generators
- Underwriters Laboratories (USA): UL 1004-Standards for Electric Motors
Another useful reference is the Model Repair Specifications for Low-Voltage Induction Motors (PDF 1.3 MB), which is published by United States Department of Energy's Advanced Manufacturing Office (AMO) and was authored by Johnny Douglass, retired Senior Industrial Engineer with the Washington State University Energy Program. It covers the routine repair and the rewind of low-voltage, random wound, three-phase AC, squirrel-cage induction motors. The "Model Repair Specifications" for low-voltage motors contains a detailed set of motor repair procedures. Here is a sampling of its content:
- Documentation: The repair form is the guide for the repair. The person requesting the repair first fills out the form with information about the problem and the form is subsequently maintained by the repair facilities. This form serves as the paper trail for that motor throughout the repair process.
- Incoming inspection: This describes the initial tests or root cause analyses necessary to determine the cause of the motor failure. The tests include visual inspection, testing of the winding insulation, evaluating the bearings, and a no-load run test if possible.
- Dismantling: Part of the failure analysis involved dismantling the motor. Related topics include how to properly mark the motor's end-bells before removal; how to store the parts and identify them with the motor; noting the bearing insulation requirements and associated resistance tests; care required for working with explosion proof motors; and care necessary for rotor removal.
- Vertical motors: Motor service centers are cautioned to refer to the manufacturer's instructions when repairing vertical motors. Measurements such as rotor lift end-play are critical and they need to be recorded.
- Winding removal: This section is about collecting data on the winding configuration. It describes the core loss tests that are conducted before and after insulation stripping and iron repair; sets limits on hot spot temperatures and core-loss tolerances; and covers winding burn out procedures as well as temperature and time limits.
That's just a sampling of a few of the specifications that could be examined. Additional line items for model repair specifications are as follows:
- Core preparation
- Rewinds
- Routine overhauls
- Rotor test and repair
- Shaft repair
- Anti-friction bearings
- End brackets
- Balancing
- Reassembly
- Final tests
- Quality control
The " Model Repair Specifications" publication from the DOE is available free of charge.
Back to TopMotor Service Centers
Membership in EASA
Being an EASA member has its benefits. As an international trade organization with close to 1900 members in 59 countries, EASA strongly encourages its members to represent the electrical apparatus sales and service industry with the highest quality of business integrity, ability and service by meeting a code of business practice guidelines.
EASA also provides its membership with access to engineering and educational programs, providing up-to-date information on materials equipment and technology. Members have access to courses or seminars such as Mechanical Repair Fundamentals of Electric Motors and the CD series, How to Wind Three-Phase Stators.
Kitt Butler, Director of Motors and Drives at Advanced Energy, said, "There are many factors to consider when choosing a motor service center. Being a member of EASA is certainly a plus. Its staff in St. Louis helps with all types of technical questions; they support their members through workshops, online webinars, and technical resources. EASA is a great organization. Look for an EASA member when choosing a shop for your motor repairs."
Service Center Quality
The value of a good motor repair specification depends on the quality of the motor service center. Finding good motor service centers requires diligence. Develop a set of criteria before you begin to audit a motor repair facility. Advanced Energy offers some guidelines in its Horsepower Bulletin (PDF .5 Mb) as follows:
- Is the facility's equipment in good condition?
- Is the facility in compliance with safety requirements, neatness and housekeeping?
- Are records and files well organized?
- Are employees knowledgeable and satisfied at work?
- Does the facility keep a variety of wire sizes and shapes in stock? (Look for half and full sizes if you have foreign motors.)
- What is the purpose and frequency of use of the test equipment?
- Does the facility comply with industry standards for motor repair quality and other specifications?
- Check the facility's compliance with standards and procedures published by EASA.
- Does the facility have an active quality assurance program?
For more information on this topic, visit the Knowledge Center.
On selecting a motor service center, Kitt Butler says, "There are many things to look for in a motor service center's guidelines. Look for the types of materials and equipment that the shop uses, the calibration procedures for its measuring equipment, the quality of its personnel and the experience and training its personnel. All play a critical role in delivering a good quality repair that maintains efficiency."
Evaluate Over Time
When choosing a motor service center it is also important to do your evaluation over time. Don't base the evaluation just on a single visit and one set of measurements. Provide your repair vendor with the specification and measure them against that specification over time. Some motors service centers create their own guidelines using a standard such as the EASA Standard AR 100-2010. You can audit a service center against its own guidelines if you haven't developed your own.
Original Efficiency
How important is it to restore an electric motor to its original efficiency? Since the cost to repair a motor may be a small percentage of the cost to operate that motor over several years, the motor efficiency when returned to service should be as close as possible to the efficiency it had when new. Many motors operate 40 to 80 hours per week or more, so even small increases in efficiency can yield huge energy savings.
The following standards and best practices cover motor repair, motor efficiency and quality assurance programs. They are available as free downloads at EASA.
- ANSI/EASA AR 100-2010: Recommended Practice for the Repair of Rotating Electrical Apparatus
- The Effect of Repair/Rewinding on Motor Efficiency
- Guidelines for Maintaining Motor Efficiency during Rebuilding
- EASA-Q: 2000 Quality Manual (purchase item)
Service Center Capability
A motor service centers can verify its capability to return a repaired motor to its original efficiency. The decision to repair a motor is often based on the motor's pre-failure efficiency; a significant decrease in efficiency would increase energy costs and perhaps rule out repair. A motor service center can be accredited for its ability to restore a motor to its original efficiency. Proven Efficiency Verification (PEV) is a quality assurance program offered by Advanced Energy, which mutually benefits both motor repair purchasers and providers. The PEV program includes an on-site audit on the use of best practices to bring the service center into conformance. Following the audit, a control set of motors are pretested, damaged and submitted to the service center for repairs. Service centers meeting the program requirements receive certification.
Mr. Butler adds, "Returning a repaired motor to its original efficiency is important and can be done. We have proven many times that you can maintain efficiency when a motor is repaired. We promote motor repair companies that have demonstrated quality assurance programs that maintain efficiency when a motor is rewound." Details of the PEV program and a list of the currently accredited motor service companies are online at Advanced Energy.
Pre-EPAct Motors
No matter the quality of repair, a pre-EPAct motor will never be as efficient as a new, premium efficiency motor. The design of the original motor is the contributing factor. Bruce Benkhart, director, Advanced Proactive Technologies, Springfield, Massachusetts, commented, "When rewinding or repairing a motor there are a number of things to consider. An older motor that is inefficient might look repairable. However, the best new technologies and the best practices in rewinding can only restore a motor to its original specifications. If it started life as a pre-EPAct lower efficiency motor then that's the best you're going to get back, no matter the quality of the repair work."
Build a Relationship
Build a strong relationship with your motor repair vendors! Pressuring your motor service center to rush a repair is never a good practice. A good motor service center adheres to a specific set of guidelines in the motor repair process. Look for a motor service center that adheres to the EASA guidelines. The risks of motor damage and losses of efficiency are too great. A good motor service center will strongly advise against rushing a motor repair. Mr. Douglass explains, "It's important to understand the viewpoint of your repair facility. There are only a few ways to do it right but many ways to do it wrong. Demanding they do the job fast is the wrong approach because there are so many ways to cut corners. These shortcuts could get a motor repaired or rewound faster but most of these methods to accelerate the process also degrade efficiency and reliability. Good planning and a sufficient quantity of spare premium efficiency motors will allow you to avoid such situations. You can put a new spare in place and have ample time to rebuild the failed motor and return it to spares with minimal downtime."
Back to TopPreventive and Predictive Maintenance
Differences Between PM and PdM
Preventive and predictive maintenance are distinct activities with the same goal: Maintain the production equipment and plant utility systems equipment in the best possible operating condition for their intended purpose. In general, preventive maintenance occurs during equipment shut down and predictive maintenance occurs when the equipment is running in normal operating mode. The former keeps equipment working, and the latter identifies and corrects potential problems during a non-disruptive time. Johnny Douglass says, "Preventive maintenance is more familiar to most people; it's been done since as long as there have been motors. Predictive maintenance is analogous to what happens in a modern doctor's office. The doctor does not just reactively treat serious conditions but rather tests for hidden indicators such as blood pressure and cholesterol and corrects them before something serious happens such as a heart attack or stroke. Modern electrical instrumentation allows you to see a lot more about what is happening and developing inside a motor than you could in the past. Using these instruments, you can anticipate a failure condition before it happens and intervene with corrective actions."
Skills and Responsibilities
Who does the work? Someone with a high level of maintenance, plant or facilities engineering experience writes the documentation that describes each task. Such a person would understand many aspects of electric motor systems: aging characteristics, impact of contaminants, temperature extremes, moisture, corrosives contact, vibration, lubrication, and use of instrumentation.
The tasks require skilled mechanics and electricians. The majority of work requests are for inspection and only a small percentage are for lubrication, despite the importance of the latter. Those performing the tasks must have a detailed understanding of the equipment so that they can effectively inspect and correctly evaluate problems.
Those directly responsible for managing the mechanics and electricians must also understand the preventive and predictive maintenance. The manager should have sufficient skills to participate in the system's failure analysis and direct the actions to prevent future failures. Upper management must support the preventive and predictive maintenance programs as necessary and important functions in the production process. They will be called on to authorize planned downtime of equipment, to implement the maintenance programs.
In addition to the technically skilled maintenance personnel, production employees can participate in a preventive maintenance program. Those closest to the working systems are the most likely to notice changes in equipment operation; they could be trained to perform inspection and lubrication tasks.
Equipment suppliers can contribute to any preventive and predictive maintenance program. They tend to be more knowledgeable about their equipment and often have advanced skills, especially true in the use of predictive maintenance instrumentation. As a major motor distributor with five locations across New York State, KJ Electric provides its customers with many services, including laser alignment, full-spectrum vibration analysis, thermography analysis, dynamic balancing and shaft voltage testing.
Kenneth E. Jacobs, CEO, KJ Electric points out, "We offer our customers thermography imaging for their motors and motor systems. This service can identify hotspots in the motors and power systems as a predictor of early failures. The results of the thermography analysis point to preventive maintenance actions that could circumvent a failure."
Preventive Maintenance
Preventive maintenance is maintenance performed on electrical motor systems at scheduled intervals. PM is necessary to optimize motor life. The timing of the intervals depends on the known reliability or failure rates of the motor components in the operating environment. Dirty or corrosive environments mandate frequent PM actions. Most industrial facilities have some form of a preventive maintenance program.
Rick Scott is Assistant Director of Facilities Operation at St. Lawrence University in Canton, New York. This private university comprises 70 buildings and enrolls about 2300 students. The school owns hundreds of motors with horsepower between 1 and 50. Many drive pumps and air handlers, and many have variable speed drives. "At our facility, we've done quite a bit to save energy. We have a preventive maintenance program with one person dedicated to that task. The program entails regular servicing of our air handlers, pumps and drives; as well as replacing belts and filters. Normally, we will replace a motor larger than one horsepower with premium efficiency motor whenever it fails so long as it is not a candidate for repair. Sometimes we replace older motors that are still running with premium efficiency motors; for example whenever a pump fails, we just replace the whole system. Premium efficiency motors tend to have higher reliability. We try to increase efficiency and save on electrical costs."
Bearing Considerations
Lubrication
Proper bearing lubrication is one of the tenets of a preventive maintenance program. Bearing failures account for a significant portion of the mechanically related problems. See the sidebar on "Most Frequent Motor Failure Areas."
If you only detect bad bearings by noise or vibration then you will always be too late. At that point, mechanical damages to the bearing raceways and perhaps even the motor shaft have already happened; and you have already incurred extra energy costs by operating the motor with increased frictional load to the motor. Mr. Butler fully acknowledges the importance of lubrication in a preventive maintenance program. "Preventive maintenance is important for electric motors," he says, "and lubrication is probably the most important aspect of PM. Make sure you have the proper type of grease and apply the proper amount in a motor on its regularly scheduled intervals."
Bearings do not necessarily wear out but they do fail, and lubrication issues are a major factor in bearing failure. According to a white paper on bearing failure published by Applied Industrial Technologies, improper lubrication accounts for 40 to 50 percent of bearing failures; improper bearing installation for 25 to 30 percent; and other causes account for 20 percent of bearing failures. Achieving the natural fatigue limits of the bearing accounts for less than one percent of bearing failures! With proper preventive maintenance, bearings should outlast the useful life of the motor. See the Bearing Failures - Causes and Cures white paper.
Lubrication in anti-friction bearings prevents metal-to-metal contact between the rolling elements, the raceways and retainers. The lubricant also provides protection against corrosion and wear, dissipates heat, and acts as a barrier to keep out solids and liquid contaminants. The anti-frictional properties of the lubricants allow the motor to run much more quietly. Yet, bearing lubricants break down over time and therefore need periodic replenishment. Use the lubricants approved by the manufacturers and follow the manufacturer's specifications for the correct application of the lubricant.
Motor Shaft Grounding
Variable frequency drives (VFDs) can cause bearing failures by inducing currents in motor shafts. This problem is specific to VFDs and affects both AC and DC motors. Considering how they can save energy and lower operating costs, VFDs are increasingly used for process control, pumps, air handling, conveyers, spindles and many more applications. As the drive switches on and off, speed variations cause voltage buildups that seek a ground potential. Oftentimes, the most direct path is through the bearings. The bearing lubricant can act as an insulator but the lubricants resistive properties will eventually break down, and the resulting electrical current flow pits the metal surfaces and the bearings eventually fail.
Fortunately, solutions to this problem do exist. According to Gilbert A. McCoy, P.E., Energy Systems Engineer, Washington State University Energy Program, "Currents induced in a motor shaft and grounded across the bearings cause fluting, which is a type of bearing damage. To eliminate fluting, consider installing a shaft grounding brush and/or insulated bearings so that the currents do not form and flow across the bearings raceway." Other solution options include hybrid ceramic bearings, and line reactors or filters. Fluting can occur regardless of the efficiency class of the motor, whether premium efficiency, energy efficient, or standard.
Back to TopPredictive Maintenance
Predictive Maintenance Programs (PMPs) are gaining acceptance as method for maintaining motor reliability. A well-rounded program includes as many technologies as practical; each technology contributes a significant factor to the diagnostic analysis. The scheduled static test and the more-aggressive dynamic test are both useful in the prediction of a potential motor systems failure.
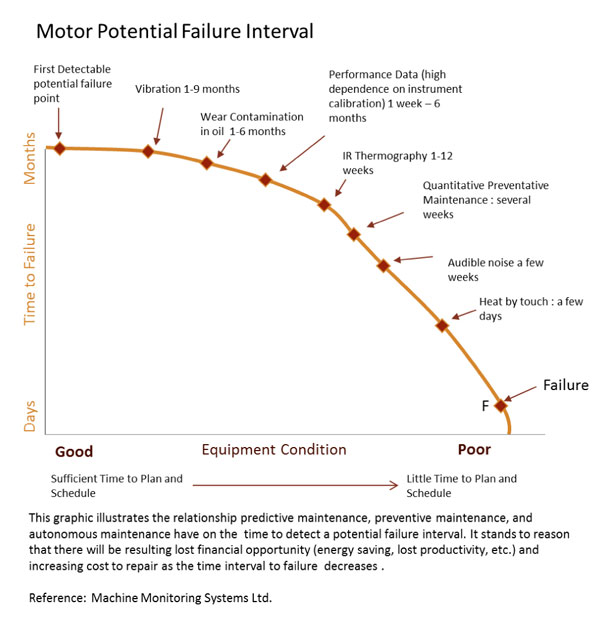
Advantages & Disadvantages
Predictive maintenance programs can be expensive but they provide real benefits. The main advantage is expressed as follows on the website of the Department of Energy. According to the DOE, "A well-executed program can almost eliminate catastrophic equipment failure because issues are identified and eliminated prior to any significant system deterioration."
Such programs save time and energy in other ways, too. The following average savings are typical within industrial settings:
- Return on investment of up to 10X
- Maintenance costs reduced by 25 to 30 percent
- Elimination of breakdowns by 70 to 75 percent
- Downtime reduction of 35 to 45 percent
- Production up by 20 to 25 percent
Advantages include the following:
- Allows preemptive corrections
- Increased system reliability and lifespan
- Decreased equipment or process downtime
- Decreased costs for parts and labor
- Better product quality
- Improved safety
- Energy savings
- Estimated 8 to 12 percent cost savings over preventive maintenance
Disadvantages include the following:
- Increased investment in diagnostic equipment
- Increased investment in staff training
- Savings potential is not readily seen by management
For details, see U.S. Department of Energy.
Back to TopPerformance Trending
When conducted periodically, predictive maintenance lends itself to performance trending. Equipment issues needing maintenance show up as abnormal performance trends. Once you establish your motor management plan and complete your motor inventory then the findings of predictive maintenance can be added to the motor inventory database. Mr. Benkhart says, "Many facility managers want to inventory every motor not only for an energy assessment but also for the backbone of a maintenance program. Predictive maintenance measurement results are entered into MotorMaster+ and become part of the record. Anyone knowledgeable of the metrics can follow the trends of the equipment."
You cannot predict when equipment will fail; you can only assess the potential for failure. Mr. McCoy says, "Predictive maintenance involves taking periodic measurements, trending those measurements, and knowing when a motor is starting to show signs of deterioration. This data and knowledge enables the maintenance staff to intervene before the motor fails. Some plants prefer the term "condition assessment" rather than the term "predictive" because management may assume they can predict when something is going to fail. "
Mr. Douglas was asked, "If you cannot predict when a failure will occur, what should you do?" He responded, "When a motor analyzer is used in a predictive maintenance program, typically the results are used to assign a condition status to a motor like red-green-yellow: green means the motor is okay, yellow means there are signs of deterioration, and red perhaps means replacing that motor at the nearest possible opportunity. As a motor shows signs of deterioration, you might put it on a watch list, take measurements more frequently and be prepared to intervene before the motor actually fails. These watch lists are useful because they inform management about the health of the motor population in the plant. Remember, the goal of predictive maintenance is to increase uptime, decrease failures, improve reliability, and ultimately increase plant productivity."
Predictive Maintenance Technologies
There are several predictive maintenance technologies:
- Thermography or infrared imaging can generate a visual image, which shows variations in the infrared radiance on the equipment surfaces. It is useful in identifying hotspots because of poor electrical connections or poor air circulation.
- Lubricant and Wear-Particle Analysis is also known as oil analysis. The lubricant condition is useful in determining if maintenance is required.
- Ultrasound analysis is similar to thermography, but uses sound waves to image internal systems, enabling the detection of system wear, leaks or failures.
- Vibration analysis seeks to identify system degeneration exceeding permissible levels. Abnormal levels indicate excessive system wear or equipment misalignment.
- Motor analysis includes several test measures that are used to identify such issues as winding short-circuits, open coils, incorrect torque limits and mechanical problems inside a motor.
One such motor analysis tool is the power quality analyzer (PGA). It provides extensive capabilities for recording and trending power quality events. Several power quality analyzers are available and they vary in price and features.
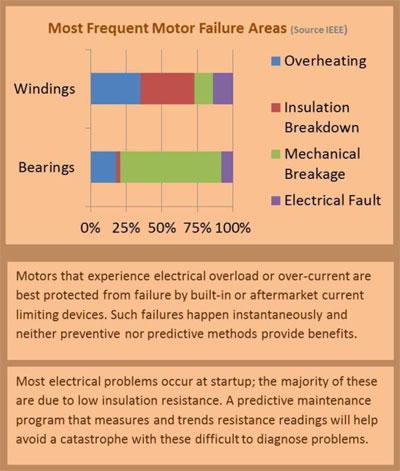
Regarding PQAs, Anthony J Simon, Energy Engineer at Washington State University, says, "The power quality analyzer (PQA) provides the highest level of sophistication in data collection for determining motor load inefficiencies. The inputs are voltage and current. The voltages for all phases are live measurements from the operating motor. The current is a nonintrusive measurement using a current transducer, or CT, with clips that wrap around the conductors. From these measurements, the PQA records the motor load at different times during the operating process. The power quality analyzer not only measures true kilowatt power, it measures harmonics, and it can give useful information on voltage unbalance and other aspects of motor operation."
Spending Decisions
The potential for a system failure tends to be inversely proportional to predictive maintenance put into a system; however, predictive maintenance can be expensive so a well-planned application is recommended. A good understanding of your motor inventory and a proper identification of the systems most critical to your plant or facility allows you to decide where to best spend your predictive maintenance dollars.
As Mr. Butler explains, "Old-timers just walked through the facility using their eyes and ears as the only predictive maintenance program available. They had strong intuitions about what was going to happen to a motor long before it failed. For example, they could often "sense," without explaining how, whether it was a bearing or a misalignment issue. Thankfully there is lot more science out there today in terms of current signature analysis, and there are a lot more tools available to really analyze motors. PdMA, Baker and All-Test Pro make or distribute signature current analysis tools that dramatically assist with predictive maintenance today."
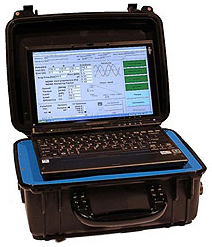
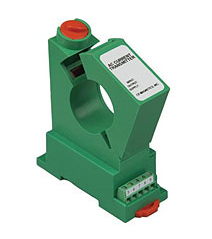
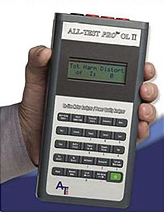
For more information, visit the following websites:
PdMA Corporation
SKF USA, Inc.
All-Test Pro
CR Magnetics
Summary: Motor Repair and Maintenance
A motor repair specification along with preventative and predictive maintenance aims at ensuring quality repairs, long motor life, minimal downtime and energy savings.
The best assurance of repairing a motor to its maximum energy efficiency is a well thought out and documented repair specification built on use of technical resources and membership in trade organizations as well as a well-developed relationship with an accredited electric motor service center.
Establishing and adhering to an electric motor preventative maintenance program, augmented by periodic predictive maintenance, is the best insurance for the longevity and efficiency of a facility's motor systems. If your facility does not have the staff or requires either training or direct services for preventative and predictive maintenance, contact your local electric motor service center for assistance.
Note
The US Department Energy has implemented new websites, eia, Energy Information Administration and the Advanced Manufacturing Office. At the time of this writing the current links to DOE articles in this publication continued to be applicable.
Acknowledgements
CDA acknowledges the help of government- and industry-based motor experts in the creation of the Motor Management Best Practices series. The following individuals were cited in this publication.
Bruce Benkhart, Director, Advanced Proactive Technologies, Springfield, Massachusetts. Mr. Benkhart can be reached at (413) 731-6546 bruce@appliedproactive.com
Kitt Butler, Director, Motors and Drives at Advanced Energy Corporation (AEC), Raleigh, North Carolina (919) 857-9017, kbutler@advancedenergy.org
Johnny Douglass, Retired Senior Industrial Engineer, Washington State University (WSU) Extension Energy Program. (360) 956-2086, douglass.johnny@gmail.com.
Gilbert A. (Gil) McCoy, P.E. Energy Systems Engineer with the Washington State University (WSU) Energy Extension Office, Olympia, Washington. Mr. McCoy can be reached at (360) 956-2086, mccoyg@energy.wsu.edu
Anthony J. Simon, Energy Engineer, Washington State University (WSU). (360) 956-2141, SimonT@energy.wsu.edu