Download in PDF format [226 Kb]
- New Motors, New Savings
- Improving Motor Efficiency
- Total Motor Program
- Rebuild or Replace?
- Rebates: Nice, But Just Icing on the Cake
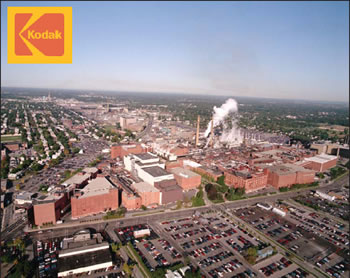
Kodak Park, the international photo giant's main research and manufacturing facility in Rochester, New York, is one of the worlds leading industrial technology centers. (Top photo). And one of the largest, as well: the 100-year-old complex covers eight square miles, contains 20 million square feet of buildings, hundreds of miles of roads and 22 miles of railroad track. Two power plants with a combined capacity of 200 MW generate most of the electrical energy the facility consumes annually.
With such a visible presence in the community, Kodak naturally places environmental concerns and energy savings among its top corporate
priorities and it addresses them aggressively. The company recently reduced its carbon dioxide emissions by 16% and is on the way to cutting its energy usage (indexed to production) by 15%. For those accomplishments, the U.S. Environmental Protection Agency recently presented Kodak with its 2003 Energy Star Corporate Commitment Award for excellence and voluntary leadership in reducing greenhouse gas emissions through strategic energy management. Kodak is cutting energy consumption by applying a lot of smart engineering, but a large portion of the savings comes as the result of a company-wide program that focuses on its electric motors.
New Motors, New Savings
As Kodak and many other companies have learned, longterm savings (and short-term paybacks) happen when old, standard-efficiency motors are replaced with modern NEMA Premium models. In a nutshell, the new motors use less energy and cost less to operate for an equivalent amount of work. Theyre also designed and built to higher standards than older motors, and they run cooler, good indications theyll probably last longer with less maintenance.
Why are premium motors more efficient? Mainly, its because they contain about 20% more copper. More copper means lower resistance, and lower resistance means lower I²R losses in the stator coils the largest single source of wasted energy.1
Kodaks decision to invest in premium-efficiency motors whenever practical is based on two well-documented facts:
- Nationwide, according to the U.S. Department of Energy, motor-driven equipment accounts for nearly two-thirds of total energy consumption in industrial facilities such as Kodak Park. Since motor-driven systems are the largest energy users, theyre also the best place to look for the largest savings.2
- The cost of a new motor is insignificant compared with the cost of the power it consumes.
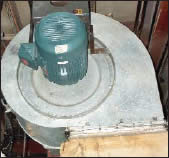
But suppose that, instead of buying that NEMA Premiumefficiency unit, the owners had spent about $1,000 to rebuild their old standard-efficiency motor. Thats a savings of nearly $700, right?
Wrong. The rebuilt motor would have continued to operate (probably not for 20 years, but lets assume it does) at 91.1% efficiency, having lost 0.5% as a result of the rewind.4 The motor will now consume 184,163 kWh/year at a cost of $13,812, or $545 more per year than that for the NEMA Premium motor. Those $700 in up-front savings will have gone the way of the dodo bird in a little over one year, and after 20 years, the old motor will have cost its owners almost $11,000 extra in unrealized energy savings.
And, if environmental concerns are as important to your company as they are to Kodak, consider that switching to NEMA Premium-efficiency motors can reduce carbon dioxide emissions. For example, the 20-hp blower motor (Figure 1) saves over 5400 pounds of CO² per year.
Kodak Park operates several large shops that rebuild hundreds of motors each year for Kodak facilities around the world (Figure 2). Just like commercial rebuilders, Kodak is a member of the Electric Apparatus Service Association (EASA) and is certified by both Reliance Electric and Underwriters Laboratories, so the work Kodaks shops do is as good as it gets.
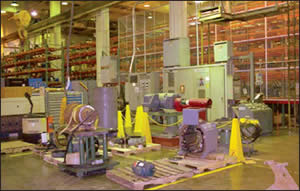
But Kodak doesnt expect to save energy by rebuilding its own motors, because even the best rewinding job can never increase a motors efficiency beyond what it was when the motor was new. In fact, sometimes efficiency drops by between one-half and two percentage points when a motor is rebuilt. So, instead of creating savings, the money spent on rebuilding an old motor could actually increase the motors energy consumption and operating costs from that point on.
Back to TopImproving Motor Efficiency
A nationwide push toward efficient motors began more than 10 years ago when President George H.W. Bush signed the Energy Policy Act of 1992, or EPAct, as it is commonly called. The law mandates that certain types of motors sold in the USA after October 24, 1997, must meet or exceed minimum electrical efficiency standards as published in (National Electrical Manufacturers Association) NEMA MG 1-1993, Table 12.10. Nominal efficiencies of these so-called EPAct motors are between one and four percentage points higher than those of standard-efficiency motors. Motors that met or even exceeded EPAct standards were available long before the law was enacted, but the law simply made compliance with those standards mandatory for all newly produced motors of the types covered by the Act.
While EPAct motors did represent a significant improvement in efficiency, top marks today go to motors that meet NEMA Premium efficiency standards, or better. These standards are listed in NEMA MG 1-1998 R3 Tables 12-12 and 12-13. Nominal full-load efficiencies of NEMA Premium-rated motors are between one and two percentage points higher than those of EPAct motors, and the NEMA Premium designation applies to more horsepower sizes than EPAct.
Premium-efficiency motors often pay for themselves in as little as one to two years, after which the savings just keep accumulating. For example, Table 1 compares annual energy consumption and cost for a few common sizes of standard-efficiency and NEMA Premium motors. The table also lists simple payback times and 20-year return on investment (ROI) for the cost of a premium motors vs. rewinding and continuing to operate a standard motor. The data are taken from MotorMaster+, an easy-to-use cost analysis program prepared for the DOE by the Washington State University Energy Program. The software is available by request at AMO Tools Help Desk.
hp | Standard-Efficiency Motors | NEMA Premium™- Efficiency Motors | Saving by Installing A NEMA Premium™ Motor | Payback Period, ROI |
---|---|---|---|---|
Efficiency at 75% of Full Load, Rewound (Avg. %) Annual Energy Cost, 600h at 75% of Full Load, $0.075/kWh |
Nominal Efficiency at 75% of Full Load (Avg. %) Annual Energy Cost, 6000h at 75% of Full Load, $ $0.075/kWh |
Annual Over 20-y Life |
Simple Payback: NEMA Premium Motor vs. Cost of Rewinding and Operating Standard Motor, Years 20-y Life, After-tax ROI % |
|
10 | 85.7 $2,939 |
91.8 $2,742 |
$197 $3,940 |
1.09 210.6 |
25 | 88.9 $7,079 |
93.8 $6,709 |
$370 $7,400 |
1.86 78.2 |
50 | 91.1 $13,812 |
92.9 $13,267 |
$546 $10,920 |
2.43 55.1 |
100 | 91.7 $27,450 |
95.5 $26,353 |
$1,097 $21,940 |
2.58 51.4 |
200 | 92.8 $54,286 |
94.5 $52,290 |
$1,996 $39,920 |
3.09 42.0 |
*Calculations were prepared using MotorMaster+ 4.0, and assume average efficiencies and average purchase (35% dealer discount) and rebuilding costs for standard and NEMA Premium motors, 6,000 h/y operation at 75% of full load, $0.075/kWh utility rate. Life-cycle ROI further assumes 5% escalation rates for cost of capital, annual O&M, fuel, energy and demand charges, 10% interest rate, 18% discount rate, 35% corporate tax rate, 5-yr depreciation. |
Total Motor Program
The key element of Kodaks energy-saving efforts is a company-wide Total Motor Program. Its guidelines are straightforward: reduce energy use through the installation, whenever possible, of NEMA Premium-efficiency motors. The program has the strong backing of top management, an important point according to Al Lopa, who represents Kodaks Corporate Energy Office. This company is totally committed to the environment, he reminds us. And, our Total Motor Program is the proactive part of that commitment. The program is also a very large undertaking, since we operate or inventory between 70,000 and 90,000 motors at any given time.
Its not just lip service. We formed a rotating-equipment team that includes motor and equipment suppliers along with Kodak managers and maintenance personnel. The team meets as often as once a week with our vendors to resolve any motor issues that might have arisen and forestall those that might come up. In some cases, the company even made seed money available to help managers replace old motors. And, we get our people involved. The maintenance guys attitude is, Whats in it for me? The Total Motor Program attempts to answer that.
The program has been in place for several years, but interest in high-efficiency motors at Kodak extends back at least to the 1980s. Today, the programs centerpiece is the deliberate replacement of unserviceable standard-efficiency motors with NEMA Premium models whenever possible.
Back to TopRebuild or Replace?
But what about those rebuild shops; are they no longer needed? Bob Steele, who coordinates the motor program at Kodak Park, explains: Although we repair and rewind between one and two percent of our motors annually, about 30 percent of that work involves DC vehicle motors for forklifts and such. Premium-efficiency models for that type of motor arent commercially available, so theres still plenty of work for the shops to do. Also, about 5 percent of our motors are special-purpose types, and we have many foreign-made motors in our international facilities. Neither NEMA Premium nor the older EPAct standards apply to those units. We are trying to phase out the specials and convert to motors that are available as NEMA Premium units, but thats not always possible, especially overseas.
But the Total Motor Program policy is very clear when a general-purpose or other non-special motor fails, says Steele. When one of those motors smaller than 20 hp fails, we always replace it with a motor that meets or exceeds NEMA Premium efficiency standards. For larger general-purpose motors, we analyze the costs using MotorMaster+, and well upgrade to NEMA Premium whenever the payback is reasonably short. Corporate policy calls for 24-month paybacks, but we like to shoot for 12 months or less, and we can often get it.
Following that policy has already saved Kodak more than $250,000 per year in energy costs, and thats just based on an initial sampling of motors that were replaced to test the programs effectiveness. Steele and his team are now in the process of inventorying a larger number of motors and developing plans that will let them upgrade to NEMA Premium models in the most cost-effective manner. Scheduling is a major factor because many processes run 24/7, and finding sufficient downtime to replace a motor is always a consideration. We wait for a down cycle, says Steele. Then, we go in and replace the motor.
Back to TopRebates: Nice, But Just Icing on the Cake
Kodak participates in an incentive program administered by the New York State Energy Research and Development Authority (NYSERDA). Among its many other activities, NYSERDA makes rebates available to any New York State company willing to improve its energy posture through the installation of more-efficient systems or equipment. As with similar programs in other states, funding is underwritten by a systems benefits charge on all utility bills. Installing (or upgrading to) NEMA-Premium-efficiency motors qualifies for a rebate, which is credited to the purchaser. The motor supplier, usually an electrical distributor, receives a separate incentive. Since Kodak generates nearly all of the power it needs, the companys participation in the NYSERDA program is voluntary, and it definitely isnt the main driving force behind the companys decision to upgrade to premium-efficiency motors.
NYSERDA rebates are icing on the cake says Richard deFay, western New York representative for the Premium Efficiency Motors Program of New York Energy $mart.
Steele adds: Reducing total energy cost and helping the environment by reducing emissions are our main reasons for switching to NEMA Premium equipment. But equally important is the ability to standardize our equipment because it helps simplify training and repair procedures. Standardization is very important, too. It helps control inventory because it lets us reduce both the number of spare parts in stock and the number of stock numbers.
We also reduced the number of vendors. We used to deal with as many as 36 motor suppliers. Now, we work closely with Chris Thornton at Kaman Industrial Technologies when it comes to premium-efficiency motors. We insist on certain special features in our motors, such as severe duty capability and suitability for inverter duty, and the manufacturers Chris supplies meet those requirements and still meet or exceed premium-efficiency standards.
The other big driver at Eastman Kodak is reliability. Were shooting for a minimum 10-year life in our motors and, with normal maintenance, 20 years might be reasonable. The more uptime we have, the better the yield on our processes. Its a little early to tell, but our experience so far suggests we should see higher reliability with premium efficiency motors. Along with lower energy bills, higher reliability helps control the cost of our products, which ultimately benefits the consumer as well as our stockholders!
Lower energy costs, less maintenance, simplified inventory control, fewer vendors and a better corporate environmental image all because of a sound plan that focuses on NEMA Premium efficiency motors. If you ask us, the EPA couldnt have picked a better recipient for its 2003 award.
Back to TopThe Principals
Bob Steele coordinates Kodaks Total Motor Program at the companys Rochester, New York, facility, as well as its many operations around the world. Mr. Steele can be reached at (585) 477-5109 or robert.steele@kodak.com.
Richard de Fay represents the Premium Efficiency Motors Program for New York Energy $mart in the western region of the state. Energy $mart (a NYSERDA program) is administered by Applied Proactive Technologies (APT). APTs clients include utilities and energy agencies for whom they plan, implement and evaluate energy-efficiency programs.
APT is headquartered in Springfield, Mass., and has offices in New York, New Jersey, Massachusetts, Rhode Island, New Hampshire, Maine, Vermont, Illinois, Idaho, Montana, Washington and Oregon.
Mr. de Fay can be reached at (585) 533-2510, richardd@appliedproactive.com. Energy $mart can be reached at (800) 388-9294.Chris Thornton represents Kaman Industrial Technologies, a national distributor of electrical, mechanical, fluid power and bearing products. Mr. Thornton can be reached at (585) 254-8060, fax: (585) 254-8959, chris.thornton-kit@kaman.com; 200 Mile Crossing Blvd, Suite 2, Rochester, NY 14624
Footnotes
For a description of electric motor efficiency, see Sustainable Energy section.
The Department of Energy's Office of Industrial Technology (OIT) is a useful source of information about energy consumption. See
http://www.oit.doe.gov/bestpractices/motors/ for one of several DOE references to the subject. A comprehensive report on industrial energy consumption prepared for the DOE can be found at http://www.oit.doe.gov/bestpractices/motors/utrecht.shtml.Actual motor costs vary with model and manufacturer. Cost and efficiency data were taken from MotorMaster+. See sidebar for details.
According to data generated for the DOE, 91.1% efficiency is the average value for 50-hp standard efficiency motors after rewinding.