Introduction to Copper: Mining & Extraction
Copper Applications in Metallurgy of Copper & Copper Alloys
The Copper Age | The Bronze Age | The Middle Ages and Later | Mining
Copper minerals and ores are found in both igneous and sedimentary rocks. Mining of copper ores is carried out using one of two methods.
- Underground mining is achieved by sinking shafts to the appropriate levels and then driving horizontal tunnels, called adits, to reach the ore. Underground mining is, however, relatively expensive and is generally limited to rich ores. El Teniente, in Chile, is the world's largest underground copper mine.
- Open pit mining is employed when the orebodies are extensive, low in grade, and relatively near the surface, where they can be quarried after removal of overburden. Chile also boasts the world's largest (in terms of output) open-pit copper mine, Escondida. The largest copper mine in North America (and the world's largest man-made excavation) is the Bingham Canyon Mine near Salt Lake City, Utah. A $1.5 billion modernization program completed in 1998 turned Bingham Canyon into North America's lowest-cost copper producer, a model of operational efficiency and environmental compliance.
Copper is found in the earth's crust and the oceans although the amount in the latter is thought to be negligible, amounting to no more than about eight months mine production at present-day rates. The upper 10 kilometers of the crust is thought to contain an average of about 33 ppm of copper. For commercial exploitation, copper deposits generally need to be in excess of 0.5% copper, and preferably over 2%. The known reserves of higher-grade ore in the world amount to nearly 1 billion tons of copper. At the present rate of mine production, which is about 13.9 million tons (12.5 million metric tons) a year, known reserves of copper could be depleted in about 65 years. However, successful exploration for new mineral deposits, technological advances in mining and extractive metallurgy (which enable the exploitation of leaner ores, thereby enlarging the pool of known reserves) and copper uses (which permit copper to be used more sparingly where larger quantities were used in the past) and the continued recycling of scrap are likely to forestall indefinitely depletion of this valuable metal.
For example, in the first mile depth of the crust of the continents, it is estimated that there is 3x 1018 metric tons of copper diffusely distributed. The relatively concentrated portion of this copper is only a small fraction of the whole, constituting an estimated 1010 metric tons in deposits with a grade of 0.25% or more. At current world mine production, this represents a million years' supply of copper theoretically available in the mineable portion of the earth's crust.
Table 4 shows some of the most common copper minerals. Some of these have long had a value in their own right, such as malachite, prized for its unusual and pleasing appearance and used for millennia in jewelry and ornaments.
Mineral | Composition | Wt % Copper | Color | Luster |
---|---|---|---|---|
Native copper | Cu | 98+ | Copper Red | Metallic |
Cuprite | Cu20 | 88.8 | Red | Adamantine |
Chalcocite | Cu20 | 79.9 | Dark gray | Metallic |
Chalcopyrite (Fools' Gold) |
FexCuyS | 10 approx | Gold | Metallic |
Covellite | CuS | 66.4 | Indigo blue | |
Bornite (Peacock ore) |
Cu5FeS4 | 63.3 | Golden brown to copper red |
Metallic |
Malachite | CuCO3Cu(OH)4 | 57.5 | Bright Green | Silky to Earthy |
Azurite | 2CuCO3Cu(OH)2 | 55.3 | Blue | Viterous to adamantine |
Antlerite | Cu3SO4(OH)4 | 53.7 | Green | |
Chrysocolla | CuSiO32H2O | 36.2 | Bluish green, sky blue, turquoise |
Vitreous to earthy |
Chalcopyrite | CuFeS2 | 34.6 | Golden Yellow | Metallic to opaque |
The barren rock, or gangue has to be separated from the sulfide minerals in order to smelt the metallic copper from the ore. By far the greatest proportion of copper is extracted from the sulfides of copper, iron and sometimes other metals. Such ores originate from sulfur-bearing volcanic magmas, which have separated into metal sulfides and siliceous melts. The copper has concentrated almost entirely into the sulfide fraction, and if this becomes separated from the siliceous melt it can become deposited in veins or in fissures in the host rock by hydrothermal or other geological activity. In many ores (and most of those found in the Western USA) the copper minerals occur as a dispersion of fine particles. Such ores are called porphyries. Where mineralized rocks become outcropped or shattered, the sulfide minerals undergo chemical changes due to air, groundwater and heat, giving rise to the other main variety of copper minerals - the oxidized ores.
There is no shortage of copper resources. In fact, copper is one of the most abundant of the metallic elements in the earth's crust. The average estimated concentration is between 55 and 70 mg/kg, placing it below chromium (200 mg/kg) and zinc (132) but above tin and lead. Commercially exploited deposits of copper ores are found in many parts of the world, frequently associated with mountain-building processes. Deposits occur at many locations in the western cordillera of the Americas, mainly in the United States and Chile, and in areas of the North American plains like Michigan, Ontario, Quebec and Manitoba, at sites associated with the Pre-Cambrian shield. Copper is also found in many other countries throughout the world. Perú, Poland, México, Zaire, Zambia and Papua-New Guinea have historically been among the leading producers, and although African production has fallen sharply in recent years owing to political difficulties, large untapped resources remain. In addition, huge quantities of copper are known to exist as "deep-sea nodules" scattered on the ocean floor, although high recovery costs has thus far prevented their commercial exploitation. Chile and the USA are, respectively, the world's two leading copper-producing nations, Chile having overtaken the USA in the early 1990s.
Extraction
Ores are first mechanically crushed and ground so that nearly all copper mineral particles are freed from the gangue. Flotation by the injection of air and violent agitation is carried out with the pulverized ore held in suspension in water, to which surface-active agents have been added. The process yields concentrates containing roughly 30% copper, which are sequentially fed to a smelter, a furnace in which most of the some iron and sulfur are removed, then to a converter or converting furnace, where most of the remaining iron and other impurities are removed. (Depending on the type of smelting and converting furnace used, as much as 99+% of the sulfur can be recovered. It is used to make sulfuric acid, which is sold or used to leach copper from suitable ores directly, thereby circumventing the entire smelting-converting cycle.) The result is an impure (98+%) form of metal known as blister copper (for its surface appearance). The blister is then fire-refined further to adjust its sulfur and oxygen contents, yielding metal that is sufficiently pure for many other-than-electrical uses. However, since the fire-refined metal may contain commercially viable concentrations of precious metals (mostly silver and gold), most of it is cast into thick sheets known as anodes that are sent to the large electrolytic cells, where final refining takes place. A dc electric current, passed through the cells, dissolves the anodes and deposits the copper on cathodes. The final product of the refining process is electrolytic tough pitch (ETP) copper normally containing between 99.94 and 99.96% Cu. Cathodes are re-melted under controlled conditions and cast into forms suitable for further processing.
Modern methods of extraction allow economic leaching and electro-winning of copper from low-grade ores and extraction techniques are continuously being refined and developed to achieve the most efficient removal of copper from a wide variety of ores from sources around the globe. The techniques for extraction of copper from oxidized ores are quite different from those employed for the sulfide ores. The oxidized ores, consisting of the silicates, carbonates and sulfates, are treated by several methods, all involving some form of leaching of the crushed ore with sulfuric acid to produce impure solutions of copper sulfate. Today, more than 13% of all "new" copper is produced from leachates, which are normally concentrated using solvent extraction (SX) and stripped of their copper content by conventional electrowinning (EW), the so-called SXEW process. Sulfide ores are not efficiently attacked by sulfuric acid, but they can be leached if first oxidized by long exposure to the atmosphere and by contact with naturally occurring Thiobacillus Thiooxidans and Thiobacillus Ferrooxidans bacteria.
A simple infographic about the mining and extraction of copper was published in the November 1997 issue of Innovations.
The Copper Age 
Pre-dynastic Egyptians knew copper very well. In hieroglyphic writing the symbol used to denote eternal life, the ankh, was also used to represent copper. The Greek philosophers later adopted the symbol, slightly modified, as . The connection between eternal durability and the lifetime cost-effectiveness of copper and its alloys is surely not coincidental!
The Egyptians obtained most of their copper from the Red Sea Hills, but copper predates ancient Egypt by several millennia, and it is now known that an older civilization based on the Euphrates also new copper and utilized well-developed smelting techniques. The earliest known artifacts made from smelted metal were copper, and excavations at Catal Huyuk near Konya in Southern Anatolia, have yielded slags derived from the smelting of copper that have been dated to as early as 7,000 BC. Other civilizations in the Near- and Middle East, Hindustan and China also developed the use of the vital metal.
The Greek author, Homer, referred to the metal as 'Chalkos'; the Copper Age is therefore referred to as the Chalcolithic Age. In Greek mythology, the goddess of love, Aphrodite, is said to have emerged out of the sea near Cyprus looking at her image in a copper mirror. Some historians hold that this shows that the oldest profession is therefore metallurgy. Roman writings refer to copper as 'aes Cyprium' since so much of the metal then came from Cyprus.
'Oetzti', the 5,000-year-old mummified man recently discovered high in the Alps on the Italian-Austrian border was found with many implements including an excellent arsenical copper axe. It seems that he was probably a coppersmith himself, since his hair had high concentrations of copper and arsenic, which could probably have come from no other source.
The Bronze Age 
Before 3,000 BC it had been found that the addition of tin to copper produced bronze, an alloy that is harder and stronger than copper. Some of the earliest bronzes known come from excavations at Sumer, and are of considerable antiquity. At first, the co-smelting of ores of copper and tin would have been either accidental or the outcome of early experimentation to find out what kinds of rock were capable of being smelted.
Significant engineering uses had been found for copper as early as 2750 BC, when it was being used at Abusir in Egypt for piping water. (Some ancient Egyptian copper water tubes have survived to the present, a remarkable demonstration of the metal's durability.) Copper and bronze were employed for the making of mirrors by most of the Mediterranean civilizations of the Bronze Age period. The obliteration of Carthage by the Romans has obscured developments in Northern Africa at that time. It is only quite recently that evidence of the considerable engineering skills of the Carthaginians has emerged, including the earliest known use of gear wheels, cast in bronze. Bronze was used in many of the artifacts of every day Roman life - cutlery, needles, jewelry, containers, ornaments, coinage, knives, razors, tools, musical instruments and weapons of war. This pattern of use tended to be repeated wherever the smelting of bronze and copper was introduced, though necessarily on different time scales.
The Middle Ages and Later 
The invention of printing increased the demand for copper because of the ease with which copper sheets could be engraved for use as printing plates to give accurate reproduction of illustrations and maps. In Germany, playing card designs were engraved on copper as far back as 1430. Copper plates have long been adopted as the best means of engraving maps. The first known maps printed from copper plates are two Italian editions, dated 1472, by the geographer Ptolemy.
Copper or bronze wire then became a very important product, being vital for the weaving industry. The use of copper for sheathing the hulls of wooden boats was developed initially to prevent attacks on the timbers in subtropical waters by the teredo worm but it was subsequently found that copper-clad hulls also resist marine biofouling. This useful property prevented the heavy drag caused by the growth of weed that limited the speed of ships. (It has been reported that Lord Nelson's victory at Trafalgar resulted in part from the speed of his copper-clad ships, which enabled him to outmaneuver his adversaries.) The demand for copper was significantly increased as a result.
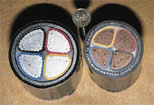
However, by far the greatest extension in the use of copper resulted from Michael Faraday's discovery of electromagnetic induction in 1831 and the way that the effect could be used to generate electricity. The same principle was used to develop electric motors. The electric lamp was invented by Sir Joseph Swan in 1860 and brought to a commercial design by Thomas Edison in 1879. These 19th century developments stimulated a tremendous demand for copper for generators, power cables, motors and all other products of the electrical engineering industry. Copper has the highest thermal and electrical conductivity per unit volume of any known substance except silver, which is only slightly superior in this respect. Because the conductivity of copper is dependent on its purity, extensive use is made of copper in its unalloyed form. Today about half of the world's production of copper is for electrical requirements.
Mining 
The oldest methods for removing rock from underground mines were the sledgehammer and wedge and the equally ancient technique of fire setting. In the latter case a fire set up against a rock face would produce thermal expansion stresses - the rock would either crumble naturally or could be shattered by water quenching. It was some time after the Islamic world introduced blasting powders from China to Europe in the 13th Century that explosives were first used specifically for mining. Today the old mining techniques have been replaced almost entirely by blasting with safe modern explosives and the use of heavy-duty mechanical cutting equipment, where the rock is soft enough to merit such treatment.
Also in this Issue:
- Introduction to Copper: Applications
- Introduction to Copper: Types of Copper
- Introduction to Copper: Mining & Extraction
- Introduction to Copper: Fact Sheets
- Phelps Dodge Morenci Has Converted All Copper Production to Mine-for-Leach
- How Hydrometallurgy and the SX/EW Process Made Copper the "Green" Metal
- Introduction to Copper: Hot Links & Further Reading