The Secret to Staying Young
Copper Applications in Mining & Extraction
New technologies and bold investments keep an aging Bingham Canyon on the leading edge.
In the early 1980's, Utah's Bingham Canyon Mine, nestled in the Oquirrh Mountains 18 miles southwest of Salt Lake City, was on the ropes, struggling through changing times and stacking up huge annual operating losses. The mine hit rock bottom in 1985. Kennecott's Utah Copper Division, operator of the Bingham Canyon Mine, laid off 4,400 workers and suspended production.But today, after a $1.5 billion modernization program (the most extensive in mining history), Bingham Canyon is mining again - this time as North America's lowest-cost copper producer and as a model of operational efficiency and environmental compliance.
Highlights
- The Bingham Canyon Mine reached its peak in 1980, with 2,500 miners drilling, blasting and hauling 370,000 tons of ore and overburden every day.
- By 1982, when sagging copper prices had created huge annual operating losses, the company began cutting back production and laying off workers.
- Today, after a $1.5 billion investment in modernization, the mine's man-shift productivity has tripled - 750 workers move 320,000 tons of ore and overburden daily.
Creating the Bingham Canyon pit required more than 90 years of mining and the removal of 5.6 billion tons of overburden and ore. The cumulative harvest of metals has been phenomenal: 14.2 million tons of copper (a single-mine record), 18 million troy ounces of gold, 150 million troy ounces of silver, 900 million pounds of molybdenum and significant amounts of platinum and palladium.
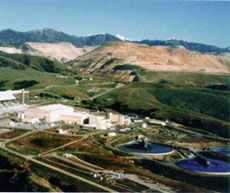
Historically, the Bingham Canyon Mine has come full circle. In the early 1900s, Bingham Canyon led the American metal mining industry away from frontier mining methods and into the modem era. Today, its modernization, productivity and efficiency once again serve as a model for the industry.
Mineralization at Bingham Canyon occurred 40 million years ago, when mineral-laden hydrothermal solutions accompanying a magmatic intrusion created a huge porphyry deposit rich in copper, gold, silver, molybdenum and lesser amounts of platinum and palladium. Erosion eventually uncovered part of the massive deposit, exposing oxidized, enriched outcrops. In the 1860s, after prospectors searching the rugged Bingham Canyon grazing area discovered the outcrops, miners went underground for lead, silver and gold, exploiting oxidized ores that were rich enough to smelt without concentration.
But underground mining exhausted the high-grade ores by 1898. Although the unmined portion of the deposit was still enormous, it was so low in grade as to make further mining economically unfeasible. But that same year, metallurgical engineer Daniel Jackling and mining engineer Robert Gemmell proposed mining the low-grade porphyry copper ores using massive surface-mining methods and concentrators. In 1903 Jackling raised capital and built the Copperton Mill, a 300-ton-per-day pilot mill. Three years later, steam shovels began open-pit mining.
Utah Copper next built the Magma Mill for a large-scale demonstration of the then-unproved flotation separation process. Flation separation utilizes the tendency of oil-covered mineral particles, such as metal sulfides, to adhere to air bubbles. A finely-ground ore slurry is mixed with an oily reagent, then vigorously agitated and acrated in tanks. Mineral particles adhere to the rising bubbles and float off as an oily froth in a rich concentrate suitable for smelting. Particles of gangue, or non-mineralized rock, fall to the bottom and are discarded as tailings.
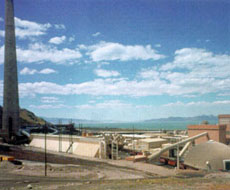
Bingham Canyon ore grades only 0.6 percent copper, meaning each ton of ore contains a mere 12 pounds of copper. Nevertheless, Daniel Jackling's system of massive mechanized open-pit mining followed by concentration by flotation separation made mining profitable. By 1910, the rapidly growing Utah Copper Co. controlled most Bingham Canyon mines, mills and claims. New technology figured prominently in the company's expansion. In the 1920's electricity replaced steam power for pit shovels and ore haulage locomotives, while a new chemical precipitation plant began recovering leached copper from the very-low-grade mineralization present in overburden waste rock.
Kennecott Copper Corp. acquired the Utah Copper Co. holdings in 1936, and soon prepared the mine for emergency wartime production with a 100,000-kilowatt generation plant to power the mill and two rail haulage tunnels to access the deepening pit. During World War II, Bingham Canyon alone supplied one-third of all the copper needed by the Allies - testimony to the size and efficiency of the growing mine. In the 1950s, Kennecott Utah Copper, an operating division of the Kennecott Copper Corp., purchased a nearby smelter and built a copper refinery, thus becoming a vertically-integrated copper producer with its own mining, milling, smelting and refining operations.
By the 1970s, Kennecott Utah Copper had invested a half-billion dollars into expansion and upgrading. New haulage trucks, downhole drills and electric shovels steadily increased mine production. Smelter workers installed new furnaces and advanced sulfur dioxide emission control equipment, and erected a 1,215-foot-high emissions stack.
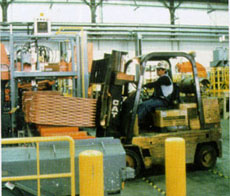
The Bingham Canyon Mine reached its peak in 1980, with 2,500 miners drilling, blasting and hauling 370,000 tons of ore and overburden every day. An additional 5,200 Kennecott Utah Copper employees worked in concentrating, smelting and refining operations to produce more than 300,000 tons of pure copper each year.
"But we had already become an old mine," says Louie Cononelos, Kennecott Utah Copper's current director of governmental and public affairs. "We were saddled with high costs of production and environmental compliance. We faced growing inefficiencies resulting from antiquated equipment, decades of 'tack-on' expansion, and an aging, in-pit rail haulage system. We were also confronted with competition from foreign copper producers. When copper prices began falling after 1980, we were no longer competitive."
Time for a Face Lift
By 1982, when sagging copper prices had created huge annual operating losses, the company began cutting back production and laying off workers. The following year, Kennecott Utah Copper suspended operations.
But Bingham Canyon still had one big asset: its world-class copper deposit with reserves for nearly 30 more years of mining - if the mine could regain competitiveness.
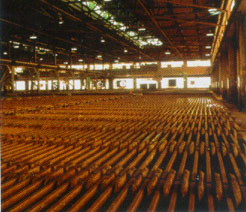
Bingham Canyon needed two things to get back on track: extensive modernization and temporary union wage and benefit concessions. The unions agreed to an unprecedented four-year contract in 1986 with significant wage and benefit concessions. Kennecott Utah Copper then embarked on a first-phase, $400 million modernization and restructuring program. As a gesture to the unions, the company resumed limited mining operations while modernization was not yet complete.
Rather than continuing to haul ore by rail from the mine, engineers installed a 60 x 109-inch gyratory crusher in the pit, then replaced the old rail haulage system with a five-mile-long crushed-ore conveyor system. Engineers constructed the ultra-modem Copperton Concentrator with three grinding lines, each equipped with a large, 36 x 17-foot, semi-autogenous grinding (SAG) mill and two new 20 x 30-foot ball mills that replaced 197 older crushing and grinding units. Ninety-seven 3,000-cubic-foot-capacity flotation machines replaced 2,000 old, smaller flotation cells. Engineers then phased out the original rail system that hauled concentrate to the smelter in favor of a new 17-mile-long slurry pipeline.
When full mining operations resumed in 1988, per-pound production costs fell by more than 33 percent. In 1992, Kennecott Utah Copper spent $220 million to add a fourth grinding line and flotation circuit to the Copperton Concentrator. The company then spent an additional $880 million to upgrade the refinery and build a new smelter.
Today, 11 years and $1.5 billion later, the Bingham Canyon Mine moves 320,000 tons of ore and overburden daily, roughly the same production level as in 1980. But it does it with only 750 workers - meaning man-shift productivity has tripled.
"Bingham Canyon is now essentially a new mine sitting atop the same grand old copper deposit," Cononelos says. "We've regained competitiveness and profitability, and we're among the world's safest, cleanest and most efficient mining operations."
Better Than Ever
Mining at the "new" Bingham Canyon Mine begins when eight rotary downhole units drill patterns of 55-foot-deep holes. Miners load each hole with a half-ton of ammonium nitrate-fuel oil (ANFO) explosive and detonate as many as four patterns daily. Electric shovels, mounting dippers as large as 56 cubic yards, load a fleet of haulage trucks. The new primary crusher reduces ore to minus-10 inches. A 900-foot-per-minute conveyor system speeds the ore five miles - three miles of it through a tunnel - to the Copperton Concentrator.
At the concentrator, SAG and ball mills reduce ore to the consistency of cosmetic face powder. Flotation separation, the same basic process pioneered at Utah Copper in 1903, separates barren rock from metalliferous particles, which float off as a 28 percent copper and by-product concentrate.
The slurry pipeline conveys the concentrate to smelter, where it is dried, then injected with oxygen into a state-of-the-art flash smelting furnace to oxidize the iron and sulfur. The iron is skimmed off, while the sulfur dioxide gas is captured and piped to the onsite acid plant for conversion to commercially-valuable sulfuric acid - a million tons of it per year.
Smelting produces matte, a molten copper sulfide containing 70 percent copper. The matte is water-quenched to form a sand-like solid, ground to a fine powder, then injected with oxygen into a flash converting furnace. The product is molten, 98.6-percent pure copper, along with additional sulfur dioxide. The sulfur dioxide is routed to the acid plant, while the copper is cast into 700-pound anode plates and shipped to the refinery.
In an automated process, anode plates are weighed, pressed flat, milled and interleaved with stainless steel cathode blanks. Robotic vehicles transport the prepared anodes to a tank house to be immersed in cells filled with an acidic electrolyte. The anodes dissolve during 11 days of electrolysis, and the copper ions are deposited on the cathodes as 99.9-percent-pure copper that is ready for shipping. Impurities and precious metals settle out as "slimes" and are sent to the precious metals plant where chlorination leaching and solvent extraction recover the metals.
By their nature, even small mines disturb the natural environment. Bingham Canyon-sized operations permanently alter it. At Bingham Canyon, environmental alteration is apparent not only in the enormous pit, but in a nine-square-mile tailings containment area.
"There's no question that the Bingham Canyon Mine has permanently altered the local environment," says Bill Williams, Kennecott Utah Copper's director of technical services. "Our challenge is to manage that alteration in a responsible manner. In just the last decade, we've spent more than $200 million on work directly related to reclamation and minimizing environmental impact. We've built a low-maintenance, high-efficiency water collection system that captures and recycles all groundwater. It's a gravity-feed system that requires no pumps and utilizes solar-powered monitors."
Kennecott's old copper smelter had managed to stay within Utah state emission limits of 3,300 pounds of sulfur dioxide per hour. But the new smelter, which went on-line in 1995 as the world's cleanest, cuts sulfur dioxide emissions to a mere 200 pounds per hour. "That means we're capturing 99.9 percent of the sulfur dioxide," Williams points out proudly.
"Our master reclamation plan will be implemented after the mine finally closes, whenever that will be," Williams continues. 'But it's not a firm plan. It will be modified as applicable new technologies evolve. The open pit will remain as it is. But the much larger tailings impoundment will be reclaimed. Remember, Bingham Canyon was a grazing area before mining began, and when we're finally through with mining, much of it will be a grazing area again."
But for the time being, Bingham Canyon is back doing what it does best - producing metals. Annual production now includes 310,000 tons of copper, 500,000 troy ounces of gold and 4 million troy ounces of silver, along with substantial amounts of molybdenum, platinum and palladium.
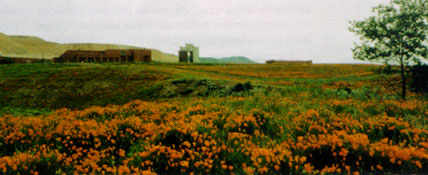
Modernization also has paid off in extended mine longevity, since reduced production costs permit much waste rock to be reclassified as ore. Ore reserves at Bingham Canyon now stand at more than 1 billion tons - enough for more than 30 years of mining.
"I see interesting parallels with the events of 90 years ago," Louie Cononelos observes. "It took investment and foresight to get this mine started back then and those same factors are keep it going now."
About the Author
Steve Voynick, a freelance writer from Leadville, Colorado, often writes on the topics of minerals and mining history.
Copyright 1998 MiningVoice
Reprinted with permission from MiningVoice January/February 1998
Also in this Issue:
- Direct Geoexchange Comfort Systems: Technology Increases Performance and Reduces Costs
- Copper DX Geothermal Heat Pump Web Site
- The Secret to Staying Young
- The Evolution of Telephone Cable