The History of Brass Making in the Naugatuck Valley
Copper Applications in General Interest
The Naugatuck Valley area in Connecticut was rather well known in the 19th century as the center of brass production in the United States. The Valley region was centered in Waterbury, and extended up and down the Naugatuck River from Torrington to Ansonia. Waterbury was affectionately referred to as the Brass City, and the entire area bustled with the rolling and manufacturing of brass and copper. There was a large demand for brass, and the Naugatuck Valley grew to meet it. Skilled brass workers were imported from England, and new manufacturing plants were set up as soon as new products were introduced. By 1850, the American brass industry forged ahead of the British and by 1884 the Naugatuck Valley was producing 85% of the rolled brass in the United States. ( 1) The Naugatuck Valley's leading position in the brass industry was maintained until World War II, when government sponsored war-based expansion was delibertly accomplished across (more or less) the country.
Some of the factors that influenced the emergence of brass manufacturing in Connecticut were the localization of the metalworking pioneers in the Naugatuck Valley, the Naugatuck River as a power source and access to the New York market. Two of the early metal working pioneers were William and Edward Pattison. The Pattions were skilled tinsmiths who began manufacturing tinware in Connecticut in 1746 ( 2) Until that time tinware was virtually unknown in the United States. Tinware such as plates, utensils, mugs, pans, and such became very popular. The Pattisons sold their tinware town to town and found it necessary to train others to work in their shop. New shops were opened by the newly trained tinsmiths, and the business expanded. Eventually the goods of the tinsmiths were sold door to door by peddlers so the tinsmiths could remain working in the shop.

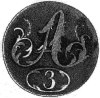


Scovill Buttons
Henry, Silas, and Samuel Grilley were also pioneer metalworkers in Waterbury Connecticut in 1790. They manufactured tin and pewter buttons by casting block tin and pewter in iron molds. ( 3) Then brass buttons came into vogue. By 1792 the Grilley Brothers were manufacturing buttons from sheet brass imported from England. Brass making technology was introduced to Connecticut by Abel and Levi Porter in the early 19th century. The Porters introduced the technology to make brass by the direct melting of copper and zinc, a technology invented twenty years earlier in England. ( 4) In 1802, the Porters and the Grilley brothers organized Abel Porter & Company in Waterbury Connecticut. A plant was set up to produce brass using the direct fusion method. The copper was obtained by melting old stills, teakettles, and other scrap. The zinc was imported from England. The copper and zinc were melted together, and the brass was cast into ingots and rolled into sheets. At first the rolls in a tiny iron mill in Litchfield were used to roll the sheets. Then the button manufacturers rolled their own sheet. Brass buttons were the first products of the American brass industry in Connecticut.
Eventually the brass buttons were added to the stock of the peddlers. Brass buttons were used on everything, both functional and ornamental. As manufacturing grew in the United States, the peddlers stock became more diverse, including tinware, woolen goods, brass goods, rugs. The peddlers would also trade and barter for the manufacturers. In the case of the button manufacturers they would pick up old copper items which were melted into scrap. The peddlers were responsible for selling the brass buttons and supplying the button manufacturers with copper scrap, creating a heritage of recycling that has remained fundamental to brass production down to the present.
In 1806 Abel Porter and Company was bought by Frederick Leavenworth, David Hayden and James Mitchell Lamson Scovill. Their business started out manufacturing brass buttons for military uniforms. Then they turned to rolling brass for their button business. By 1836, Scovill button shop had more than 50 employees and the entire button making process was mechanized. The partnerships of the early brass industries were often dissolved and reorganized, with many changes in ownership over the life time of the operation. Scovill Manufacturing Company was eventually formed from the Leavenworth, Hayden, and Scovill operation. The company went from manufacturing buttons and rolling brass to manufacturing sheet brass and nickel silver (copper-nickel-alloy alloys, also known as "German Silver"), gilt and covered buttons, brass hinges, coal oil burners and lamps, brass thimbles and a variety of other small articles.
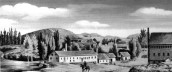
During the same time period Aaron Benedict went from manufacturing horn and ivory buttons to gilt (copper) buttons. By 1829, Benedict was also attempting to roll the brass that he consumed in button making. The company of Benedict and Coe was an outgrowth of Benedict's pioneer button manufacturing. They manufactured their own brass and nickel silver. Israel Holmes, another pioneer in the early brass business, organized four brass companies in the Naugatuck Valley, bringing production methods, the latest machines and skilled labor from England. In 1853, Holmes and two associates formed a company that was among the largest producers of brass, nickel silver and copper sheets in the United States. ( 5)
By the 1820's the Waterbury entrepreneurs were importing skilled workers to Connecticut from England to help the Americans compete in quality and price with English producers. Button manufacturing and brass production were expanding. The button companies were able to produce more brass then they needed, and began to sell rolled brass on the open market. ( 6) In 1822 there was one company in Connecticut making brass rolled buttons. They produced 20 gross of buttons per day, which accounted for 80% of the metal buttons produced in the United States. In 1843 there were three factories rolling brass with 600 workers using 250 tons of copper per year. By 1855, 2000 tons of copper per year were being produced in the Naugatuck Valley. ( 7)
By the 20th century, Connecticut ranked first in the United States in the total production of brass products, which included 75% of the brass rolling, 33% of the brass castings, and 50% of the brassware. ( 8) The range of brass products included wire, small arms cartridges, lamp fixtures, bird cages, finishing reels, chains, picture wire, clocks, locks, and bolts. The American brass manufacturers took the lead from their British rivals in both the processing of brass and brass products.
References:
-
Marcosson, Isaac F., Copper Heritage, The Story of Revere Copper and Brass Inc., Dodd, Mead & Co., New York, 1955, p. 35.
-
Marcosson, Isaac F., Copper Heritage, The Story of Revere Copper and Brass Inc., Dodd, Mead & Co., New York, 1955, p. 33.
-
Morgan, Forrest, Connecticut as a Colony and as a State, or One of the Original Thirteen, The Publishing Society of Connecticut, Hartford, 1904, p. 237.
-
Davis, Watson, Story of Copper, The Century Company, New York, 1924, p. 230.
-
Morgan, Forrest, Connecticut as a Colony and as a State, or One of the Original Thirteen, The Publishing Society of Connecticut, Hartford, 1904, p. 237.
-
Brecher, Jeremy; Lombardi, Henry; Stackhouse, Jan; Brass Valley: The Stories of Working People's Lives and Struggles in an American Industrial Region, Temple University Press, Philadelphia Press, 1982, p. 3.
-
Brecher, Jeremy; Lombardi, Henry; Stackhouse, Jan; Brass Valley: The Stories of Working People's Lives and Struggles in an American Industrial Region, Temple University Press, Philadelphia Press, 1982, p. 48.
-
Morgan, Forrest, Connecticut as a Colony and as a State, or One of the Original Thirteen, The Publishing Society of Connecticut, Hartford, 1904, p. 237.
Also in this Issue:
- New Copper Alloys: Revised and Reactivated Alloy Compositions
- New Copper Alloys: Compositions of New Copper Alloys
- New Copper Alloys
- ARI and CDA Sponsor Research on Copper Joining Techniques with Future Refrigerants
- The Butte Copper Mines
- Paul Revere - Copper Industry Pioneer
- The History of Brass Making in the Naugatuck Valley
- Environmentally Friendly Permanent Mold Casting