Download in PDF format [292 Kb]
NYCO Minerals, Inc. is a leading producer of wollastonite, a form of calcium silicate widely used in a number of industrial applications including reinforcing filler in injection-molded plastics. The company's U.S. operations are headquartered in Willsboro, New York, in the Adirondack Mountains near the southwestern shore of Lake Champlain. Here, NYCO mines and processes approximately 100,000 tons of wollastonite annually ( photo below).

NYCO's products are in strong demand, but energy costs at Willsboro have doubled over the past few years, and, as in any company, management keeps a sharp eye on its bottom line. Mineral processing plants tend to be energy intensive because they typically use hundreds of electric motors for milling, classification, purification, treatment and transport.
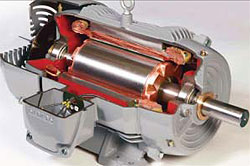
But energy costs kept rising, jumping from $0.04-$0.05/kWh to $0.07 and then to $0.09 over the past few years. What to do now?
The solution - suggested by Jeff Lawrence, vice president of sales for KJ Electric, NYCO's electric motor supplier, headquartered in Syracuse, New York, and John Moller, account manager for Siemens Energy and Automation, Inc. (SE&A) - was to replace a large number of NYCO's motors with Siemens' new IEEE Plus ® models. Those motors feature die-cast copper rotors ( Figure 1) and other design improvements that make them one or two percentage points more efficient than current NEMA Premium motors. 1
Back to TopRebate Available
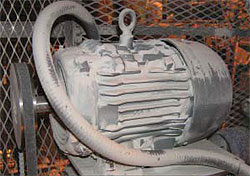
As a bonus, the highly efficient IEEE-Plus motors NYCO ordered qualified for rebates offered through the New York State Energy Research and Development Authority (NYSERDA). This utility-ratepayer funded program seeks to reduce overall state energy consumption by encouraging, among other things, the installation of energy-saving equipment, including motors that meet or exceed NEMA Premium efficiency standards. Analogous incentive plans are offered by several states and many utilities. For a listing of such programs compiled by the Consortium for Energy Efficiency (CEE).
Back to TopMotor Replacement Begins
Rick Olcott began installing the new copper-rotor motors in January 2007. His logic was straightforward: "We decided that if we could change these out, and with the NYSERDA rebate, we could save a lot of money. We've become very energy conscious. The plant runs 24/7, so we have to run the most efficient way we can." Olcott's initial purchase order included 150 motors in frame sizes ranging from 143T to 256T, with ratings up to 20 hp. Most are in the F1 configuration, plus a few in F2 and F3. He recently added a few C-face motors not included in the original blanket order.
"We developed a list of motors we wanted to change out based on their efficiency," says Olcott. "Right now, we're concentrating on anything less than 90% efficiency. Some were built in the early 1950s, and some don't even have a nameplate because, in some cases, they were supplied by an OEM. But we'll also change out some EPAct motors because the new ones are much more efficient."
In May 2007, replacement was proceeding as fast as possible, given the plant's continuous operating schedule. Examples of motors replaced as of that date include the blower motor shown in Figure 2, a belt conveyor motor that transports material between the crushing to beneficiation departments ( Figure 3), a pair of boiler feedwater pump motors ( Figure 4), and about 15 more in sizes ranging from 1 hp to 20 hp. The current round of motor replacements was completed during a scheduled maintenance shut-down in mid-summer, 2007.
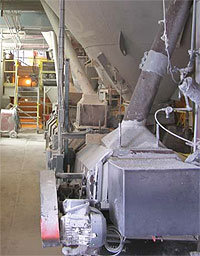
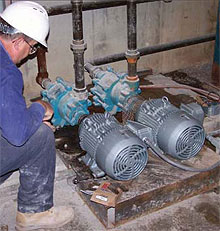
Rapid Payback Expected
The initial replacement order was valued at approximately $80,000. Olcott sees that figure as an investment. He expects the motors will pay for themselves in two to three years, some faster than that. No operating cost data were available as of this writing, but Jeff Lawrence and John Moller calculated the savings that should be realized for the range of motor sizes involved ( Table 1). These are approximate values, since, for example, they do no necessarily correspond to the actual load factors at which all motors of a given size operate. On the other hand, the estimates are based on utility rates prevailing in early 2007, and those rates might increase in the future, thereby shortening the respective payback periods.
hp | Load Factor | Annual Hourly Usage | Utility Rate, $/kWh | "Old" Eff., % | "New" Eff., % | New Motor Price | NYSERDA Rebate | Annual Savings | Payback, Years |
---|---|---|---|---|---|---|---|---|---|
1 | 0.75 | 8,000 | 0.09 | 77 | 86.5 | $208 | $25 | $57 | 3.17 |
1.5 | 0.75 | 8,000 | 0.09 | 80 | 87.5 | $268 | $30 | $57 | 4.19 |
2 | 0.75 | 8,000 | 0.09 | 80 | 88.5 | $309 | $30 | $97 | 2.88 |
3 | 0.75 | 8,000 | 0.09 | 82.5 | 90.2 | $327 | $30 | $125 | 2.37 |
5 | 0.75 | 8,000 | 0.09 | 85.5 | 90.2 | $382 | $30 | $123 | 2.86 |
7.5 | 0.75 | 8,000 | 0.09 | 85.5 | 92.4 | $518 | $60 | $250 | 1.83 |
10 | 0.75 | 8,000 | 0.09 | 86.5 | 92.4 | $624 | $60 | $297 | 1.89 |
15 | 0.75 | 8,000 | 0.09 | 86.5 | 92.4 | $837 | $60 | $446 | 1.74 |
20 | 0.75 | 8,000 | 0.09 | 88.5 | 93.6 | $1,025 | $60 | $496 | 1.94 |
Data courtesy KJ Electric and Siemens Energy & Automation |
The key point is that, once the motors have paid for themselves, they will continue to generate savings throughout their service lives. It is well-known that the cooler motors run, the longer they last, and that premium-efficiency motors of all types tend to run cooler than less efficient types.
With their exceptionally low power (I 2R) losses, copper-rotor motors should run cooler still. In fact, SE&A says its new copper-rotor motors are very conservatively designed with regard to operating temperature, utilizing F-class winding insulation for a B-rated temperature rise at a service factor of 1.15.
NYCO Minerals is proud to be an early adopter of copper-rotor motor technology. It is confident the highly efficient and exceptionally well-built motors will provide the company with years of low-cost, satisfactory service.
Why Copper?
About two-thirds of an AC induction motor's electrical losses occur in the stator, and motor manufacturers have made great strides in reducing these losses by adding more copper to the stator windings, thus reducing wasteful, resistive (I 2R) heating. NEMA Premium-grade motors are largely based on this practice. Rotor losses account for about 25% of total losses. These losses occur in three forms: slip losses, magnetic core losses and, again, I 2R losses in the rotor's conductor bars. John Caroff, marketing manager, low-voltage motors, SE&A, explains that the motors' extremely high efficiency results from their die-cast copper rotors, combined with a careful redesign of the entire motor to optimize the properties brought by copper and with stringent quality control during manufacturing to minimize electrical and stray-load losses. Substituting die-cast copper for traditional die-cast aluminum in the "squirrel cage" decreases resistive losses because copper's volumetric electrical conductivity is approximately 66% higher than that of aluminum. Copper provides other benefits, as well, including the ability to shorten the lamination stack (thus reducing cost) and, depending on design, reduce slip.
How much difference does higher efficiency make in the cost of motor ownership? More to the point, can higher efficiency justify the cost of a more efficient motor?
Consider this: an average 10-hp EPAct, TEFC, general purpose motor costs about $506 after dealer discount. Knowing the duty and load cycles, the utility rate and the nominal (dataplate) efficiency, we can calculate the annual cost of operating the motor. A more convenient method is to utilize MotorMaster+, which also enables the calculation of life-cycle costs, costs comparisons and numerous other financial functions. If we assume that our 10-hp EPAct motor operates 8000 h/y at 75% of full load, and that electricity costs $0.0617/kWh (the national average industrial rate), and that its efficiency is 90.7% at 75% loading, we find that the motor consumes $3,061 in electric power annually, or about six times the motor's purchase price. If purchased to replace an existing "standard efficiency" motor, the EPAct motor would pay for itself in 2.79 years.
According to MotorMaster+, an equivalent NEMA Premium motor costs about $117 more than the EPAct motor 2 but operates at an efficiency of 92% (at 75% load), enabling it to consume $42 less per year in energy. Thus, the gain of 1.3 percentage points in efficiency pays off the additional cost of the more efficient motor in 2.75 years when, as MotorMaster+ does, one includes a 0.1-kW demand savings.
A NEMA Premium motor fitted with a copper rotor offers even better economics. MotorMaster+ lists the Siemens GP100 as an example in this size. The DOE software cites a discounted price of $553 for this motor, which is, surprisingly, about $70 less than that for the "average" aluminumrotor NEMA Premium motor, as defined by MotorMaster+. The annual savings, compared with an average EPAct motor and as calculated using MotorMaster+, are $48 per year, leading to a payback of only 0.98 years.
After that, all savings are pure gravy, and in fact, payback can often be much quicker. For a company like NYCO paying $0.09/kWh, that "average" 10-hp NEMA Premium motor would pay for itself in a little more than 2.5 years, while a motor with a copper rotor would pay back its cost premium in a paltry 0.44 years.
Taking a longer view, $74 saved per year adds up to $1,480 over the 20-year life of the motor, enough to buy one new motor every 7.5 years, assuming the national average $0.617/kWh utility rate. At the $0.09/kWh NYCO Minerals pays, the savings add up to $108 per year and $2160 over two decades. Bottom line: efficiency is important, and life-cycle costs are all that count in the end.
Back to TopThe Principals
Rick Olcott is electrical supervisor at NYCO Minerals' Willsboro, New York, facility where he planned and currently directs the installation of 150 Siemens copper-rotor motors. Mr. Olcott can be reached at 508-963-4262.
Jeff Lawrence is vice president of sales at KJ Electric, Syracuse, New York. The company is purging EPAct motors from its active inventory and will henceforth offer only NEMA Premium motors, including the Siemens lines of copper-rotor motors. Mr. Lawrence can be reached at 315-454-5535 and jefflawrence@kjelectric.com.
John Moller is an account manager for Siemens Energy & Automation (SE&A). Mr. Moller, along with Jeff Lawrence, introduced NYCO Minerals to Siemens' new copper-rotor motors. Mr. Moller can be reached at john.moller@siemens.com.
Footnotes
-
In all sizes up to 500 hp, there are IEEE 841 motors from one or more manufacturers that meet NEMA Premium efficiency standards, and in all but seven sizes, there are motors that exceed those standards. IEEE Plus® is Siemens' trade name for their version of the IEEE 841 motors, which utilize a die-cast copper rotor to raise efficiency. Other manufacturers utilize other design improvements to achieve similar results.
-
Prices and discounts are taken from MotorMaster+ 4.0, a motor-cost program available by request at AMO Tools Help Desk.