Download PDF Version [1.15 Mb]
- Introduction
- Motor Failure Policy
- Critical Motors
- Motor Spares Inventory
- Repair or Replace
- More Recommendations
- Purchasing Specifications
- Systems Approach
- Summary
Energy costs and downtime can be greatly reduced by instituting a motor management plan. Part II of this three part series specifically addresses the establishment of a motor failure policy and the development of purchasing specifications. Part I addressed the general aspects of a motor management plan, including the first steps of creating a motor inventory and guidelines for motor repair and replacement. Part III will examine motor repair specifications as well as preventive and predictive maintenance.
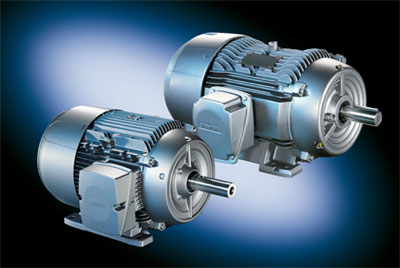
Introduction
As described in Part I, a motor management plan needs to be instituted at the facility level to be effective. Lacking such a plan, invisible and uncontrolled costs from excess energy use, frequent downtime and productivity losses can become significant.
The keystone of any plan is the assessment of the motor population of the facility, both for in service and in spares motors. There would be no clarity for acting on any plan or measuring its effectiveness without a proper motor inventory. Part I outlined a basic plan for taking inventory of the motors; creating guidelines for replacing and repairing them; and gaining management support through the demonstration of financial incentives.
In the present paper, Part II goes beyond the basic plan and details the specifications for purchasing motors. It describes sound policies that can be adopted to guide investments in new and replacement motors.In the next paper, Part III further addresses proper motor repair specifications as well as preventative and predictive maintenance.
Back to TopMotor Failure Policy
Worn-out motors ideally would be replaced before they fail and interrupt production. A motor failure policy is a set of guidelines and supporting infrastructure that enables decisive and proper action to take place. It is established before a motor failure occurs.
Using the repair and replace guidelines covered in Part I, one can begin to develop a meaningful motor failure policy. Motor failure policy comes down to these choices: repair this motor at failure, replace it at failure, or retrofit it immediately.
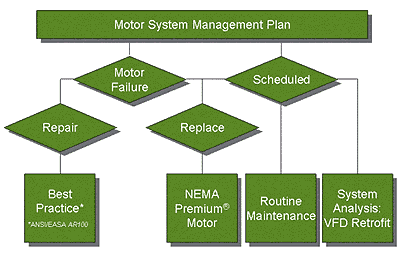
Critical Motors
It is essential to identify the critical motors in your facility. These motors are the most important to the business process; their failure would cause a financial setback or a lost opportunity.
Contingency plans should be proactively developed so if one of these critical motor fails then the problem can be quickly resolved and its effect on the business can be minimized.Kitt Butler, Director, Motors & Drives, Advanced Energy Corporation, Raleigh, North Carolina, says, “You want to identify the critical motors in your process. If one motor in the middle of the line fails then the whole mill could go down. You cannot just wait for that to happen; you have to have a plan ready before that motor fails. That is the crux of motor management: Plan before the motor fails. If you allow the motor to fail before determining what to do then you will typically be in the panic mode and bad things can happen.”
If the plan for a particular motor is to repair or rewind upon failure, make certain to select a service center that adheres to guidelines established by the Electrical Apparatus Service Association (EASA).
Back to TopMotor Spares Inventory
To address downtime, motor failure policy must define a motor spares inventory. It must support actions that minimize costly business interruptions. According to Butler, “A spare motor inventory is indispensable in motor management, especially for critical motors; spares need to be within arm’s reach should an in service motor go down.”
A spares inventory program should align with plans to upgrade motors to NEMA Premium® efficiency. Upgrade spares as well as operating motors because replacing a failed older, less efficient motor with another standard efficiency motor provides no energy savings or operating cost reduction.
Johnny Douglass, retired Senior Industrial Engineer, Washington State University Energy Program, says, “The spares inventory includes motors that fit more than one application; quite often motors in the one to 100 horsepower range can fit into a variety of locations. Consequently, the spares inventory should consist of NEMA Premium motors; the fact that a motor in spares may go many places dictates that all the motors should be NEMA Premium motors.”
MotorMaster+ inventory lists are useful for sharing with motor distributors. If you can’t stock some motors at your facility, because of lack of budget or storage space, you can share in-service motor inventory lists with your distributor and ask the distributor to stock the NEMA Premium motors on your list. In this manner, spare motors are available on short notice but stored at the distributor rather than your location. MotorMaster+ software is available by request at AMO Tools Help Desk.
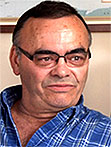
As the purchasing agent for Qubica/AMF, Rick Streeter has overseen the upgrade of motor spares and knows of the above limitations. “I try to have a spare motor for every machine whenever possible; but some of our motors are just too big to keep in spares here on site. For example, we use 150 and 200 horsepower motors that are just too big to keep in spares. On the other hand, for the smaller motors, I keep at least one spare on hand for every type of motor that we use here.”
Repair or Replace
Horsepower Breakpoint
In part I of this series, horsepower breakpoint was covered in the context of the repair or replace decision. It is also a consideration in motor failure policy. The policy can be as elementary as “always replace motors under 50 horsepower” or more sophisticated.
Useful graphs for picking a horsepower breakpoint can be created using special calculators, for example, from the Advanced Energy Corporation. In one such graph, the vertical axis represents motor horsepower and the other axis represents hours of operation. The calculator plots a curve that depends on the cost of electricity. Once a curve is plotted it is easy to find the horsepower breakpoint that corresponds to any payback period of operation. Tools for calculating the horsepower breakpoint are available on the website of the Advanced Energy Corporation.
Mr. Butler points out, “Surveying all the motors in a facility can be labor intensive. It takes eyeballs and legs. One has to walk around and look at all the nameplates of the motors, recording and processing all that information.”
Replace at Failure
Motors should be tagged for replacement upon failure. Gilbert McCoy, P.E., Energy Systems Engineer with the Washington State University (WSU) Energy Office, Olympia, Washington, advises, “Use MotorMaster+ to calculate the energy savings for each motor in your plant. Fortunately, MotorMaster+ can accomplish this for all the motors in the inventory with one quick batch analysis. Tag those motors that should be replaced upon failure so the millwrights know what to do and which spare motors should be NEMA Premium motors versus older standard motors.”
Opportunities for energy savings are lost when spare motors are not properly tagged. “The millwrights are likely to pick an old standard efficiency motor and install it,” Mr. McCoy points out. “At that point, the opportunity is lost for energy savings throughout that motor’s operating life, which could be ten years or more.”
More Recommendations
Frequent Failures First
Some industries kick off their motor improvement project by identifying motors with histories of frequent failure. Obviously, besides replacing the motors, it is also prudent to identify and correct the root cause of the problem. The Electrical Apparatus Service Association (EASA) has developed an in-depth seminar and reference manual on “Root Cause Failure Analysis," according to Tom Bishop P.E., Senior Technical Support Specialist for the EASA, St. Louis, Missouri.
If the cause of failure is due to a harsh environment then you can reduce downtime and increase reliability, while also realizing significant energy savings, by replacing those problem motors either with premium-efficiency motors or with premium efficiency, severe-duty motors.
The Longview complex of the Weyerhaeuser Company in Longview, Washington serves as an excellent example. It instituted a policy calling for all non-IEEE 841 motors of 50 horsepower or less to be replaced upon failure with energy-efficient IEEE 841-2001 models regardless of the condition, age or rebuild history of the existing motor.
Mr. McCoy recalls, “A few years ago, we had the opportunity to work with a Weyerhaeuser pulp and paper mill. A review of the maintenance records showed 28 motors with histories of frequent failures; these motors would fail every two to four years, resulting in downtime and lost productivity. The company jump-started its motor improvement program by immediately replacing problem motors with new NEMA Premium efficiency motors. It chose not only premium efficiency motors but also NEMA Premium efficiency IEEE-841 petroleum and chemical duty motors. Some manufacturers call these motors “extra tough” or “severe duty” motors; in addition to an expected longer operating life and long warranties, these motors are corrosion resistant and have lower vibration displacements.”
For more info, read the full case study on the Weyerhaeuser motor failure policy.
Monitor the Spares
Spare motors are supposed to be ready to replace failed in-service motors. How ready are they? If the spares are not premium efficiency motors then you may be better off recycling them, depending also on factors such as hours of operation. If they are NEMA Premium motors then they need occasional shaft rotation to avoid ‘flat-spotting’ as do all motors sitting in storage.
Johnny Douglass notes, “A motor upgrade program must address spares as well as operating motors. Sometimes spare motors of standard efficiency should be recycled even if freshly rewound. You may be able to recover some of the cost from the motor components inside.”
Failed EPAct Motors
The decision to scrap a failed EPAct motors and replace it with new NEMA Premium motors should be based on a life cycle analysis. EPAct motors are less efficient than NEMA Premium motors. No energy savings is realized by putting an EPAct motor back in service.
A rewound motor could be even less efficient than when it was new; however, a service center that adheres to EASA good practice guidelines should be able to mitigate or resolve efficiency losses.
For more information on good practices, see the EASA website.
Gil McCoy contends, “When we do our motor assessments, we look mainly at replacing standard-efficiency motors when they fail with NEMA Premium efficiency motors. Nonetheless, depending on operating hours and utility rates, many times it is also cost effective to junk EPAct efficiency motors when they fail, and replace them with new NEMA Premium efficiency motors.” Standardizing on T-Frame motors also reduces the number of motors that must be maintained in the on-site spares inventory.
Oversized Motors
Research shows that the efficiency of most motors peaks for loads between 70 to 75 percent and declines below 50 percent. The situation is different for large motors, however, according to Gil McCoy, who says, “Motor assessment staff generally believe oversized, under-loaded motors are bad. They recommend replacing motors loaded to less than 50 percent of their full load with smaller motors matching load requirements. But large standard efficiency motors should not be replaced with smaller standard efficiency motors. The energy savings will be small or non-existent because larger motors typically have higher full-load and part-load efficiencies than smaller motors. Large motors generally maintain a high efficiency all the way down to 25 percent of load. The benefit comes from replacing oversized motors with a smaller premium efficiency motor matched to load requirements.”
Tom Bishop summarizes, "Efficiency may be higher for larger motors than for smaller motors but it is still reduced when not matched to the load."
Minimize Downtime with Severe-Duty Motors
The true cost of downtime is difficult to calculate and often underestimated. Downtime is the subject of countless process improvement projects within a typical company, which speaks to its importance. A plant typically loses several percent of its production capacity because of downtime; and most plants do not calculate downtime costs accurately, underestimating the total cost by 200 or even 300 percent.
Bruce Benkhart, Director, Advanced Proactive Technologies, Springfield, Massachusetts, adds, “Downtime is crucial to any facility, whether an office, a hospital or an industrial plant. Whether they are making widgets, cars or pharmaceuticals, downtime means that production stops and profits plummet. Downtime is ultimately the most important consideration.”
Mr. McCoy gathered data on the cost of downtime at a pulp mill in British Columbia. “Downtime is critical for industrial plants,” he says. “This pulp mill had a capacity of about 1100 air-dried metric tons per day. We calculated the value of the pulp produced at $25,000 per hour at a price of $600 per ton. In the case of this pulp mill, the cost of downtime is huge. The reliability and uptime benefits from new premium efficiency motors can dwarf the energy costs. To realize these benefits, motor managers in the mills and process industries preferentially purchase “severe duty” motors, or IEEE-841 petroleum and chemical duty motors.
“In a severe processing environment, replacing existing motors with NEMA Premium severe duty motors makes good business sense, especially when downtime is critical,” says Mr. Bishop, "but a severe duty motor in a non-severe duty application probably won’t save more energy than other motors of the same efficiency."
Frame Adapters
Adapter rails and bases have been available for decades. They are used to install T-frame motors in systems designed for older U-frame motors.
Motor interchangeability is common today because of the standardization of frame sizes. Motors of the same horsepower, the same speed and the same enclosure normally fit the same frame size, even though the motors are from different manufacturers. In other words, if the motors are in standard frame sizes then a motor from one manufacturer is interchangeable with a similar motor from another.
Yet, in some situations, the frame sizes are not the same. Motors have become more compact for a given horsepower primarily due to better insulation (Class H at 180 °C) which allows motors to run much hotter in a smaller package (T-frame). What do you do when you find a motor of the older U-frame type in your facility?
On the subject of frame sizes, Mr. McCoy comments, “Motor manufacturers make premium efficiency U-frame motors but such motors carry a considerable cost-adder. When we see old U-frame motors in a plant, we know they are likely to be repaired when they fail. They are often returned to service because the mounting bolts and shaft heights for those motors are different than those of a T-frame motor. Nonetheless, we encourage the purchase of frame adapters or transition bases, which ideally would be maintained in the spares warehouse and readily available when an old U-frame motor fails. In this manner, the old motor can be easily replaced with a new modern T-frame motor.”
Purchasing Specifications
Purchasing specifications cover a wide gamut of elements. They identify and specify what motors to stock and how many. They document the decision-making process for purchasing stock. The following sections outline some key considerations relating to the development of purchasing specifications.
Develop Corporate Support
Organizationally, energy efficiency management tends to be a fractured process. A disconnect often occurs between plant maintenance engineering, purchasing and finance. Cooperation needs to evolve into teamwork before advances in energy savings can happen.
Rob Penney offers some insights on organization. He is the senior energy engineer for the Washington State University Energy Program as well as a professional mechanical engineer and a certified energy manager. He is responsible for the energy savings team, business development and energy project deliverables at WSU. He says, “Within a business, purchasing makes motor purchases, accounting pays the energy bill and engineering looks at the process. They often do not communicate effectively with each other. Only when each pays attention to the motor systems and they all work together as a team can they bring it all together, making good motor management decisions and really saving energy.” The team approach lends itself nicely to gaining corporate support.
Official Mandates
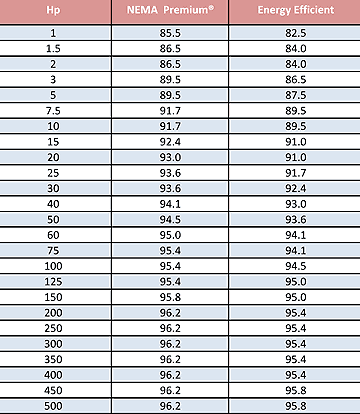
Pay attention to Energy Independence and Security Act (EISA, pronounced eye-suh) legislation for the mandates on motor efficiency for today and for the future.
Kitt Butler at Advanced Energy reminds us, “EISA was signed into law by George Bush in 2007. It covers many energy-related topics, including motors, and became effective December 2010. For general purpose motors from one horsepower to 200 horsepower, EISA raised mandated efficiency levels above the levels of EPAct legislation of 1992.”
See the energy efficiency table from Advanced Energy for a comparison of EPAct to EISA efficiencies at various horsepower.
Mr. Butler continues, “The Department of Energy is mandated by Congress to expand the efficiency envelope for electric motors. It has done so since 1992 without using exotic materials and designs, but it is reaching a point of diminishing returns. Meanwhile, the industry, efficiency advocates and other stakeholders are recommending to the DOE that it consider motors not previously covered, for example, motors with mechanical alterations that do not affect the motor efficiency. Gear motors are a good example. The DOE will rule on these motors sometime in the last quarter of 2012.”
Prior to EISA, original equipment manufacturers were motivated mainly by cost and reliability. Efficiency wasn’t a high priority but now that has changed. Emmanuel Agamloh, Ph.D., P.E., Motor Systems Engineer, Advanced Energy Corporation, Raleigh, North Carolina says, “We hear a lot about efficiency now. OEMs are paying attention to the efficiency of their motors in their equipment. The EISA legislation is playing a vital role because the increase from EPAct to NEMA Premium efficiency levels directly affects the choice of motors by equipment manufacturers. At Advanced Energy, we often receive requests from OEMs to verify that electric motors meet the EISA efficiency levels so they can be put in the OEM equipment.”
Even Higher Efficiency
Some motor technologies provide even higher efficiencies than NEMA Premium. Referring to the CDA’s technical reference library, induction motor engineers have long known that replacing die-cast aluminum with copper in the rotor squirrel cage reduces motor losses by as much as 15 to 20 percent, thereby improving the energy efficiency.
Motor manufactures have improved on copper rotor technology to the point that copper-rotor motors often exceed the NEMA Premium efficiency standard by a few percentage points.
Mr. McCoy points out, “Today the highest standard for motor efficiency is designated NEMA Premium. Yet some motors built with advanced technology exceed that standard by at least a fraction of a percentage point or even by a few percentage points. Those motors are often built with cast copper in the rotor; or permanent magnets in the rotor for motors operated exclusively with variable frequency drives.”
The advantages of permanent magnets might not be realized with smaller motors. See the cutaway figure of a copper rotor motor.
MotorMaster+ includes an embedded, motor-manufacturer inventory of 17,000 motors along with a price and performance database. The program allows search results of motors to be listed in descending order of full-load efficiency.
Mr. McCoy says, “Below twenty horsepower, copper-rotor motors are likely to be at the top of the energy listing. Copper-rotor motors tend to score high in efficiency because of their greater use of copper.”
Discounts and Incentives
Pay attention to discounts as you make payback calculations. They can be significant. Look for discounts from your distributor. List prices are merely starting points for price negotiation. Take advantage of volume purchases and any available energy program rebates.
Mr. McCoy says, “The catalogues and websites of motor distributors give the list price for each motor. The truth is that manufacturers seldom sell motors at list price but often offer discounts. The more motors an industry buys, the bigger the discount they are likely to get. If I were to place a large order directly with a motor manufacturer then I might enjoy a discount as big as 65 percent off the list price. In other words, I would pay only 35 percent of the list price. Typically, large industries achieve discounts of about 50 percent from their local distributor.”
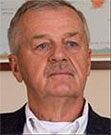
Terry Blodgett, Branch Manager (retired), Kaman Industrial Technologies, Watertown, New York says, “The price of a motor depends on the quantity ordered at one time. Buying one at a time versus several at a time has a significant impact. You could replace your motors one at a time but if you buy in multiples then the discount will be much greater; and you will have much more buying power to develop a much stronger price if you buy plant-wide. The lower the price, the shorter the payback period.”
Incentive programs provide additional savings. State programs may provide financial incentive to assist end users in purchasing energy efficient products.
NYSERDA supported an incentive program in New York State for many years. Bruce Benkhart says, “Applied Proactive Technologies has been running the NYSERDA motors program since 2002. Originally, the premium efficiency motor program in New York State was strictly an incentive program for the distributor and end user. It was funded by a systems benefit charge that applied to all users of electricity. This particular program provided an incentive to move up from EPAct motors to premium efficiency motors; it was essentially a rebate to bring down the cost of owning more efficient motors. It provided an incentive to the distributors to move those products and was a win-win program for both the dealer and the user. It was quite effective in achieving much higher penetrations of the more expensive but more efficient NEMA Premium motors than would otherwise have been the case.”
Other states may have similar programs worth investigating. Since the recent EISA legislation mandates NEMA Premium motors, many utilities have discontinued their rebate programs. Nonetheless, it is worthwhile to investigate whether “above NEMA Premium” incentive programs exist following the enactment of EISA on December 19, 2010. The “above NEMA premium” efficiency designation often is referred to unofficially as ultra-efficient or super-efficient.
Motor Sizes and Quantities
What motors should I stock and how many? The goal is to match the most efficient motors for the job to your needs. The following sections will provide some insight to help you decide.
Small Motors, Big Savings
Eighty percent of the motors in most facilities are 20 horsepower or less as shown by the pie chart. These motors have lower efficiencies than larger motors so there is an opportunity for significant efficiency gains when they are replaced with NEMA Premium.
A graph of Motor Horsepower versus Percent Efficiency Difference was created using the efficiency table from Advanced Energy. It illustrates the one to three percent efficiency gain that can be realized for motors up to 50 horsepower. The biggest improvements are for motors up 20 horsepower. Motors above 50 horsepower present lesser percentage gains in efficiency.
Johnny Douglass explains, “The emphasis has been on larger motors. That’s an appropriate starting point for your plan but smaller motors are important, too. They typically are more numerous and the gain is much higher. Smaller motors of the standard type with efficiency in the 80 percent range allow for more improvement. If you have many of these motors then you can save a great deal of energy. Sometimes a facility has a huge number of small motors driving things such as a conveyor belt system. Upgrading to a more efficient standard results in huge savings.”
Severe-Duty Motors
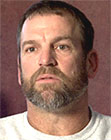
In harsh operating environments or whenever motors frequently fail, IEEE-841 severe-duty motors are a good option. An example from Weyerhauser was already mentioned. Gil McCoy provided another example through his work with the mill in British Columbia. He concludes, “There are two reasons why they were looking at extra-tough IEEE 841 petroleum and chemical duty motors and severe duty motors. One is the perception that the motor is going to last longer with more uptime; the other reason is that these motors carry a longer warranty. Generally, IEEE -841 motors have a five-year warranty and NEMA Premium motors about three years; for comparison, general purpose motors and even EPAct efficiency motors typically are warrantied for only one year.”
A final example comes from Joe Anderson, who is the maintenance manager at Interface Solutions, Beaver Falls, New York, which is the largest producer of automobile gaskets. He is highly motivated to minimize downtime using IEEE-841 motors. “We depend on the reliability of the Severe Duty NEMA Premium motors to minimize the shutdowns resulting from rooftop fan motor failures,” he says.
Payback Calculations
Payback calculations are essential. Returns on investment in 9- to 24-months make sense. But where an EPAct or older motor is used in an intermittent duty application, that is, where the motor runs only a few hundred hours a year, removing a functional motor for replacement with a new NEMA Premium motor is not a good investment. The payback period would be too lengthy. Look for applications with a quick payback period.
Sharing Inventory Data
Distributors are invaluable. They see your present needs and anticipate your future needs. They can also alleviate some storage space concerns. Distributors understand what motors are available and can provide appropriate solutions to their customers.
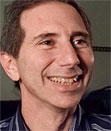
Kenny Jacobs, controls and drives product manager, KJ Electric, Syracuse, New York describes the relationship between a distributor and its customers. He explains, “As an EASA motor shop, KJ Electric provides motor survey assistance to its industrial customers. This assistance includes, for example, helping its customers minimize inventory by cross-referencing the one motor that is suitable for replacing multiple motors.”
Mr. McCoy concurs, “MotorMaster+ is useful when you have an in-service motor inventory because you can share inventory data with your motor distributor. You can easily discuss with the distributor which additional motors you are likely to buy and which he should keep in stock. In this manner, premium efficiency motors are ready to use in a spares inventory at the distributor’s storeroom instead of your own warehouse.”
Systems Approach
Look for energy savings in the entire system. The system extends from the step-down transformer at the switchyard or plant service entrance to the motor driven equipment and process controls. Anything you can do to reduce system losses saves energy.
Mr. Benkhart notes, “The motor represents a huge opportunity for energy savings but motors also are attached to systems. Whether a pump, air conditioner, or compressor, the system has its own associated losses. While many systems would benefit from variable frequency drives, other savings beyond the motor are possible. You have the transmission via a belt, a pulley or a direct drive; and then the system itself. The energy savings could be massive. There could be 50 percent savings in the system itself absent the motor. Before embarking on those system challenges, however, start with a motor that is the most efficient it can be.”
Variable Frequency Drives
Fans, mixers, conveyers and pumps are all good candidates for variable frequency drives, or VFDs, which match motor speeds to varying load requirements. VFDs enable motors to run at speeds lower than the rated speed. Less energy is wasted and in-line flow restrictions such as throttling valves or inlet discharge dampers can be eliminated.
One believer in VFDs is Johnny Douglass, who says, “Often some of the greatest savings are realized by converting fixed speed drives to variable frequency drives. In airflow or liquid flow situations, a motor often drives a fan or pump and an air damper or a valve modulates the flow. In these situations, double-digit savings can be realized by converting to an electronic variable frequency drive. These motor controllers can be retrofit to an existing motor application and accomplish tremendous savings by eliminating the pressure drop associated with a modulating valve or a damper, whose functions are replaced by simply slowing down the speed of the motor. In these situations, you can save as much as 40 percent in electrical energy costs, depending on the fraction of time the system operates at a lower flow.”
VFD’s are cost-effective. They increase productivity, lower operating costs and waste less energy. Joe Anderson at Interface Solutions claims success with VFDs and comments, “Our plant’s Variable Speed Drive Inverter Duty Ready NEMA Premium motors are working very well. Our process needs exact amounts of flow and the loads vary all over the place. With the variable speed drives, we can better control the process.”
Match Motors to Load
Overloaded motors tend to run hotter; motors that run too hot tend to fail earlier than motors matched properly to the load. The life of the motor insulation is reduced by one half for every 10 °C rise in motor temperature.
Motors can run somewhat overloaded for short time periods. The nameplate on the motor gives a Service Factor multiplier, which is the percent operational overload acceptable for the motor. A service factor of 1.15 indicates the motor can operate 15 percent overloaded without seriously damaging the motor but one should not expect the best performance or maximal service life.
As an example, see the image of the nameplate from a Baldor Reliance motor whose service factor of 1.15 is circled in red in the image, i.e., SER. F. 1.15.
So far, it has been assumed that the supply voltage is within specified limits. An under-voltage contributes to an overheating condition, too, putting undue stress on a motor.
Mr. Douglass says, “When matching the motor to the load, be careful not undersize the motor. It is particularly bad when the motor is undersized and the voltage is under voltage. This combination tends to make the motor run too hot. When a motor runs hot, its service life is shortened. Even if the voltage is correct, an undersized motor running into its Service Factor will be operating at a temperature higher than its design temperature, which will shorten its life. Service factors are often 15 percent but can be as low as 0 percent when the motor is controlled by an adjustable speed drive. Sometimes the service factor can be higher than 30 percent. One should never plan to operate very much or often in the Service Factor.”
Space Constraints
Be cognizant of space limitations when specifying a motor as a replacement for existing EPAct or standard-efficiency applications. Not all of the motor dimensions are specified in NEMA standards. Some motor dimensions are specific to each motor manufacturer.
Check a “NEMA Motor Dimensions – Reference Chart” against your space limitations, or contact your motor distributor for any dimension in question.
Gil McCoy adds, “NEMA has a frame assignment series. Motors are interchangeable parts. Premium efficiency motors, energy efficient motors and standard efficiency motors all have the same mandated dimensions and tolerances set by NEMA. The one difference between a premium efficiency motor and a standard efficiency motor is that the former may stick out further in the off-drive end direction. If you are space constrained then talk with your motor supplier to obtain the dimensions of the new premium efficiency motor and ensure it fits before you place an order.”
Financial Feasibility
Is the move to these energy efficient products financially feasible? The answer is a resounding “Yes!”
Energy efficient motors are among the best investments available, considering the high cost of energy and especially in today’s uncertain economic environment. Electric motor driven equipment accounts for between 30 to 50 percent of the electricity consumption in commercial facilities in the United States. Industrial facilities consume 60 to 70 percent.
Mr. Butler’s advises, “Motors belong to a very important electric technology classification because they use a lot of energy. The lifecycle costs of an electric motor are comprised mostly of payments for electricity. Anywhere from 97 to 98 percent of the total lifecycle cost is for electricity; only two to three percent is invested in the initial capital cost to purchase that motor and in the maintenance cost as well. When considering a new motor purchase, it is very important not to focus just on initial price but focus mainly on the efficiency of the motor. In the long run, you will mostly be paying for the energy consumed by the motor.”
Simple payback analysis shows the move to energy efficient products is feasible. Computing the return on your financial investment before investing the capital dollars is possible where energy is a factor.
In the words of Mr. Benkhart, “In the move to more expensive but clearly more efficient products, the important considerations are the price of the new motor and the cost of operating a motor. While an incentive program helps reduce the purchase price of a higher cost NEMA Premium motor, there is still the bigger expense of operating the motor. Reaching the correct answer requires many pieces of information, including the type of motor, how often the motor is in operation (duty-cycle, single or multiple shifts), the horsepower, the motor efficiency and the percent motor load as well as the local cost of electricity, which typically ranges from $0.04 or $0.10 per kilowatt-hour. By entering the data collected during an inventory into a software tool such as MotorMaster+, a range of payback periods for a variety of operating parameters and utility costs can be calculated. The resulting payback calculations will help determine the feasibility of going forward with new, efficient, NEMA Premium motors.”
Mr. Benkhart adds, “Most companies will approve a decision to buy energy saving equipment if the investment meets the simple payback or ROI requirement of less than 18 to 24 months. For a motor operating more than 6000 hours at roughly $0.10 per kilowatt-hour, the analysis yields a simple equation that estimates payback somewhere between six and twenty-four months. If the extra cost of buying the new NEMA Premium motor is $300 but the annual energy savings is $400, the nine-month payback clearly meets the payback criteria. Such information gleaned from our assessments and software tools empowers the customer to make good financial decisions regarding energy efficiency. Absent motor population information and tools to collect and analyze the data to make an informed decision, the facility is running blind.”
There are many tools to help make such payback decisions. Besides MotorMaster+, many motor manufacturers offer their own proprietary tools. Advanced Energy Corporation has a motor management spreadsheet.
An example spreadsheet from the “1-2-3 Approach to Motor Management Summary” is shown here. It is derived from the Motor Decisions Matter 1-2-3 Approach to Motor Management tool.
This spreadsheet allows five motors to be examined alongside additional quantities from similar motors. It is an excellent tool for calculating payback and energy savings. The user is required to provide accurate information regarding repair costs and new motor pricing.
Summary
A motor failure policy built on the information provided in this publication takes the risk and indecision out of the picture when a motor failure occurs. For example, tagging every spare and in-service motor in the facility with actionable information ensures that wrong decisions will not be made due to lack of such information.
Whether the policy stipulates replacing any motor under a certain horsepower, installing IEEE 841 motors in place of critical motors, or adherence to EASA good practice guidelines when repair is appropriate, in each case, you have taken the steps to minimize costly downtime and business interruptions.
Purchasing specifications developed using the technical tools and industry resources presented in this publication could serve as the blueprint or reference document for your motor management plan. The document can specify what new technologies to invest in, such as ultra-efficient copper-rotor motors or VFDs; it can specify the number of commonly used motors to stock in your facility; and it can specify the tools to assess which motors are most efficient and which yield the highest energy savings and shortest time to payback.
The purchasing specifications can also identify preferred motor distributors, who provide the best volume discounts as well as the best pre-sales and post-sales support.
Although the percentages certainly require updating, it is worth mentioning that the U.S. Department of Energy reported in 1998 that only 11 percent of customers had written specifications for motor purchases and only two-thirds of those customers included efficiency in their specifications.
Take advantage of these useful tools, the technology and the information provided here by the industry experts. It can result in an evergreen source for both energy savings and increased productivity.
Acknowledgements
CDA acknowledges the help of government- and industry-based motor experts in the creation of the Motor Management Best Practices series. Contact information for the motor experts cited in this publication is as follows.
Emmanuel Agamloh, Ph.D., P.E., Motor Systems Engineer Advanced Energy Corporation, Raleigh, North Carolina. Tel. (919) 857-9023, eagamloh@advancedenergy.org.
Bruce Benkhart, Director, Advanced Proactive Technologies, Springfield, Massachusetts. Tel. (413) 731-6546, bruce@appliedproactive.com.
Tom Bishop, P.E., Senior Technical Support Specialist, Electrical Apparatus Service Association (EASA), St. Louis Missouri. www.easa.com.
Kitt Butler, Director, Motors and Drives at Advanced Energy Corporation (AEC), Raleigh, North Carolina. Tel. (919) 857-9017, kbutler@advancedenergy.org.
Johnny Douglass, Retired Senior Industrial Engineer, Washington State University (WSU) Extension Energy Program. Tel. (360) 956-2086, douglass.johnny@gmail.com.
Gilbert A. (Gil) McCoy, P.E., Energy Systems Engineer with the Washington State University (WSU) Energy Extension Office, Olympia, Washington. Tel. (360) 956-2086, mccoyg@energy.wsu.edu.
Rob Penney, P.E., Certified Energy Manager, Senior Energy Engineer at Washington State University (WSU). Tel. (360) 628-2053, penneyr@energy.wsu.edu.