The design and installation of drainage systems range from simple to complex, depending on the type of building, the local code and the occupancy requirements. The local plumbing code will include requirements for acceptable materials, installation and inspection, and these must be followed as the first requirement of an acceptable job.
There are usually differences—sometimes minor, sometimes quite important—among plumbing codes. Among the features which differ from code to code may be minimum tube sizes, permissible connected fixture loads, fittings and connections, methods of venting, supports and testing. Few codes are completely specific about installation details and leave the responsibility of proper and suitable installation to the designer and the contractor.
In large and multi-story buildings, the design will generally require the services of a mechanical engineer and a plumbing designer. The plumbing designer has the responsibility for coordinating the drainage system design within the overall building construction requirements. A good drainage design must accommodate the problems of installation space, building movement, support, expansion and contraction, pipe sleeves, offsets and provisions for necessary maintenance.
In residential buildings and small one- and two-story commercial buildings, the drainage piping is usually straightforward in design and simple in installation. Type DWV copper tube, installed with good workmanship by an experienced plumber, will provide many years of trouble-free service.
The smaller diameter of DWV tube and fittings makes it possible to install copper drainage systems where other competing piping materials would be impossible, difficult or more costly. For example, a 3-inch copper stack has only a 3-3/8-inch outside diameter at the fitting and can be installed in a 3-1/2 inch cavity wall.
Prefabrication
Considerable savings can be effected by prefabricating copper DWV subassemblies. Prefabrication permits work even when adverse weather prohibits activity on the job site. Simple, inexpensive jigs can be made to position the tube and fittings during assembly and help eliminate costly dimensional errors. Freedom of movement at the bench permits joints to be made more readily than at the point of installation, where working space may be limited.
Soldered joints are strong and rigid. Subassemblies can be handled without fear of damage. The lightweight features of copper DWV tube and fittings make it possible to handle fairly large assemblies. Other dependable drainage plumbing materials may weigh three to four times as much. Subassemblies require a minimum of support when connected to a previously installed section of a drainage system.
Copper DWV tube has been used successfully for years in all parts of drainage plumbing systems for high-rise buildings-for soil and vent stacks and for soil, waste and vent branches. Copper tube's light weight and the ease with which it can be prefabricated have been especially important in high-rise drainage systems.
Expansion of DWV Systems
In high-rise buildings, expansion and contraction of the stack should be considered in the design. Possible movement of a copper tube stack as the temperature of the stack changes is about 0.001 inch per degree F per 10-foot floor. (See Figure 14.2) This is slightly more than for iron and steel pipe and considerably less than for plastic.
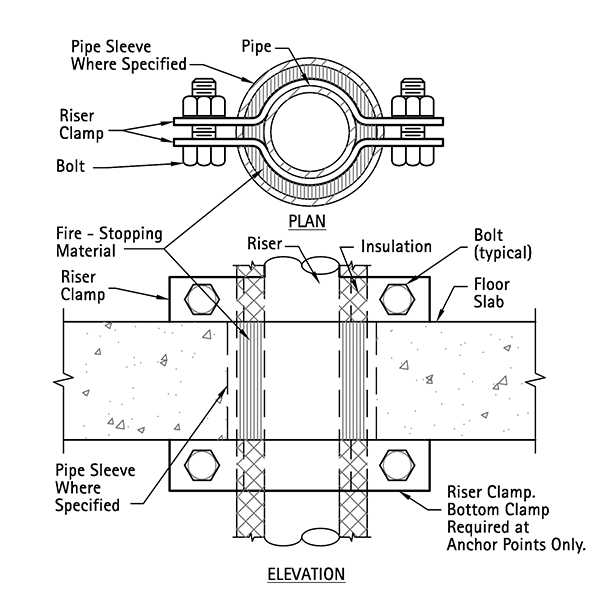
Since length, temperature changes and piping design itself are all involved in expansion, the designer must determine the best way to take care of expansion in any particular installation. One simple procedure for controlling thermal movement is to anchor the stack. Anchoring at every eighth floor will take care of an anticipated maximum temperature rise of 50°F; anchoring every four floors will take care of a 100°F maximum temperature rise. Care should be taken to avoid excessive stresses in the stack anchors or structure caused by thermal growth of the stack.
Perhaps the simplest effective anchor, when the stack passes through concrete floors, is to use pipe clamps and soldered fittings as shown in Figure 3.1. The pipe clamps can be placed above and below the floor, backed up by sliding the fittings tight against the clamps and soldering them in place. At all floors between anchors, sleeves in the concrete floors should be used to prevent lateral movement of the tube.
Hydrostatic Testing of DWV Systems
While a copper drainage system is not ordinarily operated under pressure conditions, it must withstand the pressure of a hydrostatic test. The allowable pressures for copper DWV tube and soldered joints are given in Table 14.3d and in Table 14.4a, respectively.
To determine the vertical height that can be statically pressure tested (with water) in one segment, take the lowest applicable figure from Table 14.3d and Table 14.4a and multiply by 2.3. (A 2.3-foot column of water creates a pressure of 1 psi.) For example, if 50-50 tin-lead solder is used and the largest tube size is 4-inch at a service temperature of 100° F, multiply 80 (the lower of the solder joint rating of 80 in Table 14.4a and the tube rating of 257 in Table 14.3d) by 2.3; the result is 184. Thus, a 184-foot vertical segment of stack could be tested at once.
If 95-5 tin-antimony solder is the joining material, the lower of the corresponding rating for 4-inch tube from the tables, 257 (the tube governs) is multiplied by 2.3, equaling 591. Thus, theoretically, 591 feet (59 ten-foot stories) could be tested at once. If the joint is brazed, the value from Table 14.3d for annealed tube (150) governs. This value multiplied by 2.3 equals 345 feet, or only 34 stories at once. The actual vertical segment height tested is usually much less and depends on practical considerations on the job.