- Abstract
- Introduction
- Trailer Corrosion Tests
- Test Results
- Additional Testing
- Summary and Conclusions
- References
Abstract
For many years the tubing in automotive brake systems has been manufactured from low-carbon steel. One or more superficial coatings are applied after brazing to protect the steel substrate from corrosion, because steel has no inherent corrosion resistance to the road environment. Although coating composition has changed since the original hot-dip lead-tin coatings were used, coating flaws remain a problem. The addition of zinc-rich paints did little to improve the protection of the tube. Current aluminum-zinc coatings and added polyvinylfloride coatings are still inadequate to totally protect the steel tube.
In a recent series of tests, 90-10 copper-nickel tube (UNS C70600) was fabricated into typical brake system '.shapes" which were then attached to a test trailer and conveyed through various corrosive and mechanically abusive test track environments. The tests included holding the tubes in a high humidity chamber for a portion of each 24-hour test cycle. After 40 cycles and at each 10 cycles thereafter, the individual tubes were required to pass a 20,684 kPa (3,000 psi) pressure test. Candidate tube materials had to complete 60 cycles to satisfy the minimum requirement.
Current production steel tubes passed the 60-cycle requirement but failed well before 120 cycles. The 90-10 copper-nickel tubes completed 200 cycles with essentially no reduction of their original burst strength.
Back to TopIntroduction
Brake tubes are located in a high-corrosion area. Although many other automotive components operate in the same hostile environment, few are less forgiving in the event of a failure. Thus, one of the major considerations in the design of an automotive hydraulic brake system is the integrity of the brake tubing which distributes the system pressure.
In 1965, an annual safety inspection of motor vehicles was introduced in Sweden and subsequently in other European countries. This procedure included the inspection of hydraulic brake tubes for the presence of rust. Concurrently, the Swedish Motor Vehicle Inspection Company began publishing annual reports on the results of these tests. 1
In 1969, laboratory tests were reported comparing some inherently corrosion-resistant copper alloy tube materials with the then-current production materials. 2
Early in 1970, the Swedish Corrosion Institute approached the brake tube corrosion problem from the standpoint of using a corrosion-resistant material rather than trying to protect the surface. 1
The European auto industry's initial response to brake tube corrosion problems was to terminate the use of the then-current hot-dipped terne metal coating over steel tube. Laboratory testing in a 6% neutral vapor salt spray test indicated that corrosion resistance could be obtained by a 25-micron zinc coating in place of the terne coating. In the years that followed, it became apparent that the laboratory testing had not accurately reflected conditions that exist in the actual operating environment. Subsequently, various plastic coatings were applied over the zinc and some are still being used to this date. 1
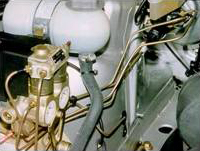
The bar graph shown in Figure 2 depicts the percentage of vehicles failing safety inspections because of defects in the brake systems of eight-year-old Volvo passenger cars. The 1970 model cars had terne-coated steel tubes. Tubes in the 1971 models were zinc coated. Defects other than rusted tubes are included in these values, but their effect on the data is minimal. The reduction in defects related to the introduction of 90-10 copper-nickel tube in 1976 is dramatic.
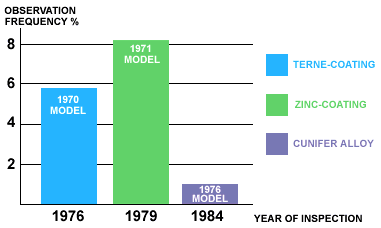
The paper 2 presented at the SAE Annual Meeting in January 1970 dealt with the then "state of the art" in tube coatings; the data presented in that paper are still pertinent. Voids, poor adhesion, discontinuities and physical damage to the superficial coatings used today can result in accelerated, localized corrosive attack which renders useless the value of any intact coating elsewhere on the tube.
An incident reflecting the latter condition was recorded in an SAE paper presented in 1991. 3 A brake line which should have burst when tested at 1 1 5,832 to 158,579 kPa (1 6,800 - 23,000 psi), in fact, burst at 4,825 kPa (700 psi). The paper states, "This particular tube portion was located at the end, above and behind the rear axle, and showed a great deal of corrosion, perhaps due to gravel impingement."
Against the background summarized above, a test program was undertaken by the Copper Development Association Inc., with the cooperation of an automotive vehicle manufacturer, to evaluate thoroughly the applicability of Copper Alloy C70600 tube, 90-10 copper-nickel, for automotive brake line application. The tube material is described in Table 1.
Composition, percent maximum, unless shown as a range | |||||||||
---|---|---|---|---|---|---|---|---|---|
Ni Fe Mn Zn Cu |
9.0 - 11.0 1.0 - 1.8 1.0 1.0 Remainder |
||||||||
Mechanical Properties | |||||||||
Yield Strength, min (0.2% offset) Tensile Strength, min Elongation in 50.8mm (2.0) |
110,316 kPa (16,000 psi) 310,179 kPa (45,000 psi) 40-55% |
||||||||
Pressure Proof Test | |||||||||
Unless otherwise specified, the finished tubing shall sithstand a hydrostatic proff test, with no evidence of failure, at a p[ressure which will subject the material to a fiber stress of 110,316 kPa (16,000 psi). Test pressure shall be determined by Barlow's equasion for thin hollog cylinders under tension: ![]() Where:
No tube shall be tested beyond a hydrostatic pressure of 34,473 kPa (5,000 psi), unless so specified. |
Trailer Corrosion Test
The design test procedure generally used today to evaluate the corrosion resistance and integrity of motor vehicle body and chassis components consists of 100 cycles of controlled humidity soaking and drying, salt spraying and mileage accumulation over various road surfaces with test samples mounted on a trailer. The sequence of test cycle events is listed in Table 2.
Pre-Conditioning | |||
---|---|---|---|
1) | Salt Bath 20 km/h (12 mph) |
||
2) | Dirt Road 70 km/h (45 mph) |
||
Test Cycle | |||
3) | Salt Spray Booth 15 Minutes |
10) | Vehicle Ramp Closure Checks |
4) | Salt Bath | 11) | Salt Bath 20 km/h (12 mph) |
5) | Washboard Salt Highway 65 km/h (40 mph) |
12) | Washboard Salt Highway 65 km/h (40 mph) |
6) | Dirt Road (Car/Lt Trk) Gravel (Hvy Trk) 70 km/h (45 mph) |
13) | Dirt Road 70 km/h (45 mph) |
7) | Washboard Salt Highway 65 km/h (40 mph) |
14) | Washboard Salt Highway 65 km/h (40 mph) |
8) | Dirt Road 70 km/h (45 mph) |
15) | Dirt Road 70 km/h (45 mph) |
9) | Humidity Chamber @ 50C (120°F) 85-92% R.H. 6 hours |
16) | Humidity Chamber @ 50C (120°F) 85-92% R.H. 7 hours |
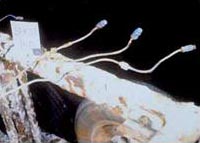
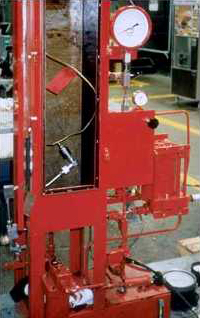
Beginning with the 40th cycle, and at 1 0-cycle intervals thereafter, each tube is subjected to an internal pressure test of 20,684 kPa (3000 psi). Candidate materials must complete 60 cycles to satisfy the minimum requirement. Figure 4 shows the test equipment on which the hydrostatic pressure tests were made.
This performance would be expected even if a measured superficial abrasion had been inflicted on the tube as a condition for the evaluation of the tube surface.
Back to TopTest Results
The data in Table 3 4 reveal that after 200 test cycles, which exceeds three times the minimum benchmark of 60 cycles, the copper-nickel material retained more than 89% of its initial average burst strength.
Sample No. | Hydrostatic Brust Pressure | |
---|---|---|
kPa | psi | |
Before Test Exposure | ||
1 | 114,108 | 16,550 |
2 | 113,079 | 16,400 |
Average: | 113,591 | 16,475 |
After 200 Test Cycles | ||
3 | 104,111 | 15,100 |
4 | 102,732 | 14,900 |
5 | 100,663 | 14,600 |
6 | 99,974 | 14,500 |
Average: | 101,870 | 14,775 |
Also noteworthy is the narrow spread in post-test burst pressure. This attests to the uniformity of copper-nickel's strength and physical properties, a feature which is not present in the currently used coated carbon steel tube.
Back to TopAdditional Testing
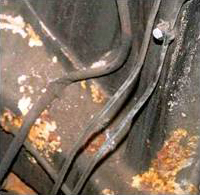
The brake tubes were removed from this vehicle and hydrostatic burst tested with the following results:
Tube No. 1 111,694.95 kPa (1 6,200 psi)
Tube No. 2 106,868.62 kPa (1 5,500 psi)
These real-world data are welcome confirmation of the trailer test results.
Back to TopSummary and Conclusions
The automobile industry faces many challenges in the market place and on its test tracks. It must produce vehicles that will compete in a world market on the basis of quality, safety, reliability, durability and cost. The test results presented above demonstrate that 90-10 coppernickel tube is a significantly better choice for automotive brake lines than low-carbon steel because:
- The use of an inherently corrosion resistant material is the best protection against long-term brake tube corrosion. This has been demonstrated by Volvo, which uses 90-10 copper-nickel tube in automobiles they have produced during the last 15 years.
- The results of trailer corrosion testing indicate that 90-10 copper-nickel tube (UNS 70600) is a superior product compared to the coated steel tube used for brake lines in today's U.S.-made vehicles.
- Current double-wrapped, brazed and coated steel tubing is susceptible to brazing voids, coating voids, poor coating adhesion and discontinuities. These susceptibilities, combined with random service damage, mean the actual service life of the brake tube materials presently used in U.S.-manufactured vehicles should be considered unacceptable.
It must be recognized that all underbody components, including the brake tubes, will be struck by objects thrown up by the tires. Such random damage must be considered the most vulnerable link in the chain.
The tubing designer generally specifies the addition of a metal or plastic sleeve to the tube areas believed to be most vulnerable to stone damage. However, an inherently corrosion-resistant copper-nickel tube provides the surest protection against such random service damage, especially compared to a coated steel tube.
Back to TopReferences
-
Svenson, G.E., Swedish Motor Vehicle Inspection Company, Brake Pipe Corrosion - the Situation 1986, Except from ISO Document 150/22/2WG 8N 82, February, 1986.
-
Ingram, A.G. and Miner, D.K., Hydraulic Brake Line Corrosion; An Initial Investigation of the Problem, SAE Technical Paper 690530; presented at the SAE Annual Meeting, Detroit, Michican, May 1969.
-
Bologna, D.J., Accelerated Corrosion Tests and the Evaluation of New Automotive Brake Line Coatings, SAE Technical Paper 912292, Conference, Dearborn, Michigan, October 1991.
-
Brantigan, J., Control Power Company, Hydrostatic Burst Test Results, September 11, 1992.