- Automobile Life-Expectancy
- Worldwide Data On Wear
- Added Cost of Coatings
- The Move to Copper-Nickel Tubing
- The Right Tubing for the Job
A vehicle's braking system is as crucial to a vehicle's performance as its engine and drive train. The tubing carrying pressurized air or fluid through the system is the vital link between master cylinder and slave cylinders at the wheels.
Brake system tubing is vulnerable to the pressures of air or fluid flowing through it, to corrosion from road mud and salt, and to damage of any protective coatings on its surfaces from stone pecking where it is exposed under the chassis.
Prior to 1930, copper and brass, having excellent inherent pressure containing and anti-corrosion characteristics, were the materials of choice for brake tubing. By post World War II, automotive industry mass production economics dictated adoption of a low-cost form of double wrapped, furnace-brazed steel tubing that is still in use today worldwide.
Having excellent, initial pressure bearing characteristics, steel tubing is, however, susceptible to corrosion. To retard its inherent corrodability, coatings of various materials, e.g., zinc-rich paint, terne (a lead/tin alloy) and epoxy, have been applied to steel tubing exteriors. However, no coating has proven to be totally impervious to pitting, scuffing and chipping due to flawed manufacture, careless installation and exposure to hostile environmental conditions like loose gravel. A penetrated coating allows the corrosion process to begin.
An inherently corrosion-resistant tubing material is the only way to insure continuing effective corrosion resistance.
Copper-nickel alloy C70600, an alloy of 90% copper and 10% nickel, is inherently corrosion resistant to road salt, and its use as brake tubing is increasing based on: 1) Changing life-expectancy for automotive vehicles; 2) Worldwide service-experience data on brake tubing wear; and 3) Increasing cost of corrosion-retarding coatings for steel brake tubing.
Automobile Life-Expectancy
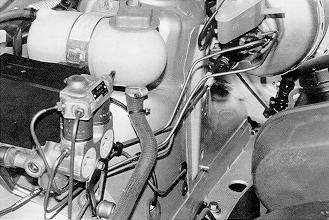
Automobile use habits serve as an unspoken directive to manufacturers to continue their efforts in providing cars with extended lives.
The adoption of extended warrantees by the automotive industry compels design engineers to pursue the 10-yard-life goal as the new standard of total vehicle reliability. In the case of subsystems like brakes, a 20-year component life is desirable to ensure that critical subsystems long outlast the vehicle of which they are a part.
Back to TopWorldwide Data On Wear
In 1965, 251,000 automobile accidents in the USA involved brake failures. In that same year, at a major meeting of the Society of Automotive Engineers (SAE), the problem of brake loss due to steel tubing damage was identified as both dangerous and costly. By 1969, the SAE published a study, Hydraulic Brake Line Corrosion: An Initial Investigation of the Problem (A.G. Imgram and D.K. Miner, Paper 690530, Mid-Year Meeting, May 1969). Indications were clear: corrosive deterioration of steel brake tubing created maintenance problems and could be a hazard to safety. The report revealed that steel brake tubing was highly erratic after 4-6 years in service. It also identified copper-nickel alloy C70600 tube as outstandingly superior to conventional steel brake line tubing in laboratory salt-spray-exposure burst tests. Copper and four copper alloys also out-performed the double wrapped steel tubing in the tests.
Sweden, with a national program of vehicle inspection since the mid 1960s, has been a consistent source of the most accurate data on the problem. The Swedes frequently ban vehicles from the road due to badly corroded steel brake tubing. As in the USA, roads in Sweden during the winter are salted for snow and ice removal.
In spite of corrosion-retarding coatings that are applied in accordance with specifications requiring a minimum coating weight per square foot of tubing surface area (not an overall coating thickness), little protection may result in local areas.
Since the 1970s, observed brake tubing faults have diminished with improved coatings. Still, in 1988, over 90,000 Swedish vehicles failed testing due to damaged steel brake tubing, most of which was corrosion related. West Germany, which instituted mandatory vehicle inspections in 1970, has collected data in line with Sweden. Data from the United Kingdom reveal 20% failure rate of brake systems. However, there is no indication of what part of that is attributable to tubing damage.
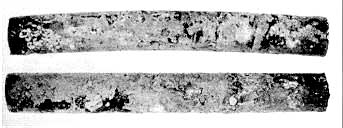
The Swedish data cover the period during which Volvo upgraded the material it used for brake tubing. Prior to 1971, Volvo had used terne coated steel tubing. In 1971 they changed the coating to zinc. The zinc coating was eventually supplemented by epoxy, and in 1976, Volvo adopted copper-nickel alloy C70600. In Figure 1, the performance of these four materials are compared on the basis of the percentage of observed occurrences of corrosion damage to brake tubing over 12 years of service. Copper-nickel is shown as the most reliable material by far.
Users of copper-nickel brake tubing in addition to Volvo include world-class vehicle manufacturers like Rolls Royce, Lotus, Aston Martin, Porsche and, most recently, Audi. Copper-nickel is also used in military, fire fighting and other heavy vehicles.
Back to TopAdded Cost Of Coatings
The steel tubing in predominant use is produced from continuous steel strip in the cold-rolled and annealed condition, which is formed into a fully-overlapped tube and copper brazed.
The introduction of steel tubing was coincidental with salting of roads as a means of clearing ice and snow and in anticipation of icy conditions. As steel tube alone does not have adequate corrosion resistance, it requires coating. Three coatings in wide use have been zinc, terne (lead and tin alloy with from 7%-14% tin) and epoxy.
Zinc Coating
Zinc has a low corrosion rate in neutral or alkaline environments. If the pH is less than 4, the corrosion rate is higher. In a crevice corrosion situation, pH drops, resulting in degeneration of the zinc and exposure of the copper brazing metal. Galvanically, copper is more noble than zinc, and once exposed, zinc corrosion accelerates. For example, if the steel is exposed due to damage to the coating from stone pecking or other penetration, the copper, being galvanically more noble, creates a large cathodic/ anodic area ratio that accelerates the corrosion of the steel resulting in perforation.
Terne Coating
Terne metal has good corrosion resistance, but once damaged it is also noble to the steel, and a large cathode/anode area ratio is created that accelerates corrosion of the steel.
Epoxy and Plastic Coatings
Epoxy and plastics (including teflon) are acceptable until perforated, whereupon localized corrosion of the underlying steel occurs. Perforation can result from stone pecking, from flaring, or when tightening nuts during installation
Other Types of Tubing
Coated seamless or welded steel tubing have been used, but once the coating is perforated, the problems are very similar to those of copper brazed steel tubing. Stainless steel has also been used, but has disadvantages in terms of susceptibility to localized pitting and crevice corrosion especially in chloride-containing environments.
With successive attempts to upgrade the performance of coatings, cost has been added to the manufacture of steel brake tubing.
In the late 1960's and 1970's, corrosion of motor vehicles was estimated to cost motorists nearly $500,000,000 in the United Kingdom alone. Brake tubing was a particular area of concern, so an alternative material was once again sought.
Back to TopThe Move To Copper-Nickel Tubing
Copper had been proved since the early days to have many good attributes. It was easy to bend and had very high corrosion resistance, but there was concern about its low corrosion-fatigue strength. When copper-nickel was introduced, it displayed corrosion resistance similar to copper, higher general strength and better fatigue strength. Good formability allows ease of flaring and bending, and although the metal cost is greater than that of steel alternatives, copper-nickel is very attractive in view of its extra life, trouble-free installation and safety/reliability characteristics.
Properties of Copper-Nickel Brake Tubing
The copper-nickel alloy used for brake tubing typically contains 10% nickel, with iron and manganese additions of 1.4% and 0.8% respectively. The product conforms to ASTM B466 (American Society for Testing and Materials), which specifies dimensions, tensile strength and yield strength. Formability and internal cleanliness conform to specifications SAE J527, ASTM A254 and SMMT C5B (Society of Motor Manufacturers and Traders). Also, the alloy meets the requirements for pressure containment, fabrication and corrosion resistance for ISO 4038 (International Standards Organization) and SAE J1047.
The mechanical properties of alloy C70600 in comparison with steel and copper are shown in Table 1.
Material | Ultimate Tensile Strength 1000 psi (MPa) | Yield Strength 0.5% Ext.under Load 1000 psi (MPa) | Elongation % in 2 in. | Fatigue Strength (10x7 cycles) 1000 psi (MPa) | Burst Pressure* 1000 psi (MPa) |
---|---|---|---|---|---|
Copper-brazed Steel | 48-55 (0.330-0.380) |
28-34 (0.190-0.235) |
30-40 | 30 (0.210) |
19.5 (0.135) |
C12200-Phosphorus deoxidized Copper |
32-38 (0.220-0.265) |
10-14 (0.070-0.100) |
45-60 | 10 (0.070) |
12 (0.083) |
C70600-Copper Nickel 90-10 | 48-54 (0.330-0.370) |
16-22 (0.110-0.150) |
40-55 | 15 (0.100) |
19 (0.130) |
* For typical 3/16 in.tubing, 0.187 in. (4.7 mm) o.d. and 0.028 in. (0.7mm) wall thickness. |
Alloy C70600 is normally supplied as redrawn tubing in the annealed condition. The combination of strength and good ductility give excellent formability.
As copper-nickel is softer than steel, it was first feared that fretting might be a problem. Experience has shown this is not the case.
Corrosion Resistance
For many years prior to its application as a brake tubing material, alloy C70600 had been used in ships, power station condensers and hydraulic lines on tankers, and had displayed excellent resistance to saline conditions. Early tests revealed that copper-nickel has almost the same resistance to burst pressure as steel. In testing, however, when exposed to salt spray over 180 days, steel's burst strength decreases significantly. The copper alloy remains consistently resistant.
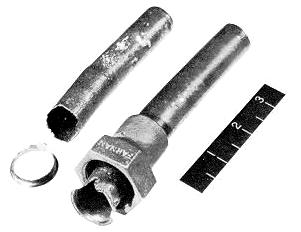
For tubes covered with a moist, salty mudpack for six months, brazed steel was severely corroded resulting in perforation of the tubing wall; whereas, only superficial general corrosion was found on the copper-nickel tubing. ISO 4038 and SAE J1047 include a corrosion resistance requirement referring to ISO 3768 asking for a minimum burst pressure of 110 MPa after 96 hours in neutral salt spray. Swedish requirements include a resistance at least equal to 25 of zinc. In all cases alloy C70600 easily exceeds the required corrosion resistance.
Back to TopThe Right Tubing For The Job
Even the best tubing will be unsatisfactory unless it is used properly. The following considerations are necessary for establishing the specifications for brake system tubing installations:
- Since tubing may suffer damage and/or loss of corrosion resistance as a result of gravel impact, it should be adequately protected in areas of potential damage.
- Tubing should be adequately protected against hoist or towing fixture damage.
- Tubing should be routed or otherwise protected so that under no condition can the tubing or its protective conduit come in contact with any vibrating or moving component. (That is, if the tubing is attached to the frame, the underbody is considered to be a "vibrating component.") The tubing should never intersect an exhaust pipe, muffler or catalytic converter, unless it is adequately protected against excessive movement of the pipe, muffler or catalytic converter, even if a hanger failed.
- Tubing should be routed so that its stress limits will not be exceeded during flexing.
- Tubing should be routed so that it will not be in or form a pocket that will trap salt or other de-icing chemicals.
- Tubing should avoid or be protected from exhaust systems or other areas of extreme heat.
- The design engineer should take into account possible electrolytic corrosion resulting from contact between dissimilar metals, for example, brake tubing and protective conduit, clips, fittings and mounting surfaces.
- The design engineer should determine the brake tubing's minimum inside diameter based on brake system actuation time. The factors affecting actuation time are:
- Brake fluid viscosity,
- Operating temperature,
- Tube length, and
- Fluid flow rate as determined by wheel cylinder displacement requirements.
Copper-nickel brake tubing provides superior reliability and assures both manufacturers and vehicle owners improved durability for effective long-life functioning of the brake system.
Back to Top