Electric Motors with High Temperature Cuprate Superconductors in the Rotor
Copper Applications in Electrical Applications
- Introduction
- Superconductors
- Electric Motors and Cuprate Superconductors
- Hysteresis Motors
- Synchronous Reluctance Motors
- Trapped-field Synchronous Motors
- Future Prospects
Introduction
The benefits of using copper, with its excellent electrical conductivity, for the stator windings of an electric motor have been recognized for many years. This article describes recent developments on the incorporation of bulk high-temperature superconductors (HTS) into the rotor to improve their performance and increase the overall power density. It might be expected that the use of superconducting windings in the stator would offer further savings, but these are more than offset by the difficulty of fabricating the present ceramic HTS materials into suitable windings. The current preferred option is, therefore, the use of copper windings in conjunction with HTS rotors. The HTS materials operate at liquid nitrogen temperatures, and therefore it is anticipated that these new motors will find their first applications where the environment is already suitably cold, for example, in space and for pumping cryogens (e.g. liquid hydrogen fuel for future vehicles). As further improvements are made, more applications will befound.
Back to TopSuperconductors
When cooled below their critical temperature, T c, superconductors can carry large currents without any dissipation of resistive (I 2R) heating, i.e., the superconductors exhibit essentially zero resistivity. Apart from the obvious benefits of being able to transport electrical current without loss of energy, these materials also have important magnetic properties. Before 1986, all known superconductors exhibited critical temperatures near absolute zero, -273C (-460 F) meaning that they had to be cooled by liquid helium to exhibit superconducting properties. Cooling with liquid helium is difficult and expensive and, consequently, superconductivity found few engineering applications outside the laboratory, until recent years, that is.
This situation was transformed in 1986, when Bednorz and Muller discovered that a copper oxide-based ceramic with a perovskite structure became superconducting at a much higher temperature than any superconductor known until then. This discovery was quickly followed by the identification of other cuprate-based ceramics with even higher critical temperatures. One of the best known of these so-called high-temperature superconductors is an yttrium-barium-copper oxide compound (known as YBCO) discovered by Wu in 1987. It has a Tc of 93K (-292 F, -180 C), which is higher than the boiling point of liquid nitrogen. Liquid nitrogen is relatively inexpensive and much easier to handle than liquid helium, and this happy phenomenon allows the new copper-oxide, or cuprate superconductors, as they are sometimes called, to be considered for applications that were not viable with earlier superconductors.
Back to TopElectric Motors and Cuprate Superconductors
An electric motor consists of two basic components, a stator and a rotor. The stator consists of a hollow cylindrical winding connected to an AC power supply to create a rotating magnetic field. The rotor sits inside the cylindrical stator and tries to align itself with the magnetic field to achieve a position of minimum field energy. The result of this interaction is the generation of a torque that acts on the rotor, causing it to spin.
There have been many variants on this basic design, both to improve the efficiency of the motors, i.e., increase the ratio of the generated torque to the power consumed and also to develop specialized motors for particular applications. Over the past decade, a number of research teams have explored the use of HTS materials to make electric motors more efficient and powerful than the ones currently available. Important properties of these materials that can be exploited are their hysteretic nature, i.e., their ability to shield and direct magnetic flux and their capability of trapping large flux densities. These properties translate to hysteresis motors, reluctance motors and trapped-field synchronous machines, respectively, all being brushless devices that require no contacts on the rotor.
Back to TopHysteresis Motors
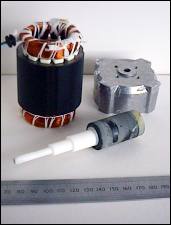
Hysteresis motors have a very simple construction. They produce a steady torque even at low speeds and thus provide good starting properties when loaded. Figure 1 illustrates the conventional copper wound stator and a YBCO rotor of a prototype superconducting hysteresis motor.
The cylindrical rotor is placed in the stator, whose field induces currents in the superconductor giving rise to a magnetized rotor. HTS materials are especially beneficial for this type of motor because they are intrinsically hysteretic, implying that the magnetic flux cannot move freely throughout the material causing the magnetization and stator fields to be misaligned and, thereby, resulting in a large alignment torque.
Computer modeling of hysteresis motors suggests that alternative rotor designs can give additional benefits. For example, only a thin-walled tube of HTS is required for optimum power output, and the tube can be constructed from longitudinal segments of the HTS material. These design modifications considerably reduce the amount of HTS required, but by being able to utilize and join thin segments of the material, it is possible to assemble a rotor of large diameter. Since, in a motor, torque is proportional to the cube of the diameter of the rotor, light weight but high power motors could be easily constructed.
Back to TopSynchronous Reluctance Motors
The alignment of iron artifacts in magnetic fields is a common experience, for example, when a magnet is brought near to a pile of nails. This phenomenon forms the basis of a reluctance machine in which the axis of a suitably shaped iron rotor tends to align with the rotating field of the stator. The rotor therefore spins at the same speed as the stator field and forms a synchronous machine. The torque for a motor can be realized by allowing an easy magnetic path (low reluctance) along one axis of the rotor, known as the direct axis, and a difficult route (high reluctance) along the axis perpendicular to this, known as the quadrature axis. This effect can be achieved by simply using an iron rotor that is elongated in one direction, as illustrated in Figure 2.
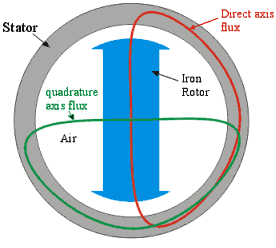
Magnetic flux traversing the direct axis meets little reluctance because iron has a high magnetic permeability, whereas flux traversing the quadrature axis must cross the large air gaps that have a higher reluctance. Magnetic flux barriers can be used to further increase the reluctance along the quadrature axis, and the magnetic shielding properties of superconductors are ideal for this purpose. Figure 3 shows the effect on the field distribution of adding two HTS components on either side of the rotor.
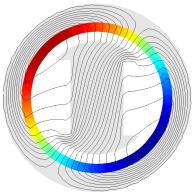
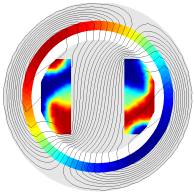
Currents are represented by the colors, blue = largest current into plane, red = largest out of plane.
The currents induced by the stator field in the HTSs oppose the field, thus almost completely preventing flux from passing through the rotor in the quadrature direction. Increasing the amount of flux passing along the iron axis and decreasing that in the perpendicular direction increases the alignment force and results in a more powerful motor.
Reluctance motors incorporating YBCO blocks with powers up to 20kW have been constructed by Oswald Elektromotoren GmbH, Germany, Figure 4. Preliminary results show an increase of the power output of up to 50% for the superconductor-enhanced motor.
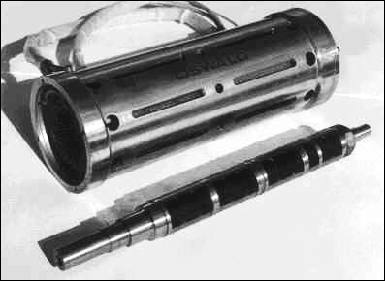
Trapped-field Synchronous Motors
The power and efficiency of electric motors can be increased if there are sources of magnetic flux both on the stator and on the rotor. This can be achieved by incorporating into the rotor either permanent magnets or energized coils acting as electromagnets. For optimum performance, the magnetic field on the rotor should be maximized, and superconductors can provide much higher magnetic fields than conventional permanent magnets, which are limited to roughly 1.5 T. Magnetized superconducting materials also have an additional advantage over field windings, since no electrical connections are necessary. This simplifies construction.
Magnetic flux can be trapped within high-temperature superconductors by cooling through the transition temperature in the presence of an external magnetic field. On removal of the external field, currents still flow in the superconductor and re-create the field that previously existed. The material with its trapped magnetic field can be used like a permanent magnet. Another method of trapping a magnetic field in a HTS is to simply apply a large magnetic pulse while the material is in the superconducting state. When the pulse has passed, a field remains trapped in the superconductor.
Motors of this type have not yet been realized in practice, but computer modeling has indicated that large power densities are achievable provided that the superconductors can be sufficiently magnetized. In particular, by modifying the rotor of a reluctance motor so that the superconductors can be magnetized, the power output could theoretically be increased by up to 10 times for small stator fields. It is anticipated that motors of this type will be constructed in the near future to validate the predictions of the modeling.
Back to TopFuture Prospects
Although the prototype electric motors incorporating copper-based HTS materials are not yet suitable for commercial applications, the performance benefits that can result from the use of these materials has been satisfactorily demonstrated. Applications for these high performance motors are already being considered and patented, e.g. as pumps for pumping cryogens.
Development efforts are continuing in many laboratories throughout the world, and improvements to both the design of the motors and to the manufacture, fabrication and properties of HTS materials that are anticipated over the next few years, can be expected to make these copper-based superconducting motors a commercial reality.
Also in this Issue:
- Copper-Nickel Alloys - Marine Supreme: Introduction
- Copper-Nickel Alloys - Marine Supreme: Types of Copper-Nickel Alloy
- Copper-Nickel Alloys - Marine Supreme: Resistance to Corrosion and Biofouling
- Copper-Nickel Alloys - Marine Supreme: Fabrication
- Copper-Nickel Alloys - Marine Supreme: Applications Information
- Copper-Nickel Alloys - Marine Supreme: Website Articles
- Copper-Nickel Alloys - Marine Supreme: Other References
- Copper-Nickel Alloys - Marine Supreme: Illustrations
- Medical Uses of Copper in Antiquity
- Electric Motors with High Temperature Cuprate Superconductors in the Rotor