Research on Copper Joining Techniques Evaluates New Designs and Brazing Methods
Copper Applications in Innovative Technology
This document is reprinted, with permission from Tech Update, November 1998, copyright Air-Conditioning and Refrigeration Institute
Introduction
This article summarizes the results of the second part of a two-part research effort undertaken at Amalgamated Technologies Incorporated (ATI), sponsored by ARI and Copper Development Association (CDA). The objective of Part 1 was to determine whether current braze joining technology for copper tubing is adequate for the higher operating pressures of alternative refrigerants proposed for future usage (see New Research Program Focuses on Improvements for the 21st Century ).
The objective of Part 2 was to ascertain whether experimental braze joint designs and alternate braze heating methodologies can economically provide improved brazing quality and higher product performance. See below for information on obtaining a copy of the final report.
The Part 1 research indicated that current brazing technology is capable of high quality brazed joints that likely can meet the requirements of the industry in the future. However, the research indicated that some minor aspects of current technology could be modified or improved to result in significant gains in refrigeration product quality. The researchers speculated that tube joints made with less female socket depth relative to tube diameter, i.e., less overlap, would allow more effective brazing, thus improving the leak-tightness of the joints in each system, and raising product performance above and beyond that attained with current practice. The Part 1 report further speculated that an alternate heating method, which heats more rapidly and consistently than a conventional gas torch, would also increase braze joint integrity and performance.
In Part 2 of the research project, ATI tested both of these theories. The research indicates that more rapid heating does in fact improve braze joint integrity and strength over that attained with slower heating. The research also indicates that tube joint designs with less overlap do braze faster and more effectively with both slower and faster heating.
Methodology
Testing involved two heating methods. The "conventional" heating method was an acetylene gas torch, and the "alternate" heating method for more rapid heating was an industrial 2,500 watt inductive brazing unit.
The intent of the work was to evaluate these two heating methods and various joint designs for brazed joint strength, endurance, and relative ease of brazing. In equipment applications, sound joints are considered those that do not leak or develop leaks during normal operation. For the accelerated testing of Part 2, braze integrity of the various joint designs was assessed by mechanically testing for static burst strength and cyclic stress endurance. Because the Part 1 project demonstrated that braze joint performance is determined largely by the degree of braze filler metal penetration throughout the overlap region of a tube-in-socket joint, the integrity of the braze joints was also evaluated under that criteria.
Two braze filler metals were selected: AWS BCuP-2 braze alloy, 0% silver, copper-phosphorus, and AWS BCuP-3 braze alloy, 5% silver, copper-phosphorus. Both 5/16" (8 mm) and 3/8" (9.5 mm) tubes were tested, each with and without fins.
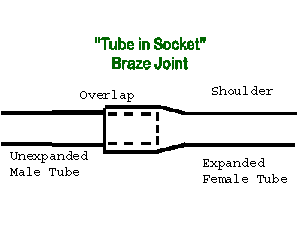
The four types of tubing were configured into two types of test samples, depending on the test procedure used. Each sample contained at least one "tube-in-socket" joint, where one tube is expanded to form a female socket, to allow an unexpanded tube to slip inside and form an overlapping joint as shown in Figure 1. The two types of test samples are shown in Figure 2.
Tubing samples tested in Part 1 were supplied to ATI by the manufacturer with a shoulder angle of approximately 15º, and an overlap ratio of 150% of the diameter. This became the definition of a "conventional" joint design for Part 2. The experimental joint designs of Part 2 employed three different shoulder profiles and three different overlap ratios, as shown in Figure 3.
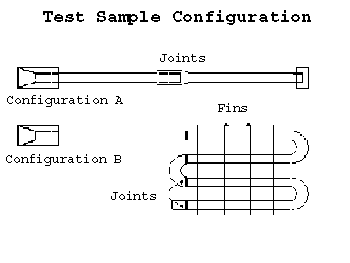
Three test procedures were utilized: static burst pressure, vibration cyclic fatigue life, and pressure cyclic fatigue life. The cyclic fatigue tests were performed at three different stress levels to establish stress-vs-life behavior of the brazed samples.
Every braze joint of all designs and both heating methods had complete filler metal penetration, indicating that all joints were expected to perform well. There was no clear difference between the joint designs in terms of ease of brazing, as would be indicated by varying degrees of filler penetration. Optimum braze technique with both heating methods resulted in consistently good joints, which negated the relative differences in brazability between the various designs.
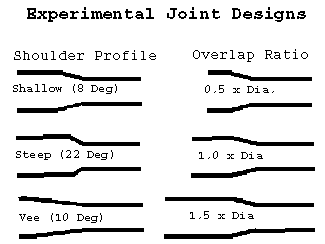
However, there were differences between the sample groups in terms of average burst pressure. Samples brazed with the inductive heater averaged five to eleven percent higher burst strength than corresponding samples brazed with the gas torch. This was due to the fact that the inductive heater made each joint in one-third the time or less, compared to the gas torch. Reduced braze time resulted in less annealing and less grain growth in the copper material, allowing the tube to retain more of the work-hardened strength imparted from swaging.
Also, joints with shorter female sockets (less overlap) heated faster than joints with longer overlap, for both heating methods. Under the gas torch heating method, the shortest joints brazed 12 to 15 percent faster and had higher static burst strength, compared to the longest joints. There was no difference in average burst strength between the three overlap lengths for inductive heated samples, because the inductive heater brazed all joints so quickly, nor was there essentially any difference in burst strength between the three shoulder profile groups. Even the Vee profile joints, with overlap engagement of only 25% of the diameter, achieved the full strength of annealed tubing itself, again due to proper braze technique more than inherent brazability.
The joint design determined to be the "best" was the steep shoulder profile, with an overlap ratio of equal to the diameter. This design was selected because it was consistently at or near the highest average burst pressure, and also because it was compact and easy to fixture, and would likely be preferred in a factory environment.
The researchers constructed additional samples with this joint design using both heating methods and braze alloy BCuP-3, to determine if there would be any change of brazability with this filler metal. Alloy BCuP-3 contains 5% silver, and is less fluid within capillary spaces than alloy BCuP-2. These tests showed that all BCuP-3 samples had full penetration joints and strength equal to samples with alloy BCuP-2, with no reduction of brazability.
Vibration fatigue behavior of brazed joints was determined using an apparatus which mechanically induced a vibration-like motion in the samples while recording elapsed time. Configuration A samples with the best joint design, as concluded by static burst testing, were made with both heating methods and alloy BCuP-2.
Samples with the new joint in 3/8" tubing lasted longer than the conventional joints of Part 1 in three out of six groups. However, samples with the new joint design in 5/16" tubing lasted longer than the conventional joints in five out of six groups. At the lowest stress levels, the Part 2 joins lasted 475% to 652% longer than joints of Part 1.
Inductive heated samples lasted longer than gas torch heated samples in eleven out of twelve vibration sample groups. This is because metal with higher hardness and yield strength can bend more without yielding, and therefore has greater fatigue strength and longer cyclic stress endurance. As was seen in the burst testing, fast inductive heating results in less annealing of the copper and thus higher yield strength.
The primary conclusion from vibration fatigue testing is that the new joint design worked as well or better than the conventional design in most cases. In addition, samples brazed with the inductive heater were distinctly better than gas torch heated samples for this particular test.
Pressure Cyclic Fatigue Testing
Pressure cyclic fatigue behavior was determined using an apparatus which rapidly pressurized and depressurized samples to simulate pressure cycling effects of refrigeration system operation. Testing was limited to 5/16" and 3/8" Configuration B coil tubing samples only. ATI's prior experience with this test indicates that the most useful data is generated by pressure cycling at 70 to 95 percent of the static burst strength of the test coils. Prior experience also shows there can be considerable quality variation between coil production runs, so it is necessary to determine the static burst strength of each set of test coils before pressure cyclic testing can begin. For example, one set of coils supplied for Part 1 testing had mechanical score marks on the tubing from coil forming operations, and had 15% lower static burst strength than another batch of coils made without score marks. Thus in order to generate comparable pressure cyclic fatigue test data between different coil production batches, it is necessary to first determine the static burst strength of each batch.
As was observed on some Part 1 coils, the coils supplied for Part 2 had severe score marks from coil forming machines. [Note: score marks and other mechanical deficiencies were present on coils used in this project. These marks were due to manual coil forming operations, and would not normally be incurred in production heat exchangers.] Because of the presence of score marks, it was a big surprise when the new Part 2 coils showed a tremendous increase in static burst strength over the static burst strength of coils tested in Part 1. The 5/16" coils supplied for Part 2 were 30% stronger than the Part 1 coils, and the 3/8" coils supplied for Part 2 were 63% stronger than the Part 1 coils. The only difference between the Part 1 and Part 2 coil batches was that the open ends of the hairpin tubes of the new coils were shorter in length than the tubes of the Part 1 coils. The Part 1 coil tubes of both 5/16" and 3/8" coils protruded 1.0 inch from the end sheet, while the Part 2 coil tubes of both sizes protruded only 0.5 inch from the end sheet.
Pressure cyclic testing was then performed with cyclic pressure at 60, 70 and 80 percent of the measured burst strength for the Part 2 coils of both tube sizes and both heating methods. Because the Part 2 coils had higher static burst strength than prior testing, the cyclic pressure levels were correspondingly higher as well.
In spite of severe score marks, the Part 2 coils lasted much longer than Part 1 coils at equivalent pressure levels. For example, 3/8" Part 2 coils lasted for 300 more pressure cycles at 1,478 psi than equivalent Part 1 coils lasted at that pressure. The Part 2 coils had significantly higher burst strength, longer fatigue endurance, and braze joints that were actually stronger than the rest of the coil. All three of these improvements over the Part 1 coils are credited to the reduced tube protrusion length from the end sheet of the Part 2 coils. Reduced protrusion length results in less unsupported tubing between the end sheet and the braze joint, and greatly enhanced coil properties.
However, reduced tube protrusion made brazing more difficult, because the braze joints were in closer proximity to the coil. Shorter tube protrusion results in a greater heat-sink effect from the coil, causing brazing to take approximately twice as long as the coils with longer protrusion, for both heating methods. This suggests that there may be an optimum protrusion length for each coil design. Densely packed, multiple row coils may need longer protrusion to ensure the inner rows of tubes are effectively heated. Narrower or low density coils will effectively braze with less tube protrusion, and could take advantage of higher burst strength and fatigue life from the shorter tubes.
Both types of heating were used, but there was no difference between them in pressure cyclic fatigue life. The inductive heater was hindered by the close proximity of the steel end sheets. As a result, brazing took the same amount of time for both methods, leading the researchers to conclude that coil heating is a less suitable application for the inductive heater.
Conclusions
This study confirmed the conclusion of the Part 1 effort that full braze filler metal penetration of the joint is essential to optimum joint and system performance. The authors propose that a full filler penetration throughout the overlap region should become the industry definition of a good joint.
Conventional brazing technology is capable of producing high quality joints. However, there is potential to further raise quality and performance of refrigeration products in the future. This study indicates that reduced joint overlap can enhance brazability for all joints and heating methods. The report also shows that a fast, consistent heat method, such as that produced by the inductive brazing unit, can more effectively produce full penetration joints in suitable applications.
Summary of ATI's Conclusions
Static Burst Test
- Inductive heating delivered faster brazing and higher burst strength with each joint design.
- Joints with less overlap heated faster with both heating methods. This resulted in burst strength gains for gas torch heated samples, but no additional gains for inductive heated samples.
- Joint profile and shoulder angle had little or no effect on brazing properties and strength.
- The combination of steep shoulder angle and 1.0 x diameter overlap was selected as the "best" joint design for several reasons. The "best" joint worked equally well with alloy BCuP-3.
Vibration Cyclic Fatigue Test
- Inductive heated samples lasted longer than gas heated samples in 11 out of 12 groups.
- The Part 2 "best" joint design lasted longer than the conventional joint of Part 1 in eight out of twelve sample groups.
Pressure Cycling Fatigue Test
- Coil tube protrusion length from the end sheet greatly affects performance. Less protrusion results in much higher static burst strength and cyclic fatigue endurance.
- Reduced protrusion length also results in more difficult brazing, which suggests a coil design tradeoff between higher strength and uniform braze joint quality.
- The inductive heater proved less suitable for coil joint brazing.
Other Observations
- The inductive heater brazed each joint for 6% of the energy cost, and three times faster than the acetylene torch.
- Coil quality and braze performance is compromised by mechanical tube damage and heavy oil contamination.
How to Get the Report
Scott A. McCracken, Roy E. Beal (Amalgamated Technologies Inc.), Evaluation of Joining Techniques for Copper Tubing in AC&R Applications - Part Two, October 1998. Copies can be ordered from: ARTI Database c/o James M. Calm, Engineering Consultant, 10887 Woodleaf Lane, Great Falls, VA 22066-3003 (reference RDB8B01).
Also in this Issue:
- Alloy 171 for Electronic Interconnects
- Copper's Role in the Safe Disposal of Radioactive Waste: Copper's Relevant Properties - Part I
- Q & A With Hans-Erhard Reiter of the ADSL Forum
- Copper and Aquatic Life
- Research on Copper Joining Techniques Evaluates New Designs and Brazing Methods