Download in PDF format [541 Kb]
- Company Policy Stresses Efficiency, Reliability
- OEM Equipment: the Hidden Opportunity
- High Turn-down Ratio Important
- Power Quality Issues Avoided
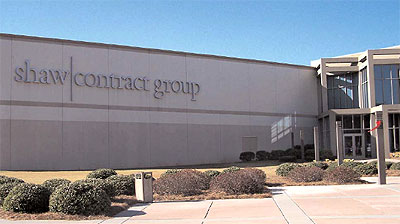
Q: What do you do when (a) you want to reduce your company's energy costs, (b) you understand premium- efficiency motors will do that, and (c) in fact, your company already has a sound policy with respect to motors, but much of your highly specialized equipment requires motors that don't fall under NEMA Premium efficiency mandates … or even EPAct, for that matter.
A: Obviously, you reduce energy consumption with premium- efficiency motors wherever you can. Then you make high efficiency a key part of your purchase decision in other situations. That's exactly what America's leading carpet manufacturer does, and they're saving money every day.
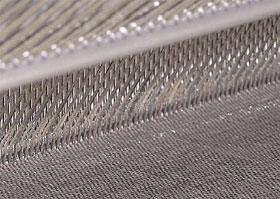
The Contract Division designs, weaves and processes carpeting to a finished product. Other divisions of the highly integrated parent company make the polymer raw materials, spin or extrude them into yarn, and make dyes and various types of backing materials.
Almost all of those operations are motor-driven, so they all consume electrical energy. That's where copper comes in.
Why is copper important? Because, other factors being equal, the efficiency of any electric motor depends to a large extent on the amount of copper it contains. The more copper found in the motor's windings, the lower the resistive (I²R) stator losses and the higher the efficiency.
If you want to save your company a lot of energy quickly, motors are the first place to look. The Department of Energy estimates that electric motor-driven systems account for 23% of all electricity sold in the USA and almost 2/3 of all electricity consumed in industrial settings.1 Shaw's Contract Division fits that profile. True, natural gas (mainly for drying operations) is the division's largest single energy burden; but, on the electrical side, the skeining, spooling, tufting, warping and coating machines found in the company's 321,000-sq-ft Plant 13 in Cartersville, alone, contain more than 135 motors in sizes between 2 hp and 50 hp. Other motors, in sizes up to 150 hp, drive air compressors and circulating fans. There are even more large motors at the nearby million-square-foot Plant 15, and there are “hundreds” of fractional-horsepower motors at both plants, according to Jerry Zolkowski, P.E., demand-side engineering manager for the Shaw Industries Group's energy division. Reducing the company's energy costs is Zolkowski's primary responsibility.
Back to TopCompany Policy Stresses Efficiency, Reliability
“Shaw Industries has had a formal motor purchase and replacement policy in effect for a number of years,” says Zolkowski, pointing out that the policy's stated objective is straightforward: “to save on energy costs by buying premiumefficiency AC motors instead of rewinding existing AC motors when certain circumstances are met.”
“Among other things,” he explains, “those 'certain circumstances' give plant managers options in dealing with motors that fall outside the NEMA Premium2 motor standard.”
Otherwise, the policy is pretty clear-cut. Here are a few excerpts:
1. “Replace all AC motors smaller than 20 hp with premium- efficiency motors when the windings fail. If only the bearings fail, then the motor should be repaired, unless the plant engineer deems that it is necessary to replace the motor for other reasons, such as a need for higher horsepower.”
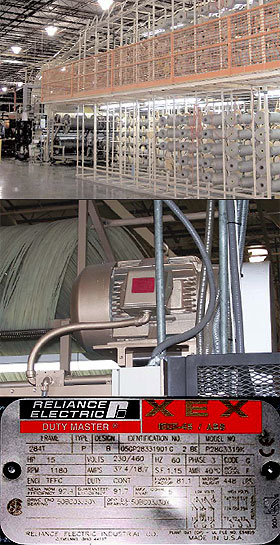
Operating continuously at 75% load for 50 weeks per year, those two premium-efficiency motors, together, save Shaw 11,448 kWh per year in energy and reduce its annual utility bill by $666.4 That amount might appear modest in terms of the division's overall budget, but keep in mind that it is a nearly free savings, since the motors paid for themselves in only 1½ years. Everything from then on is gravy. The savings will continue year after year over what could very well be the motors’ 20-year service life. In addition, the two premium-efficiency motors reduce carbon dioxide emissions at the City of Cartersville Electric generating plants by 17,744 pounds per year.5 That keeps the plant’s neighbors happy and credibly underscores Shaw’s commitment to environmental responsibility.
2. “For AC motors between 20 hp and 300 hp operating between 16 hours and 24 hours per day:3. “For AC motors (20 hp to 300 hp) running 8 hours to 16 hours per day: upon failure these AC motors will be replaced if the payback is less than two years.”
- Rewinding may be performed a maximum of three times. But,
- If the rewind cost is 60% or more of the cost of a premium-efficiency motor, then a new premium efficiency motor shall be purchased.
- When a motor has already been rewound up to twice before, the motor will be replaced if the payback is less than two years using Shaw’s payback equation.
Consider the following situation using Shaw’s motor policy. If a 25-hp, standard-efficiency motor operating at 75% load operates (a) 8 hour/day, (b) 16 hours/day or (c) 24 hours/day, do you repair or replace it? To determine this, we’ll compare rewinding the old motors with new premium efficiency Reliance Electric XE Duty Master ® motors such as one that drives a coating line at Shaw Contract’s Plant 15, Figure 3.
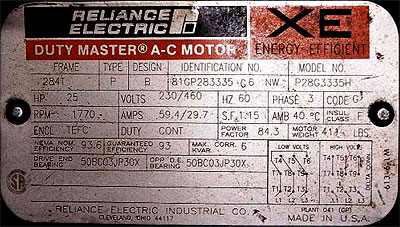
We’ll calculate payback using MotorMaster+, the versatile and easy-to-use software developed by the U.S. Department of Energy.6 Among many other things, MotorMaster+ enables users to compare the annual and lifecycle costs of new, premium-efficiency motors with the cost of rewinding and continuing to use old standard-efficiency models. We’ll assume (just like the DOE software does) that the existing motor would suffer a 2% loss in efficiency due to rewinding.7 Utility rates, duty cycles and load factors remain the same as those given in the earlier example.
MotorMaster+ indicates the old 25-hp motor will cost $660 to rebuild. The rewind cost is therefore 72% of the cost of a new premium-efficiency motor, assuming a nominal 50% discount off the list price. That satisfies the 60% rule in Shaw’s motor policy. But even if it didn’t, could the company still justify replacing the old motor? Easily! The numbers are shown in Table 1.
Rewind Standard Eff. Motor | New Premium Eff. Motor | |
---|---|---|
8 h/day (2800 h/y) Operation, at $0.058 per kWh | ||
Efficiency at 75% load | 87.9% | 94.1% |
Cost | $660 | $921* |
Energy Use, kWh/y | 44,551 | 41,621 |
Energy Cost/y | $2,584 | $2,414 |
Annual Savings | $170 | |
Simple Payback | 1.53 y | |
16 h/day (5600 h/y) Operation | ||
Efficiency at 75% load | 87.9% | 94.1% |
Cost | $660 | $921* |
Energy Use, kWh/y | 89,102 | 83,241 |
Energy Cost/y | $5,168 | $4,828 |
Annual Savings | $340 | |
Simple Payback | 0.76 y | |
24 h/day (8400 h/y) Operation | ||
Efficiency at 75% load | 87.9% | 94.1% |
Cost | $660 | $921* |
Energy Use, kWh/y | 133,653 | 124,862 |
Energy Cost/y | $7,752 | $7,242 |
Annual Savings | $510 | |
Simple Payback | 0.51 y | |
*Discounted cost of new motor. |
Even a motor operating as few as eight hours per day would pay back its investment in less than two years compared with the cost of rewinding an old, standard-efficiency unit. That’s how valuable premium efficiency is.
Here’s the reason: Electric motors that operate at high duty cycles can consume 10 to 25 times their purchase price in electrical energy costs per year.8 Cutting a motor’s operating costs by even a few percent — by installing a premium efficiency model — shortens payback remarkably. Smart facilities managers know that first costs are insignificant when it comes to electric motors; it’s life-cycle costs that matter.
Back to TopOEM Equipment: the Hidden Opportunity
Shaw’s motor policy includes several more provisions that other facility managers or plant engineers might find useful. One to note is:
4. New motors purchased through this AC motor policy or on new jobs/projects will be premium-efficiency (P.E.) instead of standard-efficiency. Note: Item 4 applies to motors that range in size from 1 hp to 200 hp. For motors over 200 hp, the plant engineer will have to be concerned with the motor frame size.
This is a very important provision. Although it doesn’t specifically deal with components of machinery, in practice, it permits plant managers to insist that the new OEM equipment they buy must be fitted with premium-efficiency motors whenever technically feasible. Equipment manufacturers might not be used to that sort of request. They might not even like it because it could increase their costs a little, but they will comply if the customer insists. Shaw does.
Back to TopHigh Turn-down Ratio Important
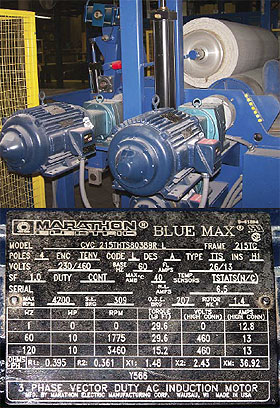
In another of its successful energy-saving programs, Shaw’s Contract Division replaced the dc motors on its coating and inspection lines with inverter-duty-rated AC motors powered through variable frequency drives (VFDs). Plant 13’s plant engineer, Jerry Tidwell, explains: “We need motors with variable-speed capabilities here because the lines often need to be driven at speeds as low as 10 ft/min, which translates to 1–2 rpm on the motors. We used to do that with DC motors, two of which would fail every year. The new AC motors are much more reliable, and none has failed yet. However,” he quickly adds, “another important reason for the changeover was to reduce energy consumption. Inverter-duty motors equipped with VFDs will do that.”
Unfortunately, inverter-duty motors do not fall under NEMA Premium standards. Shaw engineers and plant managers want motors with turn-down ratios as high as 2000:1, and, even if they couldn’t buy motors with NEMA Premium efficiency levels, they’d try to get close. They found that the Marathon Blue Max® vector-duty line, and, for some applications, comparable Leeson and Toshiba models are best suited their needs.
The two 10-hp inverter-duty motors shown in Figure 4 operate part of the coating line in Shaw Contract Divisions Plant 15. They are rated at an efficiency of 91.0%, which is not quite premium-efficiency level, but its as close as it can possibly be for this type of motor. (The minimum nominal efficiency for a general-purpose, 10-hp, 1800-rpm NEMA Premium motor is 91.7% at 100% loading.) In fact, the difference in efficiency between the inverter-duty motors shown in the figure and a NEMA Premium motor of the same size would yield an annual savings of only $23.
Back to TopPower Quality Issues Avoided
Chuck Willis and Stacy Adams, engineers responsible for equipment at Plant 15, must not let the VFDs interfere with front-office operations. “The VFDs on our drive motors generate a lot of harmonic distortion,” says Mr. Willis. “We have to keep that electrical noise out of the front office, or it could harm the computers and office equipment. As a result, we install a lot of isolation transformers, and they’re all copper wound.”
Jerry Zolkowski sums up his company’s position well: “Our corporate policy emphasizes premium-efficiency motors wherever possible. It takes into account that not all of our motors will fall under the NEMA Premium standard, and so it gives our plant managers the flexibility they need while still making sure we save energy. It’s a common-sense approach that works well for us.
It makes a lot of sense to us, too, Mr. Zolkowski. It’s motors that really make the difference when it comes to saving energy.
Making a Motor Decision that Matters Is as Easy as 1-2-3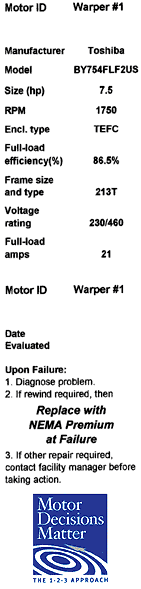
The repair-or-replace options presented in this case study were analyzed using MotorMaster+, the popular DOE software that is used by many facilities engineers and energy professionals. But another alternative for those who want to estimate potential NEMA Premium installations is the 1-2-3 Approach to Motor Management.
Like MotorMaster+, 1-2-3 is user-friendly software designed to help make motor repair-or-replace decisions, but it uses a number of simplifying assumptions and is more limited in its capabilities. The program was developed by Motor Decisions MatterSM, a national campaign educating industrial managers about the significant bottom- line benefits of sound motor management. The campaign is co-sponsored by the Consortium for Energy Efficiency and its partners, including CDA Inc.
To apply 1-2-3, users insert the utility rate, usage data and information taken from the dataplate of the motor in question, along with similar information for candidate EPAct and/or NEMA Premium replacement models (unlike MotorMaster+, 1-2-3 does not have a database of motor characteristics). The software then calculates annual energy costs for retaining the old motor in service, rewinding and retaining the motor, replacing it with an EPAct motor and/or a NEMA Premium motor, respectively. The software also calculates, for the two replacement options, annual energy savings in dollars, percent return on investment for the new motor, and the simple payback period in years, and prepares detailed spreadsheets for presentation to management.
Finally, 1-2-3 prints double-sided tags to be attached to the old motor, instructing service technicians what to do when the motor fails. An example of such a tag for one of Shaw Contract's 7.5-hp motors is shown at left.
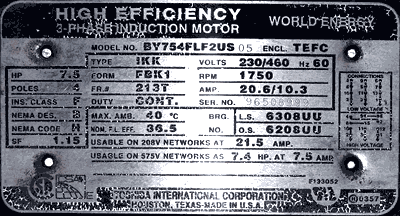
The Principals
Jerry Zolkowski, P.E., is demand-side engineering manager for the Energy Division of Shaw Industries Group, Inc., the parent organization of the Shaw Contract Division. Zolkowski is based in Dalton, Georgia and can be reached at 706-275-4750, Fax 706-275-4865, jerry.zolkowski@shawinc.com.
Jerry Tidwell is plant engineer at the Shaw Contract Division Plant 13 in Cartersville, Georgia. He can be reached at 770-387-8706, jerry.tidwell@shawinc.com.
Stacey Adams is senior automation engineer at the Shaw Contract Division Plant 15 in Cartersville. He can be reached at 770-387-8881, stacey.adams@shawinc.com.
Footnotes
See US Department of Energy and CEE sites for additional information.
As used in this article, the term: “premium-efficiency” refers to motors conforming to NEMA MG 1-1998 (Rev. 3), Tables 12-12 and 12-13. Use of the trademarked NEMA Premium identification and label is voluntary, even among NEMA members, and lack of a NEMA Premium label does not necessarily mean a particular motor does not meet the standard.
Shaw's motor policy permits managers freedom to select the brand and model of premium-efficiency motors. While a Reliance motor is shown in Figure 2, Marathon XRI and Toshiba EQP3 , among others, are also used in Shaw facilities.
Calculated using MotorMaster+ for known duty and load factors and Shaw's current utility rate of $0.058/kWh.
Based on 1.55 lbs CO2/kWh, the national average based on U.S. Department of Energy reports.
The software is available by request at AMO Tools Help Desk.
Rewinding a motor can never result in efficiency ratings that are higher than those of the original equipment. At best, efficiency will match the original rating. An efficiency loss of between 1% and 2% is not uncommon.
See CEE site for further information from the Consortium for Energy Efficiency, a nonprofit public benefits corporation whose North American members promote the manufacture and purchase of energy-efficient products and services.
Premium-efficiency motors may have characteristics different from standard- or EPAct-efficiency motors, such as starting current, torque, speed, etc. All engineering parameters must be taken into account when considering replacement.