Out-of-sight, out-of-mind. That's the phrase that comes to mind for all who have installed copper and copper alloy piping systems in buried, underground applications. An expectation well supported by the excellent corrosion resistance of copper alloys used in these applications. An expectation that may not be realized when this out-of-site, out-of-mind philosophy extends to the practices used in installing the system.
While little is written regarding the proper installation of buried copper and copper alloy piping systems, many existing plumbing codes make an attempt to address the issue. Though generally the text found in most of the major model plumbing codes falls well short of providing definitive steps to adequately address the issue of corrosion protection of underground copper piping installations.
More often than not, proper installation is left up to the installer; and they install the tube the way they have forever, without truly understanding the pitfalls of their actions.
This brief article will attempt to dispel many of the "old wives tales" related to burying copper tube by providing technically correct information on the proper installation of buried copper and copper alloy piping.
The majority of the literature available on the causes of soil-side corrosion of copper tube is based, for the most part, on the corrosiveness of the soil and backfill materials used. Based on studies undertaken by Denison 1 , and others, like James R. Myers and Arthur Cohen the following are conditions that may render soils corrosive to copper 2 :
- Elevated sulfate or chloride contents together with poor drainage, retained moisture, and an annual rainfall exceeding 30 in.;
- Very low resistivity of the soils (below 100 to 500 ohm-cm);
- Large quantities of organic matter, particularly organic acids;
- Moist cinder fills, either because of the sulfides present in the cinders or because of galvanic action between the copper tube and the cinders;
- Anaerobic SRB (sulfate reducing bacteria), which produce sulfides and are aggressive to copper;
- Inorganic acids; and
- Appreciable amounts of ammonia or ammonia compounds, which may be introduced by lawn fertilizers.
Other factors that could promote underground corrosion of copper include:
Oxygen differential concentration cells. Preferential corrosion is sometimes found on the underside of copper tubes because they are in contact with undisturbed soil where the oxygen content is reduced, in contrast to the upper portion of the tube which may be exposed to aerated backfill where oxygen content is high.
Variable aeration characteristics. These depend on particle size and distribution, the degree of compaction, and the drainage characteristics of the soil or backfill material.
Deicing practices. If the chloride content of the soil is elevated because of deicing (thawing salts for roadways and side walks) the metal becomes more anodic than the areas where the chloride content of the backfill material is lower.
Stray currents. Direct current (DC) from impressed cathodic current corrosion protections systems or from the grounding of alternating current (AC) systems to the underground copper service can be detrimental.
Cinders. Although connections of copper tube to ferrous water mains can be very favorable for the copper tube, the copper could still be attacked if it is embedded in backfill materials containing cinders.
Observations and Recommendations
Most installers are aware that the trenches provided for the installation of sewer and water for a building tend to be the repository for all types of construction debris. It is vitally important for installers to ensure that the trenches they provide do not become the dumping location for wood scraps, insulation, and a myriad of different kinds of construction debris. Or to make sure that this debris is cleared prior to tube installation, and final backfill. The decomposition of wood, especially many types of treated wood products, can greatly increase the acidic level of the soil surrounding the tube as those wood (organic materials) decompose.
It is recommended that copper tubing be installed so that it is surrounded by a homogenous backfill. Laying the tube on the bottom of a trench, directly on the undisturbed or virgin soil can allow an oxygen differential cell to develop along the bottom of the tube where it is in contact with the less oxygenated (less aerated) soil, possibly leading to accelerated corrosion in this area. This is easily prevented by laying a layer of loose backfill, either the soil removed from the trench or a selective backfill, on the trench bottom prior to laying the tube. Types of selective backfill materials that may be used (though not limited to these) are: washed sand, limestone sand or small limestone chips, small smooth river stone, or washed pea gravel. Four to six inches of a homogenous backfill material spread evenly along the bottom of the excavated trench prior to installation of the copper tube will provide for an even support of the tube and improve the drainage of groundwater from the trench. Once the tube is installed and tested an additional four inches to a foot of homogenous backfill material should be evenly spread over and around the tube prior to backfilling the trench excavation with the soil that had been removed. Proper compaction of the backfill in the trench is also advised.
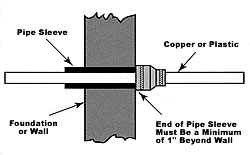
Figure 1. Fernco Clamp
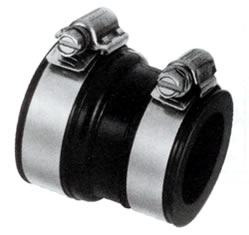
Figure 2. Fernco Elastomeric Clamp
In most applications, copper's corrosion resistance to underground environments provides a lifetime of service in direct burial in the soil. However, in some cases, sleeving may be required or desired. When sleeving is required it is very important that the sleeve be sealed water-tight against the infiltration of ground water. It has been determined that many unsealed, sleeved installations have exacerbated the soil-side corrosion of the copper tube by allowing the thawing salts, fertilizers, or other contaminants in the ground water to collect and concentrate between the copper tube surface and the sleeve.
Sealing of sleeves can be accomplished several ways, although many practices which are thought to be satisfactory are actually very detrimental to the copper tube.
One such practice that should be avoided is the sealing of the space between the tube and sleeve with silicon caulk. Many silicon caulking materials outgas ammonia and/or methanol during their curing process. The outgassing of ammonia, within the sleeve, can lead to stress corrosion cracking of the copper tube, and eventual failure.
Another often employed practice that should be avoided is the sealing of the sleeve with hydraulic cement. Though no adverse reaction with the copper tube will occur, the fact that the tube is held very rigid at the location of the hydraulic cement may contribute to stress fracturing of the tube at that point. Stress fracturing is caused by overworking the tube at that point through motion from thermal expansion/contraction, movement of the backfill material by freezing and thawing, or settling of the soil or structure around the sleeve and tube by improper compaction of the backfill.
Two inexpensive and easily installed ways to properly seal sleeves, water-tight can be accomplished using Fernco TM elastomeric clamps (Figures 1 and 2 above) and electrician's duct seal (Figure 3). Both of these allow the tube to expand and contract and move within the sleeve and still maintain the water-tight seal.
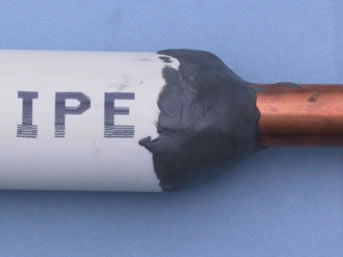
Figure 3. Electrician's Duct Seal
Following these simple guidelines to ensure proper backfilling, and sleeving of buried copper tube systems will help make sure that all of your underground installations remain out-of-sight and out-of-mind for years to come.
References
- I.A. Denison, Trans. Electrochem. Soc. 81, 235 (1942): p. 111.
- J.R. Myers, A. Cohen, JAWWA 76, 8 (1984): p.68.