This document is a edited version of an article which appeared in American Water Works Association Journal, August 1984 and is reprinted, with permission from American Water Works Association.
- Download a PDF version [PDF - 700 Kb]
- Abnormally Aggressive Soils
- Concentration-Cell Corrosion
- Stray Direct Current Corrosion
- Faulty Design and Workmanship
- Alternating Current Action
- Thermogalvanic Effects
- Identifying the Corrosion Problem Without Excavation
- Mitigating the Underground Corrosion of Copper
- Summary
- References
Copper, a noble metal that occurs naturally in its elemental form, is almost totally impervious to corrosion from soils found worldwide. But it would be misleading to infer that copper will not corrode. This article identifies a host of possible situations in which copper pipe or tubing may be subject to external corrosion. These situations are discussed in detail, and suggestions are given on how to identify underground corrosion of copper pipe without excavating and how to mitigate existing corrosion conditions.
The belief by knowledgeable engineers, architects, and water utility personnel that copper is not adversely affected by the majority of soils worldwide is well founded. Uncommonly well-preserved copper artifacts continue to be recovered in Mesopotamia from beneath the clay deposited by the "Great Flood," which is believed to have occurred about 4000 B.C. 1 Many of the underground copper pipes used to convey water in Egypt nearly 5000 years ago are still in existence. Furthermore, copper is one of the few metals that exists as an element in its natural form. There is also the outstanding history of copper tubing as a highly corrosion-resistant material in most underground environments. There are conditions, however, that can cause copper to corrode when it is exposed to certain soils. These include:
- abnormally aggressive soils,
- localized and long-line-type concentration cells created by differences in soil composition,
- the action of stray direct currents (DC) flowing in the ground,
- faulty design and workmanship,
- certain conditions created by alternating currents (AC),
- thermogaivanic effects, and
- galvanic action involving dissimilar materials.
Abnormally Aggressive Soils
Copper is essentially immune to corrosion. It behaves like a noble metal in most underground environments because of the naturally protective film that forms on the metal's surface. If this film, which often consists of reddish-brown cuprous oxide (Cu 20), is destroyed and cannot be repaired, copper will corrode. Fortunately, the protective film on copper remains intact or is readily repaired under most soil conditions.
Three definitive studies on the underground corrosion of copper have been conducted. 2-4 Very likely, this apparent lack of interest in the soil-side corrosion of copper is the result of the metal's known corrosion resistance in underground environments.
Analysis of the results obtained in these three independent investigations clearly establishes that the underground corrosion of copper is unusually complicated. In general, corrosion cannot be directly related to any one or even several factors, as many interrelated soil conditions are involved. The data presented in the three studies and the results of others 5,6 permit some tentative conclusions regarding the corrosion of copper in underground environments. These include:
- Corrosion is often associated with a combination of elevated sulfate or chloride content in the soil in conjunction with poor drainage, a soil having considerable capacity to hold moisture, and a moderate to heavy annual rainfall (usually more than 76 cm [30 in.]).
- Elevated concentrations of sulfate or chloride or both in the soil are probably the primary factor in the underground corrosion process, but considerable moisture is required to support the electrochemical action. The sulfates and chlorides may not adversely affect the copper if the rainfall is slight and drainage is adequate.
- Very low soil resistivity (i.e., less than 100-500 ohm-cm) generally indicates a soil that could be aggressive.
- Soils containing large quantities of organic matter (particularly soils containing organic acids) can be corrosive
- Moist cinder fills are generally corrosive, either because of the sulfides present or because of the galvanic action created by the carbon particles in the cinders
- Construction rubble that contains considerable lime should not be particularly corrosive, provided that localized concentration cells, especially oxygen differential cells, are not created during backfilling
- Soils such as clay, sand, gravel, loam, and chalk seldom possess the combination of properties that are associated with corrosion
- Organic soils supporting active anaerobic bacteria (i.e., sulfate-reducing species) can produce sulfides, which are aggressive to copper
- Soils containing inorganic acids can be unusually aggressive to copper
Soils containing appreciable amounts of ammonia compounds are usually corrosive to copper. The appearance of the copper surface and identification of the corrosion products generally provide insight regarding the cause of deterioration. For example, green copper corrosion products are often basic copper carbonate, basic copper sulfate, or copper oxychlorides. The existence of appreciable amounts of copper oxychlorides in the corrosion products would be expected for a copper water tube that had been buried in a low-resistivity tidal marsh environment. A heavy black layer on the copper would suggest the presence of copper sulfide and the possibility of anaerobic bacteria activity as the cause of corrosion. The presence of ammonia, in combination with sulfate compounds on the copper surface, indicates that the cause of corrosion could be lawn fertilizer.
Corrosion of underground copper can be either uniform or localized (figure below).
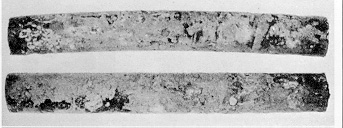
Localized corrosion suggests the existence of local-action cells such as those created by nonhomogeneous backfills. Local-action-cell corrosion is also suspected when the underside of a horizontal copper-water-tube service line suffers preferential corrosion.
Back to TopConcentration-Cell Corrosion
There are at least three types of electrochemical concentration cells that cause corrosion to a metal or alloy because of differences in the environment. These include oxygen, neutral-salt, and hydrogen-ion cells.
Areas on a metal surface in contact with a soil that has an elevated oxygen content will generally be cathodic relative to those areas where less oxygen is present. Oxygen usually functions as a cathodic depolarizer; further, areas of increased oxygen tend to be preferred cathodic sites where the reduction of oxygen can occur:
2H 20 + 0 2 + 4e - 40H -
This is commonly referred to as an oxygen-differential concentration cell. Oxygen-type concentration-cell corrosion is often the explanation for the preferential underside corrosion of a copper water tube. The underside of the tube is often in contact with reduced oxygen-content, undisturbed soil, whereas the upper portion of the tube is exposed to aerated backfill. Corrosion on the underside of the tube is aggravated under this condition by the large ratio of cathode area to anode area that exists. Oxygen-differential concentration cells can also be created by nonhomogeneous backfills. Metals and alloys in contact with lumps of clay will almost always be anodic to nearby metal when the major backfill material is sandy loam. Similarly, long-line corrosion currents can exist if the service line passes through areas of major soil differences.
Corrosion of underground copper can be caused by certain neutral-salt concentration cells. Regions of elevated chloride are generally anodic to regions of reduced chloride. Such choride-type concentration cells are sometimes created by deicing salts, such as in a serviceline trench that can act as a subsurface drainage ditch for several years following its excavation and backfill.
There is also reason to believe that regions on a metal surface in contact with soil having a low ph will be cathodic to areas on the same metal where the localized pH is somewhat higher. The concept of hydrogen-ion concentration cells is supported in part by the observation that the corrosion potential of a metal or alloy generally becomes increasingly positive as the pH of the environment decreases. 7
Back to TopStray Direct Current Corrosion
Stray current corrosion or interference, too often erroneously referred to as "electrolysis," can occur on underground copper water tubes when uncontrolled direct currents exist in the area. This form of corrosion is related to the magnitude and direction of direct currents flowing in the earth through paths other than those intended. When stray currents flow onto the underground structure, no corrosion damage occurs because these areas are cathodically protected. These stray currents also cause no deterioration while they are flowing in and along the structure. However, the currents must eventually leave the structure, return to the earth, and flow to their source of generation. Areas where these currents leave the structure and enter the soil are anodic, and serious corrosion can occur at these locations.
A common source of stray DC electricity is an impressed-current-type cathodic protection system such as those widely used by utilities and gas and oil transmission companies for the mitigation of corrosion on underground steel pipelines. Electric utility high-voltage direct-current (HVDC) transmission systems, DC-powered transit systems, welding facilities, and mining equipment are also potential sources of stray direct current.
Back to TopFaulty Design and Workmanship
In addition to those problems created by abnormally aggressive soils, concentration cells, and stray DC, the corrosion of underground copper can be aggravated by faulty design and workmanship.
Allowances must be made for thermal expansion and contraction when copper water tubes pass through the concrete slab of a building. If this is not done, corrosion fatigue can sometimes occur on the convex surface of the tubes near where they pass through the concrete. 5, 8 Corrosion fatigue is indicated when brittled type, transverse cracks are present in the ductile tube. Although the incidents of corrosion fatigue are rare, they can occur on improperly installed, under-the-slab, domestic hot-water lines, where periodic expansion and contraction take place.
It is also known that improperly prepared or installed flared tube joints on underground service lines, caused by the presence of residual burrs on the seating surface, can result in localized erosion and corrosion. When this occurs, the problem is readily recognized by the U-shaped pits on the affected areas, which are essentially free of residual corrosion products (figure below).
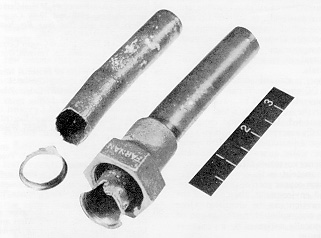
This can be aggravated by abnormally fast water velocities in the distribution system.
Back to TopAlternating Current Action
The role of alternating current on the underground corrosion of copper is not well understood. 9 Some investigators contend that any metal dissolved during the anodic half-cycle should be redeposited during the cathodic half-cycle. Others believe that the efficiency of the anodic half-cycle is greater than that of the cathodic half-cycle and, therefore, that AC-induced corrosion can occur. The argument persists as to whether cuprous oxide on the outer surface of an underground copper water tube can rectify AC, although some of the recent research suggests that this rectification does not occur. 10, 11
Some investigators believe that a critical AC density must be exceeded for AC corrosion to occur. 12, 13 It is also possible that AC facilitates depolarization of the local anodes and cathodes on an underground copper surface. 11 This depolarization would be expected to increase the corrosion-current density and the resultant corrosion rate.
Until these differences of opinion are reconciled and recent research results are corroborated, it is reasonable to believe that the commonly used practice of grounding electrical systems to underground copper water systems can lead to corrosion. If the copper plumbing system is connected to a nonconducting main, such as asbestos-cement, some corrosion damage can be anticipated where the current leaves the copper, even if the current is alternating. Further, cuprous oxide could become semiconducting under certain conditions of soil pH and electrical-field intensity. Grounding of the AC system to the underground copper water tubing and unbalance in the AC system could very well be involved in the underground corrosion process.
Back to TopThermogalvanic Effects
Driving potentials for the corrosion of copper can be created by temperature differences in under-the-slab, hot and cold domestic water lines that are in metallic contact with each other at the hot-water heater. This phenomenon should be suspected when the external corrosion of copper water lines occurs only to the hot-water tubes.
Thermal effects in the immediate vicinity of underground hot-water tubes can sometimes aggravate the corrosion problem by concentrating salts at these locations through the evaporation of water that might be draining through the soil.
Galvanic action. Although copper is normally cathodic to most commonly used underground metals and alloys such as steel, galvanized steels, and cast iron, two forms of galvanic corrosion can occur to underground copper lines. 14 These are the carbon-copper cells associated with certain cinder fills, and the copper-in-soil-copper-in-concrete cell associated with on-slab construction.
Copper is anodic to carbon, and corrosion can be expected to occur if the cinders used for backfill contain appreciable amounts of carbon. Moisture, however, must be present for this galvanic action to take place.
It is also known that copper embedded in concrete will normally be cathodic to nearby copper that is exposed to soil. This subtle form of galvanic corrosion can cause the deterioration of copper exposed to the soil in the immediate vicinity of the soil-concrete interface. Reportedly, this form of corrosion is the reason that complete concrete encasement of copper water tubes is required in some Southern California areas. 5
Back to TopIdentifying the Corrosion Problem Without Excavation
Close-interval surveys of tube-to-soil potential can often be used to predict those areas where active corrosion of underground copper is taking place. 15-17
Based on one investigation, 17 which is supported by another, 18 it is believed that the data in Table 1 can be used to predict the corrosion activity on an underground copper-water-tube system.
Similar potential surveys can be used to identify major areas of stray-current corrosion.
Potential-V Versus Copper-Copper Sulfate | Corrosion Activity |
---|---|
-0.5 or more negative | Copper is well protected; suggests that copper is cathodically protected |
-0.25 or more negative | No corrosion in most soils |
-0.1 or less negative | May be corroding |
0.0 or positive | Probably corroding |
In general, negative potentials will be recorded where the stray current enters the copper tube and the material is cathodically protected. Much less negative and even positive potentials will be obtained where the stray current leaves the underground structure, returns to the earth, and causes corrosion. Stray-current corrosion can also be confirmed with the tube-to-soil potential survey technique. Interruption of the offending current source will often reveal major potential differences between the current-off and current-on readings, especially if the reference cell is located at the site of major anodic activity.
Back to TopMitigating the Underground Corrosion of Copper
The underground corrosion of copper can be effectively mitigated by a number of techniques. These include:
- cathodic protection,
- improved drainage,
- avoidance of nonhomogeneous and cinder backfills,
- judicious use of selective nonaggressive backf ills,
- proper system design and industry standard workmanship, and
- mitigation of any stray-current corrosion.
One of the most cost-effective methods for mitigating the corrosion of copper exposed to a hostile environment is cathodic protection. 17, 19 Corrosion control is achieved when the potentials of the cathodes on the corroding copper surface are polarized to the open-circuit potentials of the local-action anodes. For most copper-water-tube systems, this can be readily accomplished using sacrificial anodes. Zinc anodes in packaged backfills can be used, provided the soil resistivity is less than approximately 2000 ohm-cm. Packaged magnesium anodes should be used if the soil resistivity is greater than about 2000 ohm-cm.
Although the current required to protect underground copper cathodically will vary depending on local soil conditions, copper apparently polarizes quite readily in most soils. The current required to protect a square foot of bare copper can be as low as 0.4-1.7 mA. 20 The belief that relatively small currents are required to protect underground copper cathodically is supported by the observation that this form of electrochemical corrosion control is generally achieved automatically when service lines are in metallic contact with cast iron water mains. General guidelines for the design of a workable cathodic protection system for underground copper are available in the technical literature.
Improvements in the drainage pattern, so that water flows away from the building or service line, can be used to eliminate underground copper corrosion problems. The trench containing the service line must not be directly downstream of any septic drainage systems or building downspouts. Similarly, the trench must not be a collection basin for deicing salts and lawn fertilizer.
For those areas in which it is known that the underground copper will be exposed to abnormally aggressive soils, it is possible to encase the metal completely in a selective backfill. These backfills can be prepared by mixing sand with cement powder, screened soil with chalk, or screened soil with pulverized limestone. A selective backfill, however, may not accomplish its intended objective if the drainage is such that aggressive species can concentrate and come into contact with copper.
Stray-current corrosion of underground copper should be mitigated by the responsible organization. This deleterious form of underground corrosion is readily rendered innocuous through resistance bonds and the proper installation of sacrificial anodes on the adversely affected structure. For severe conditions, when the offending current source is an impressed-current-type cathodic protection system, it is sometimes necessary to relocate the anode bed associated with the cause of the interference.
It cannot be overemphasized that underground copper-water-tube systems must be properly designed and installed. Provisions must be made for thermal expansion where copper hot-water tubing passes through concrete slabs. Improperly installed flared tube joints on copper service lines must be avoided.
Back to TopSummary
Copper water tubing has an outstanding history of corrosion resistance in most underground environments. Copper does not naturally corrode in most clays, chalks, loams, sands, and gravels. Certain aggressive soil conditions, however, can cause it to corrode. The basic prerequisite for corrosion is the presence of appreciable amounts of moisture. Other factors that can facilitate the corrosion process include soils having: (1) elevated concentrations of sulfate, chloride, ammonia compounds, or sulfide; (2) poor aeration, which supports anaerobic bacteria activity; (3) large amounts of organic or inorganic acid; and (4) large oxygen or neutral-salt (especially chloride) differentials.
Copper is also subject to corrosion by stray DC electricity. It can apparently be adversely affected by certain conditions in the AC system to which it might be grounded. Underground copper is reportedly susceptible to thermogalvanic effects and dissimilar material corrosion. Copper water tubes can occasionally experience corrosion fatigue.
Fortunately, in those rare instances in which copper corrodes in the underground environment, the cause of the deterioration can be identified. Once this is accomplished, corrosion can be economically mitigated by a variety of techniques.
Back to TopReferences
- Copper Underground: Its Resistance to Soil Corrosion.
Copper Development Assn. Publ. 40. London (1947). - DENISON, I.A. Electrolytic Behavior of Ferrous and Non-Ferrous Metals in SoilCorrosion Circuits.
Trans. Electrochemical Soc., 81:435 (1942). - GILBERT, P.T. Corrosion of Copper, Lead, and Lead-Alloy Specimens After Burial in a Number of Soils for Periods Up to 10 Years.
Jour. Inst. of Metals, 73:139 (1947). - ROMANOFF, M. Underground Corrosion.
Natl. Bu. of Standards Circular 579. NBS, Washington, D.C. (1957). - WOODSIDE, R.D.; WATERS, F.O.; & CORNET, Corrosion and Other Problems in Copper Tubing in Some Southern California Housing Tracts.
Proc. Third Intl. Congress Metallic Corrosion, Moscow (1966). - KROON D.H. Corrosion Detection of Copper Concentric Neutrals on URD Cable.
Proc. Ann. Appalachian Underground Corrosion Short Course, Morgantown, W.Va. (1979). - MYERS, J.R.; BECK, F.H.; & FONTANA, M.G. Anodic Polarization Behavior of Nickel-Chromium Alloys in Sulfuric Acid Solutions.
Corrosion, 21:277 (1965). - WATERS, D.M. Internal and External Copper Corrosion in Domestic Water Services.
Proc. AWWA Ann. Conf., Anaheim, Calif. (May 1977). - ZASTROW, O.W. Effect of AC on Corrosion of Buried Electric Distribution Cable.
Materials Performance, 20:12:41 (Dec. 1981). - WILLIAMS,J.F. Corrosion of Metals Under the Influence of Alternating Current.
Materials Protection, 5:2:52 (Feb. 1966). - COMPTON, K.G. Corrosion of Concentric Neutrals.
Materials Performance, 16:12 (1974). - KRUGER, S. & BIRD, C.E. Corrosion of Metals by Applied Alternating Currents.
British Corrosion jour., 13:163 (1978). - SERRA, E.T.; DE ARAUJO, M.M.; & MANN. HFIMER, W.A. On the Influence of Alternating Current on the Corrosion of Aluminum and Copper in Contact With Soil.
Proc. Corrosion '79, Atlanta (1979). - DENISON, I.A. & ROMANOFF, M. Soil-Corrosion Studies, 1946 and 1948: Copper Alloys, Lead, and Zinc.
Jour. Res. Natl. Bu. Standards, 44:259 (1950). - KROON, D.H. Underground Copper Corrosion.
Proc. Corrosion '75, Toronto, Ont., Canada (1975). - HUSOCK, B. The Use of Potential Measurements in Analyzing Corrosion of Concentric Neutrals in URD Cables.
Proc. Corrosion '78, Houston (1979). - Manual on Underground Corrosion in Rural Electric Systems.
Rural Electrification Admin. Bull. 161-23. USDA, Washington, D.C. (1977). - KROON, D.H. Corrosion Evaluation and Cathodic Protection of URD Cable.
Proc. Corrosion '76, Houston (1976). - ROGERS, P.C.; GROSS, E.E.; & HUSOCK, B. Cathodic Protection of Underground Heating Lines.
Materials Protection, 1:7 (1962). - ZASTROW, O.W. Galvanic Behavior of Underground Cable Neutral Wires and jacketing Materials.
Materials Performance, 16:11 (1977).