Abstract
It is not always possible to get water into all areas of an injection mold. This is especially pronounced with mold cores. One solution is to apply high thermal conductivity materials, such as copper alloys to non-watered areas. However, it has been difficult to predict the exact outcome of installing non-watered copper components. This study examined modeling and analysis strategies to accurately predict watered and non-watered copper and steel mold cores. Use of these techniques should help mold designers and mold engineers to apply high thermal conductivity materials in a way that will do the most good.
Introduction
Increasing demands for tighter part tolerance and shorter overall cycles, have made mold cooling an ever more significant issue (1). This problem is especially acute in those areas of the mold where putting water lines is difficult or impossible. Applying high thermal conductivity materials into these areas makes a great deal of sense. (2,3) However, the results have not always met the customers' expectations.
Providing an adequate source of heat removal from non-water cooled copper alloy inserts is a key to success. The use of chill plates for second-surface cooling will provide this ultimate heat removal, but design of the system is critical. (4) Thus, correctly applying design and analysis tools becomes an important factor for success in a cooling system using high thermal conductivity copper alloy cores with ultimate heat removal coming through second-surface cooling. This research took an iterative approach to developing strategies to correctly model second-surface cooling behavior with verification using both instrumentation and non-instrumented injection molds.
Methodology
This study was used to verify modeling methods and analysis considerations necessary to determine how different combinations of core and chill plate materials can affect the heat transfer, cycle time and part quality in a tool.
Analysis Tools
The analysis program used in this study was from Moldflow's Dynamic series BEMCL version 9.4.0. This is a modified boundary element algorithm. With this method, up to 10 different tooling materials can be defined by the user to represent the various materials in the mold. As a result, the model of the mold can have various cavity and core inserts. This model can then be investigated to see how different material in these inserts will influence the heat extraction in the part.
Analysis Considerations
During the tool design stage a cooling analysis was used to determine how to best apply the use of mold materials and the placement of water lines to have an efficient tool and produce quality parts. A boundary element cooling analysis can require significant computer resources so there always needs to balance between accuracy and compute time. How the plastic part and mold are modeled will also have a significant influence on the time required to run a cooling analysis. In addition the thermal properties of the mold materials being investigated, the water temperature and flow rate, and the cycle time components are all critical inputs. (5)
Thermal properties needed for a cooling analysis include; conductivity, specific heat, and density. These properties will be different for various grades of mold materials, and can also change depending on how the mold material was manufactured and heat treated. The variation in thermal properties within one grade of mold material, will not be significant enough to cause major changes in mold temperature.
Water temperatures and flow rates on the production floor are often difficult to consistently maintain. In most plants, the flow rate available at each press and the temperature of the coolant (normally water) will continually change, sometimes with wide season to season differences. The best way to take water flow rate and temperature changes into consideration in the cooling analysis is to make the cooling design efficient. When the cooling design is efficient and optimum, changes in flow rate and water temperature will only change magnitude of the temperatures, not the temperature distribution.
To run a cooling analysis, the following components of the cycle time must be input; injection time, packing time, cooling time, and clamp open time. When designing a tool, where cycle time is not known, the injection time can be determined from a flow analysis. The packing time can be estimated based on flow analysis. The cooling time can be determined in the cooling analysis automatically. These all relate to the "unknown". The minimum cycle for any part may not be controlled strictly by cooling the part until it is frozen. The part can often be ejected before it is completely cooled. Finally, the clamp open time can also be estimated.
Modeling Considerations
There are several ways the part and mold models can make a significant difference on the accuracy and analysis speed. The mesh density and aspect ratio are very important.
When modeling a part, consider what type of analysis is going to be done and what information is needed from the analysis. Having a very fine mesh for a cooling analysis will make the analysis take a very long time to calculate to a stable solution and require a very large amount of disk space and ram. Over one Gigabyte of disk space and several hundred megabytes of ram is possible for models that have over 10,000 elements. The number of elements that is used in the part model may need to be high to account for some flow issues like hesitation or weld line location. For this reason, the part can be meshed at a high density for the flow analysis optimization, then re-meshed for the cooling with a lower density. If this is done, a second flow analysis must be done so the flow analysis can be used as heat load input into the cooling. Also, the course mesh must still have a good aspect ratio. The aspect ratio should stay below 6:1 as a maximum. Meshing at a lower number of divisions with a maximum aspect ratio can result in a model that has fewer elements but will provide an excellent cooling model for the heat load is modeled.
If insects are going to be modeled as part of the mold model, the surface boundaries on the part model must touch the insert. This is best achieved by having the part surface follow the same line. This will not normally be a problem, but should be considered. See Figure 1.
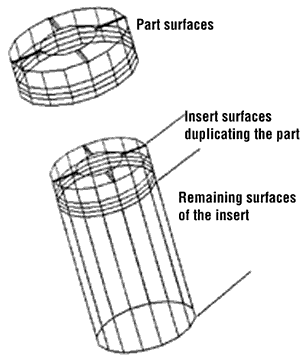
When modeling the mold, careful consideration should be given to adding detail. The minimum detail that must be in a mold model are the waterlines. Since different mold materials are used in the tools being evaluated, inserts must be modeled. The mold boundary and parting planes can also be modeled.
An insert can represent two things, a mold material other than the mold base and a thermal interface between the insert and the mold plate within which it is located. An insert is modeled by a group of surfaces that make a closed volume. Where the insert touches the plastic part, the surfaces that create the part and insert must be perfectly coincident. This can be accomplished by changing the attributes of points and surfaces on the plastic part that touches the insert to define an insert. Additional surfaces then need to be created to form a closed volume. Attributes were assigned for the thermal properties of the mold material and the interface conductance. By assigning interface conductance as resistance to heat transfer could be modeled. This interface could occur due to clearances for assembly purposes, and various fits used in the mold.
A parting plane is used to model the thermal interface by assigning an interface conductance. This could be used at a parting line, or the interface between the core plate and the core support plate as an example.
Finally the mold outer boundary can be modeled. If this is not explicitly modeled, the XYZ size of the mold must be entered for the calculations of the boundary element method. Having a mold boundary modeled is not mandatory but is a good visual aid for the model.
Care in meshing the mold model is the best way to minimize the number of elements in the model. When waterlines pass through an insert, the insert must have a node at the intersection of the waterline. The aspect ratio of elements around these intersection points is critical. If the aspect ratio is high, it can cause a convergence problem that may affect the entire model and not just the local area. In Figure 2, the baffle is passing through the insert. The mesh aspect ratio on the insert surface was high enough to cause convergence problems. The aspect ratio is under 7:1. The way to fix the problem is to mesh just that one surface at a higher density.
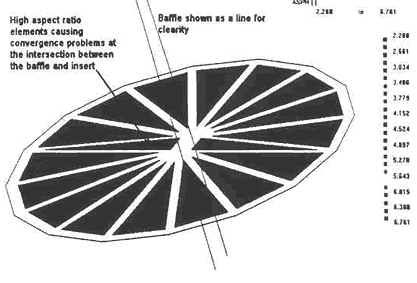
Experimental Molds
The single cavity injection mold used in this study produced a 33 mm dia bottle cap. The cap is molded with Huntsman polypropylene co-polymer. The tool is shown in Figure 3.
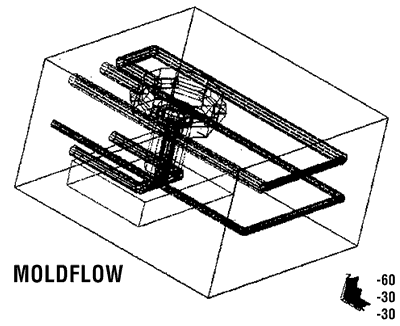
The mold was constructed with inserts for the cavity and core so different mold materials can be used. A chill plate is also used to evaluate the cooling cores with no water directly in the core. In this study, the cavity insert was always 420 SS. The core material was 420 SS or C17510 BeCu. Core temperature measurement for this tool was done with a temperature thermocouple imbedded in a hole approximately 3 mm from the top and edge of the core. The thermocouple was modeled using a parting plane that represented the top of the hole and part of the side walls. See Figure 4.
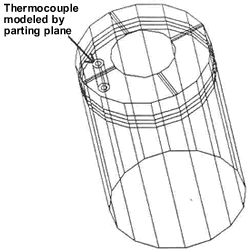
Results
When using cooling analysis to optimize the design of the tool, the trend of the temperature results is much more important than the actual number. The cooling conditions that are used in an analysis will never match what is happening on a production floor because conditions are constantly changing. However, the trends will be consistent. The cap too shown in Figure 3 used four different combinations of core materials, chill plate materials and watered vs. Non-watered cores. Results obtained from actual production runs were compared with the cooling analysis. Two analyses had no baffle within the core, and two did have a baffle. Table 1 is a summary of the results. The temperature measured with the thermocouple is the range of temperatures over the production runs for the combinations.
Combination No. | 1. | 2. | 3. | 4. |
---|---|---|---|---|
Core Material | 420 SS | C17510 BeCu | C17510 BeCu | 420 SS |
Chill Plate Material/ Baffle in Core |
P20 Baffle in Core |
C18000 No baffle in Core |
P20 Baffle in Core |
P20 No baffle in Core |
Core Temperature measured with Thermocouple | 48.1 to 51.8 deg. C 118.5 to 125.2 deg. F |
36.9 to 39.3 deg. C 98.4 to 102.8 deg. F |
20.3 to 23.2 deg. C 68.5 to 73.8 deg. F. |
77.8 to 80.4 deg. C 172.0 to 176.7 deg. F |
Core temperature from cooling analysis | 41.3 to 42.9 deg. C 106.3 to 109.2 deg. F |
25.0 to 25.4 deg. C 77.0 to 77.7 deg. F |
20.9 to 21.2 deg. C 69.9 to 70.2 deg. F |
57.3 to 59.0 deg. C 135.1 to 138.2 deg. F |
Temperature Variation between thermocouple and analysis | 6.8 to 8.9 deg. C 12.2 to 16.0 deg F |
11.9 to 13.9 deg. C 21.4 to 25.1 |
-0.6 to 2.90 deg. C -1.1 to 3.6 deg. F |
20.5 to 21.4 deg. C 36.9 to 38.5 deg. F |
The core temperature from the analysis is the cycle averaged temperature in the mold model at the parting plane that represents the location of the thermocouple. The results on the thermocouple are also shown in Figure 5.
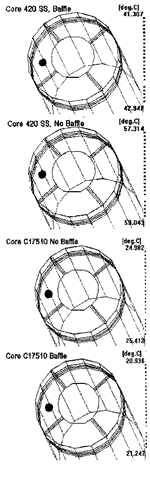
Looking at the temperature variation row of the Table 1, two trends emerge. First, the tend of the temperature ranges are very good, comparing one combination to another. Combination 3 should have the lowest temperature because the core material is C17510 and has a baffle in the core. Combination 2 is next because it is the same core material, but no baffle. The hottest core is combination 4 which is 420 SS with no water. The distribution is logical. The predicted temperature at the thermocouple location in the cooling analysis is from the range of the thermocouple to as much as 21.4 deg. C. low. The trend here is the higher the temperature variation in the core, the higher the error. The reason is a combination of a lower thermal conductivity for the core material and larger distance between the plastic part and water line. When there is an error in the thermal properties as input to the cooling analysis, the longer distance the heat travels in the mold material and the lower the material conductivity the more the error has an effect on the analysis. Even with a rather high error in combination 4, the trend of the temperature distributions is excellent. This is what is important when optimizing the design of the cooling system of a mold.
Conclusions
This study shows that the analysis tools available today will do an excellent job in assisting the tooling designer/engineer to properly apply high thermal conductivity alloys in tools.
Acknowledgements
The authors extend their thanks to the Copper Development Association Inc. for providing necessary support for this research. Performance Alloys & Services Inc. constructed all necessary mold components. Ampco Metals, Materion Corporation, Copper and Brass Sales, and NGK Berylco provided alloys for the mold. Research assistance was also provided by Robert Dealey, Cliff Moberg, Dr. Dale Peters and Scott Smyers.
The research was completed with the work of the following students: Tom Bayer, Ole Hansen, Kurt Hayden, Jerome Hund, Pat Jeakle, Eric Peterson, Tim Perkins, Frank Rinderspacher, Dennis Rosten, and Ryan Wejrowski.
References
Engelmann, P., Dawkins, E., Shoemaker, J., Monfore, M. (1996). Predicting the Performance of copper alloy mold cores. Plastic Engineering, vol. 52 (10), pp. 35-37.
Engelmann, P., Dawkins, E., Shoemaker, J., Monfore, M. (1997). Improved product quality and cycle times using copper alloy mold cores. Journal of Injection Molding Technology, vol. 1 (1), pp. 18-24.
Engelmann, P., Dawkins, E., Monofore, M. (1997). Copper vs. Steel cores: Process performance, temperature profiles and warpage. Technical Papers, vol. 43, pp. 972-976, Brookfield, Ct: Society of Plastics Engineers.
Engelman P., Dawkins, E., Dealey, R., Monfore, R., (1998). Getting Heat Out Of The Mold Where Water Won't Go. Technical Papers, vol 44, Brookfield, CT Society of Plastics Engineers.
Engelmann, P., Dawkins, E., Shoemaker, J., Monfore, M. (1996). Applying copper alloys using new mold cooling software. Technical Papers, vol. 42, pp. 1000-1005. Brookfield, Ct: Society of Plastics Engneers.