Abstract
The process of regrinding thermoplastic resin is associated with a series of handling, feeding, contamination, and melting problems. Some have suggested that removal of fines from reinforced resin can have an adverse effect on certain material characteristics and processing conditions. A dedicated system employing special grinding techniques, aspiration of fines, and static abatement was used to study the impact of fines removal through a number of generations of process history. The system once optimized allowed a detailed study of the relative viscosity, glass content, and tensile properties of the material conditions. The results provide a foundation for molders seeking to incorporate thermoplastic regrind into current production settings.
Background and Introduction
Both environmental and economic concerns have led many in the plastics industry to conclude that the goal of in-plant recycling is that of zero waste. In other words, every pound of resin that comes into the plant should leave the shipping department as finished product. It is clear that although the goal is not likely to be realized, it helps to keep the industry focused on the direction by which progress is marked. Problems associated with regrind have been well documented over the years.
The work detailed here is an outgrowth of long term research at Western Michigan University. As part of the investigation into wear mechanisms associated with injection molds, it became necessary to run over a million shots of glass-filled nylon 6. Both from an economic and ecological standpoint, it was unthinkable to do this project with virgin resin. This was viewed as an opportunity to apply the findings of both theoretical and applied work with regard to producing ultimate quality regrind.
One goal of this work included reusing the glass-filled nylon 6 resin as many times as possible without negatively affecting the wear research. In other words, all reasonable efforts were made to ensure that the viscosity, shear, and glass content (by weight) did not change during the study. The second goal of the research was to institute a cascade regrind system to document resin performance. The third goal was to minimize or eliminate handling and conveyance problems with the regrind. This included consideration of all portions of the regrind reclamation system. The fourth goal was to reduce or eliminate losses of resin in the system so that the final generation of regrind had as close to the original net volume of resin as possible. The fifth goal was to reduce the number of contaminates found in the regrind. The final goal was to reduce the amount of time personnel spent handling the resin to zero.
Both the system for resin reclamation and the level of resin analysis evolved over the course of the wear study. System optimization was viewed as critical to meet the goals of the project. The most important factor in determining how many generations of regrind could be run without becoming a nuisance variable to the research revolved around the definition of what aspect of the molding process caused tooling wear. It was determined that the following key factors needed to be monitored.
- The temperature and shear rate of the resin flowing through the tool needed to be held constant through the various generations of virgin and regrind.
- It was decided that a change in glass content greater than the manufacturer's tested specifications would constitute an unacceptable alteration of the experiment.
- It was concluded that a substantial change in fiber length might have an impact on wear. These factors taken together establish the decision criteria by which resin quality was measured.
Statement of Theory and Definitions
Regrinding glass filled nylon creates obvious handling and processing problems (i.e. static, dust, and water absorption). Two separate material forms, fines and heavies characterize the regrind. Fines defined by Webster's Dictionary are very small particles in a mixture of various sizes (1). The term heavies in this experiment refers to particles, having great mass in proportion to the maximum dimension. Through an extensive rotap study it was determined that fines are particles above a thirty sieve (openings of 590 microns) and heavies are anything below. However, this method defines the two material conditions mostly by shape and dimensions. The mesh sieve simply restrains large irregular particles, while allowing particles with smaller dimensions to pass through.
In this experiment, aspiration was used to separate fines from heavies. Aspiration forces a continuous air stream against free-falling regrind. The fines are then separated and carried away, as shown in Figure 1. This method defines fines and heavies based upon the particle's relationship between mass and maximum dimension, assuming density remains constant. Aspiration provides an environmentally friendly method of reducing nuisance impurities in thermoplastic regrind. Past research has determined the air velocity setting to be a key variable in the percentage of fines separated (2). It was concluded in this experiment that roughly eight percent (by weight) of the regrind was being aspirated as fines.
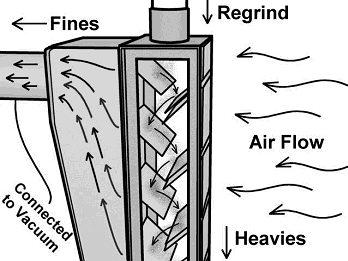
Description of Equipment
The operation of the current regrind reclamation system is shown in Figure 2. The system begins with parts being fed into an auger granulator via a conveyor belt. The aspirator operates simultaneously to the granulator and deposits the fines into 35-gallon drum and the heavies into a gaylord. A Herbert static controller de-ionizes the regrind while, magnets located under the exiting heavies relieve the chance for contamination. Virgin resin and the heavies would then be transported, mixed, and dried. Finally, the mixture would be reintroduce to the injection-molding machine. The fines can be extruded and pelletized for later use.
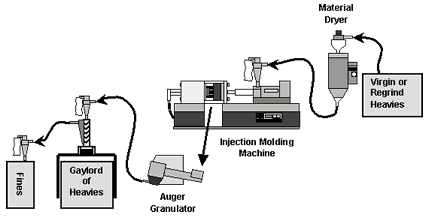
The regrinding operation in this experiment was conducted on a three-rotating blade Conair-Jetro granulator. An aspirator built in 1998 by Western Michigan University was attached and operated simultaneously to the granulator. The fines were extruded and pelletized with a 32 mm (1¼ diameter) Killion extruder. The extruder screw had an L:D ratio of 24:1. Extrusion was necessary to prevent handling and loading problems of the fines. The material used was 33% glass-filled nylon 6 supplied by Allied Signal. The nylon was dried with a Una-Dyne dryer. Moisture contents were analyzed with a Computrac MAX2000 moisture analyzer.
The parts for the grinding and aspiration were formed by an eight-cavity wear mold. They were 1.5 mm (.06) thick round chips with a diameter of 19 mm (.75). The parts had a 5 mm (.20) high wall running around their diameter. The delivery system consisted of a DME straight-shot hot sprue bushing, two P-20 runner bars, and one edge gate per part.
Molding and on-machine rheologies were conducted on a 77 metric ton (85-ton) hydraulic toggle injection molding machine. The injection screw was 35 mm (1 3/8 diameter) with a 20.6 cc (5 ounce) shot. A data acquisition system was attached to the injection molding machine. Cavity pressure, screw position, and hydraulic pressure were monitored by an RJG Technologies DART system. Readings were processed by DARTWin software (Release 3.0). An AEC mold temperature controller regulated mold water. Resin loading was done with an AUTOLOAD hopper loader.
Tensile specimens were molded from a standard ASTM testing mold. Tensile testing was conducted on a Tinius Olsen universal low-capacity testing machine. Specimen dimensions were measured with a digital Mitutoyo caliper. Burn tests were conducted in an Omegalux furnace. Crucible and sample weights were recorded from an OHAUS microbalance.
Experimental Design
Independent variables for the experiment included generation which was measured by heat history (processing cycles), grinding/aspirating history, and material form, (including the treatments, virgin resin and the subsequent fines and heavies of regrind). All other process and molding factors were held constant. Virgin resin used in the experiment was recycled and reused through several heat and grinding/aspirating histories. Response or dependent, variables for the experiment included relative viscosity, tensile characteristics, and percent glass content (by weight). Since it was not possible to have generation one fines for viscosity and tensile tests, the combinations of heat history and material condition were not fully cross-classified.
Standard on-machine rheology experiments to measure relative viscosity were run on two separate days. Two replicates of virgin material were tested, one at the beginning and one at the end of each day. This replication was employed to monitor any potential block effects, such as experimental drift. The various material conditions were run in random order. After each run, Dupont Zytel with purging compound (PA 6/6) was purged to reduce contamination between samples. As part of the viscosity evaluation, injection speed was set at half second intervals from 5.0 to 0.5 seconds and quarter second thereafter, for a total of eleven different time intervals.
A gate seal experiment and process optimization was performed to set up the tensile bar molding process. Following a stabilization period, 12 tensile bars were collected per material condition. The specimens were then conditioned in a testing lab under
ASTM D613 environmental guidelines for a minimum of 48 hours.
For the tensile measurements, six specimens were randomly selected from each experimental run and tested in accordance with ASTM D638. Included were four replicates of virgin material tested periodically to track and monitor experimental error.
The following tensile properties were analyzed, yield and break.
Glass content was established using a standard ash test procedure. The ash tests were conducted in a furnace at 482 ° C (900 ° F) for one hour. Five random samples from each experimental run were tested. Samples weighed approximately 0.6 grams (.02 ounce) and were measured to the nearest 0.001 gram. Samples were burned in random order and placement. The remains were allowed to stabilize in accordance with ASTM D613 before reweighing and recording the final weights.
Throughout the experiment, particular care was taken to monitor and maintain consistent process and molding conditions. Prior to all molding cycles, the test resin (nylon) was dried to a moisture content of 0.30% or lower. All key molding issues were held constant, such as gate dimensions and melt temperature. Introducing pelletized fines not only reduced handling issues; it lessened the variation between material forms in terms of plasticating. In regard to aspiration and grinding, the air velocity setting and granulator blade condition were kept constant.
Analysis of Data
The data were analyzed using the software package STATISTICA for Windows (3). The data were analyzed using a combination of standard analysis of variance methods and graphical methods. For all graphical analyses, a distance weighted least squares line was fit to each treatment of data to facilitate interpretation. All tests for statistical significance between treatment effects were performed at a 95% confidence interval. Mean separation tests were performed using the Scheffe method at a 95% confidence level.
Findings
The viscosity curves shown in Figure 3 were similar for all treatments. This suggests the independent variables had little practical effect on viscosity. Any variations were most likely due to noise. Please note generation corresponds to heat history.
Results for tensile data are presented in Figure 4. The data suggest there was a significant reduction in tensile strength of the nylon resin between the virgin generation and all subsequent generations. Additionally, a significant difference was observed between the regrind treatments of heavies and fines (p<.05). The 100% heavies and heavies/fines mixture were similar for tensile performance (p>.05). However, the 100% fines group exhibited lower tensile performance than either of these groups (p<.05). Tensile differences within post-virgin generations did not appear to be significant (p>.05).
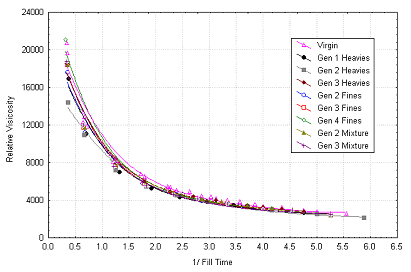
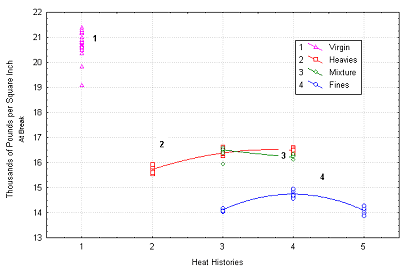
Results for the ash test are shown in Figure 5. The data indicated a significant difference in the glass content among the various generations (p<.05). The pattern of these differences was unexpected, but was most likely the result of sampling error. Relative to the manufacturer's tested specifications of 33% (+/- 2%), the range between all treatment means was just over 2%, well within the manufacturers tested specifications. While the data indicated the treatment averages were statistically different, no practical difference was judged to exist. These findings suggested that no important changes in glass content were influenced by the independent variables of generation or material form.
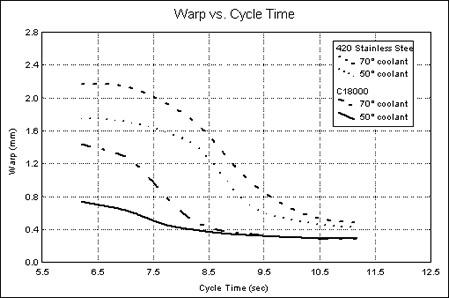
Conclusions
In this experiment, there was no appreciable change in relative viscosity between the various material conditions. This is not to say other key processing variables such as cooling rate or plastic temperature will not be impacted by successive heat and/or grinding/aspirating histories.
The breakdown in tensile properties was not a result of a change in glass content of the various material conditions. Recent observations in glass fiber length suggest a correlation to the tested tensile characteristics. Preliminary data show a decrease in glass fiber length after being molded the first time. The cause is under study.
These data clearly disprove any theories that grinding and aspiration decreases the glass content in regrind. Instead, aspiration produces a quality regrind that eliminates the problems associated with static, dust, and water absorption.
The research detailed in this experiment has allowed Western Michigan University to take advantage of implementing a reclamation process approaching complete automation and zero net loss of material. This process may be tailored to meet the needs of many molders seeking to recycle or improve the quality of regrind. This study provides a basis for tackling other thermoplastic materials with similar characteristics. However, other dependant material variables and cost justification will need to be examined.
References
- Mish, F. (Ed.). (1991). Webster's Ninth New Collegiate Dictionary . Springfield, MA: Merriam-Webster Inc.
- Gami, R., Schott N., Groth, B., Gerlitz, F. (1998). Value-added impact of fines separation from free-falling dry thermoplastic regrind. Technical Papers , vol. 44, pp. 2946-2951. Brookfield, CT: SPE.
- StatSoft, Inc. (1998). STATISTICA for Windows [Release 5.1.] Tulsa, OK.
Acknowledgements
The research team at Western Michigan University wishes to acknowledge the significant support of a number of organizations and individuals; the Copper Development Association Inc., Johnson Controls, Inc., and Kalamazoo Sheet Metal. Allied Signal provided the resin for the entire study.
Research assistance was also provided by the WMU Material Engineering Department. The following students put in many hours on this project: Eric Osborne, Frank Asher, Allen Woodruff, Alicia Habercorn, Joe Piesco, Wataru Tsutsui, Troy Winningham, Michael Buckle, Alex Lorenz, Paul Arkinstall, Johan Maertens, Leonid Fedorovitch, Eric Kuusisto and Marty Lemon.
