Abstract
Hot days with high dew points, and their high relative humidity, invariably lead to a host of molding problems. The molder is faced with either substantially altering the process or coping with the effects of sweating molds and equipment. A steel core in an injection mold was replaced using a copper alloy. Process conditions for the mold were established to accommodate operating conditions with a high dew point. Controlled testing was performed under adverse weather conditions. Results of these tests prove the efficacy of correctly applied copper alloy components for the reduction or elimination of problems caused by condensation on molding components.
Background and Introduction
Molding operations during hot weather are complicated by a series of problems. This is especially acute during operations where the dew point is also high. These conditions create problems in three areas. Hygroscopic resins tend to pick up significant moisture requiring additional drying, personnel fatigue tends to increase, and sweating of molds and mold cooling equipment becomes an acute problem. Research conducted at Western Michigan University, focused on the latter of these three problems associated with a high dew point.
Sweating of molds and equipment has several negative effects. It poses a safety hazard, it causes corrosion damage to the molds and equipment, and it causes attribute defects on the molded products themselves. In many cases, it is necessary to keep mold water extremely cold in order to achieve even modest temperatures on the mold surface. A 28°C difference (this is equal to a 50°F difference) between the water temperature and mold surface temperature is not uncommon.
With cycle time at a premium, molders are reluctant to arbitrarily raise mold coolant temperatures by modest amounts to eliminate sweating. This situation is compounded by the fact that most molders today, ship product on a just-in-time (JIT) basis, running molds across the calendar year. If the mold temperature was increased by 11°C (20°F) during summer operations, a molder would have to alter the process used for a given mold. Not only could there be a penalty of longer cycle times during high temperature operation, but some products might need to be re-certified based upon the altered process. In any event, knowledgeable customers of the end product view radical changes in the molding process across the calendar year in a negative light.
Because of these factors, the effectiveness of strategically applying high strength, high thermal conductivity copper alloys to critical mold surfaces was investigated. This study tested the hypothesis that by substituting copper for less thermally conductive steels, the temperature of mold water could be raised, eliminating sweating problems. Simultaneously, the overall cycle could be either maintained or in fact decreased when compared to a steel tool.
Many thermoplastics require a mold surface temperature of 24°C (75°F) or higher. Since the dew point is seldom above this temperature, it was suspected that mold water temperature would never need to be below the dew point if water temperature closely matched the mold surface temperature.
Description of Equipment
Mold
For the experiment, a single cavity 33-mm bottle cap mold was used ( Figure 1). The mold design allowed for easy interchangeability of the core. During experimentation, both C18000 copper alloy and type 420 stainless steel cores were installed in the tool.
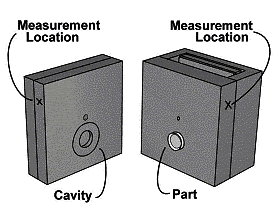
The cavity and core plates were also cooled using ¼ NPT water lines. The core was cooled with the use of a 13mm (½) spiral baffle and ¼ NPT water lines. Depending upon the phase of the experimentation, water temperature was set to 10°C (50°F) and 21°C (70°F) to establish mold temperatures above and below the dew point, respectively.
Runner and gate sizing analyses were run using Moldflow's MF/FLOW analysis. The resin used was a Huntsman polypropylene co-polymer. The resin entered the cavity through a .89mm (.035 inch) orifice sub-gate, making the parts self-degating. Ejection was accomplished with an air-assisted ring ejector.
Previous research had investigated the ability of Moldflow's MF/COOL analysis to predict temperature relationships of interior mold surfaces (1, 2, 3). Because dewpoint interacts with all surfaces of a mold, exterior surface temperatures were also critical. A cooling analysis was used to predict the coolant temperature required to establish an exterior mold temperature higher than the anticipated dewpoint.
Additional Equipment
Experimentation was performed with a 77 metric ton (85-ton) VanDorn hydraulic toggle injection molding machine with an Autoload hopper loader for resin handling. The injection screw was a 35mm (1?" diameter) with a 20.6 cc (5 ounce) shot. An AEC mold temperature controller and a 2.7 metric ton (3-ton) Thermal Care chiller were used to regulate water temperature. Water was monitored on all circuits for flow rate, input and output temperatures, and pressure lost through the circuit.
Temperature was monitored in the cores, the gate area and the cavity with Strawberry Tree's Quicklog PC data acquisition and control software. Thermocouples were embedded in heat transfer compound to eliminate air gaps and provide a more accurate temperature reading.
Experimental Design
Procedure
Previous research at Western Michigan University had established that the three high strength, high conductivity copper tooling alloys, C17200, C17510 and C18000, performed similarly under normally watered conditions (1, 2, 5). Therefore, it was established that C18000 could be used to model the general performance of a copper tooling alloy. However, it must be noted the actual performance of a specific copper alloy will be dependent upon the specific design of the mold in which it is applied. The focus of this experiment was to compare the cure time performance of copper cores versus steel cores under at two cooling temperatures conditions.
The experiment included three independent variables; core material, cooling temperature and cure time. Two core material treatments (steel or copper), two cooling temperatures (above and below the dew point), and seven cure time treatments were used. Dependent, or response, variables included part weight and warpage, a dimensional characteristic. A four run factorial arrangement of core material and cooling temperature factors, plus one replicate, formed the five run base of the experimental design. The replicate was used to measure any experimental error that might have occurred during the course of the experiment. The five base combinations were run with various cure times. Cure time was initially set at 5 seconds and reduced in increments to zero. Initial cycle time was 11.2 seconds. A full replicate of the base study was also conducted, resulting in a total of ten runs. This replicate of the base study also included various cure time treatments. Some, but not all, of these cure time treatments were replicates of the first portion of the study. The specific sequence of cure times was used to gain additional resolution in the highly nonlinear responses.
With the exception of cure time, the molding process was not changed for the duration of the experiment. A period of process stabilization was allowed after each cure time adjustment and at the beginning of each run. Part weight was measured at press-side and was used to determine process stabilization by part weight trend. Changes in the independent variables typically destabilized part weight. The process was declared stable and sample collection begun when the process was observed to have returned to normal variance conditions.
Measurement
The parts were allowed to stabilize in accordance with ASTM environment guidelines for a minimum of 72 hours. Part warpage was defined as the amount of deflection across the surface of the bottle cap. Deflection was determined by subtracting the edge height of the cap from the center height of the cap. A gauge was used to measure the height of the cap in two locations. These measurements were taken with a digital plunger indicator. Gage repeatability and reproducibility (R & R) study was performed using ANOVA methods for validation.
An Omega pyrometer (model HH21) was used to measure exterior tool temperatures at a fixed location on the exterior of both the cavity and core plates of the mold. After allowing the process to stabilize at a given cure time, multiple samples were taken in rhythm with the molding cycle and the average value was calculated and recorded. These measurements were used to ensure that the exterior temperatures on the mold were above the dew point. During these measurement periods, the mold was also inspected for the presence of condensation.
Embedded thermocouples were used to measure tool temperatures in the core, cavity, and gate areas. These thermocouples were located approximately 3 mm from the molding surfaces. This placement was intended to allow for the detection of any temperature changes during the molding cycle. The data acquisition software was used to sample these temperatures in 10 millisecond intervals.
Measurements were entered into the software package Statistica (version 5.1J) for statistical analysis (4). Data was grouped by independent variables and graphed to resolve the relationship of cycle time and cure time using distance weighted least squares trend lines.
Findings
Visual observation of the mold, flow meter and cooling hoses during all portions of the experiment showed that the 21°C (70°F) coolant temperature was sufficient to raise the temperature of the mold surface above the dewpoint. Dewpoints during the experiment reached a maximum of 22°C (72°F).
The accuracy of the predicted exterior mold temperatures (calculated during the cooling analysis) was verified using the temperature measurements taken during the experiment. Graph 1 compares the measurements to the predicted values for both the "A" and "B" halves of the tool. From this graph, it was observed that the results of the Moldflow MF/COOL cooling analysis were within 10°C (equivalent to within 18°F) of the actual values observed.
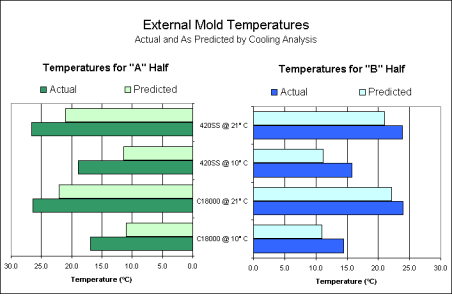
The temperatures of the cavity and gate area were plotted for each combination of material and coolant temperature using the information from the data acquisition system. As in previous studies, the temperatures of the gate and cavity were dependent upon the coolant temperature, but not upon the core material (5, 6, 7). This can be observed in Graph 2. In other words, regardless the core material, the temperatures on the "A" half of the tool remained constant for a given coolant temperature. However, the temperatures of the steel cores were significantly higher than the copper cores at similar coolant temperatures.
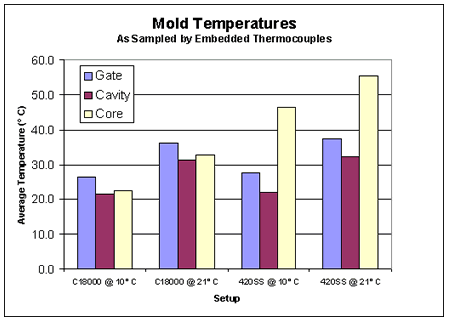
From the measurements taken, the relationship between warpage and cure time was established. This relationship is represented in Graph 3. When the copper core was used with 10°C (50°F) coolant, a stable low-warpage condition was maintained at cycle times as low as 8.5 seconds. When the coolant temperature was increased to 21°C (70°F), the part only required a cycle of 9 seconds to maintain the same low warpage as that of the 10°C coolant.
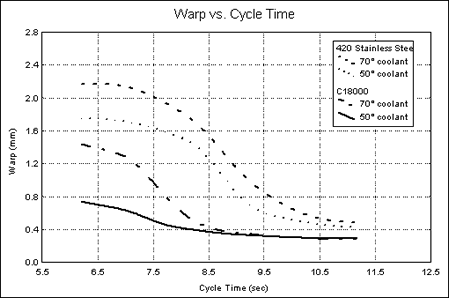
Cycle times of 10 seconds and longer were required to obtain minimum warpage with the steel core with 10°C (50°F) coolant. At cycles less than 10 seconds, warpage increased until maximum warpage was reached with an approximately 7-second cycle. With 21°C (70°F) coolant used with the steel core, minimum warpage occurred at cycle times in excess of 10.5 seconds.
Conclusions
During this experiment, a coolant temperature above the dewpoint prevented condensation from forming on the tool and cooling equipment. In industry, this lack of condensation provides a safer environment for personnel, and reduces the possibility of moisture becoming trapped within the mold itself. Thus, the possibility of damage to molding surfaces due to corrosion is reduced.
A Moldflow cooling analysis accurately predicted the relationship between the core material, the coolant temperature and the temperature of external mold surfaces. This type of analysis can be used to aid in the development of a process that can run year-round without causing condensation during periods of high dewpoints. Specifically, the cooling analysis can be used to predict the lowest coolant temperature necessary maintain a mold temperature above the highest anticipated dewpoint.
A slight increase of 11°C (equivalent to an increase of 20°F) in coolant temperature was required to raise the tool temperature above the dewpoint. The relatively high thermal conductivity of the copper core allowed this increase in coolant temperature without a dramatic increase in warpage. With the C18000 core, an increase in cycle time of only one half second was required to maintain the same level of warpage at both coolant temperatures.
With cooling temperatures less than the dewpoint, the steel core still ran hotter than the C18000 core cooled with water temperatures above the dewpoint. The warpage of parts molded with the steel core stabilized at cycle times two seconds longer than the copper cores. The steel cores were never able to reach the same low warpage levels as those of the copper cores. In addition, the steel cores experienced a more drastic change in the magnitude of warpage as cure time was reduced.
With minor adjustments of coolant temperature and cure time, seasonal condensation issues can be eliminated. It is understood that when coolant temperature is increased a longer cure time will be required to maintain the same level of warpage. This necessary increase in cure time is minimized when copper alloys are used to form core-like structures in the tool. Since copper alloys can provide lower warpage levels at faster cycle times than steel, copper can be used in place of steel to allow a single process to be run year-round without decreasing productivity or creating condensation.
References
- Engelmann, P., Dawkins, E., Shoemaker, J., Monfore, M. (1996). Applying copper alloys using new mold cooling software. Technical Papers , vol. 42, pp. 1000-1005. Brookfield, CT: SPE.
- Engelmann, P., Dawkins, E., Shoemaker, J., Monfore, M. (1996). Predicting the performance of copper alloy mold cores. Plastics Engineering , vol. 52 (10), pp. 35-37.
- Shoemaker, J., Engelmann, P., Dawkins, E. & Kietzmann, C. (1998). Cooling prediction of non-watered copper and steel cores. Technical Papers , vol. 44, pp. , Brookfield, CT: SPE.
- StatSoft, Inc. (1998). STATISTICA for Windows [Release 5.1 J]. Tulsa, OK
- Engelmann, P., Dawkins, E., Dealey R., Monfore, M. (1998). Getting Heat Out of the Mold Where Water Won't Go. Technical Papers , vol. 44, pp. 836-840. Brookfield, CT: SPE.
- Engelmann, P., Dawkins, E., Shoemaker, J., Monfore, M. (1997). Improved product quality and cycle times using copper alloy mold cores . Journal of Injection Molding Technology , vol. 1 (1), pp. 18-24.
- Engelmann, P., Dawkins, E., Monfore, M. (1997). Copper vs. Steel cores: Process performance, temperature profiles and warpage. Technical Papers , vol. 43, pp. 972-976, Brookfield, CT: SPE.
Acknowledgements
The research team at Western Michigan University wishes to acknowledge the significant support of a number of organizations and individuals.
The Copper Development Association Inc. provided financial support for this research.
Performance Alloys & Services Inc. constructed all necessary mold components.
Huntsman Chemical donated the polypropylene for the study.
Special research assistance and project guidance was provided by Scott Smyers of BrushWellman Inc.
Research assistance was also provided by Dr. Dale Peters, and Matthew Hagerty.
The following students also assisted in the research: Eric Dawkins, Guliha Dheeraj, Marie Dudek, Keith Wilkenson and Allen Woodruff.
