Download PDF [317 Kb]
General
Copper and copper alloys are widely used because they combine unique properties at an economical price. These include high thermal and electrical conductivity, ease of manufacture, high recyclability and good corrosion resistance. Copper, a noble metal that occurs naturally in its elemental form, is almost totally impervious to corrosion from soils found worldwide. But it would be misleading to infer that copper will not corrode.
Corrosion
Galvanic corrosion is an electrochemical process whereby one metal corrodes preferentially to another whenever both metals are put in electrical contact and immersed in an electrolyte. What is surprising to some is that soil or air can be an electrolyte.
Underground
Copper is the preferred metal for grounding conductors and electrodes. This is not only due to its high degree of connectivity, but also its corrosion resistance. In most soils, copper electrodes outlast alternates such as galvanized steel. However, there are certain conditions where tinning (coating with tin) the copper would be useful.
The designer of a grounding system typically performs a soils analysis before designing the grounding system. Soil aggressiveness and chemical composition will determine the appropriate steps to take.
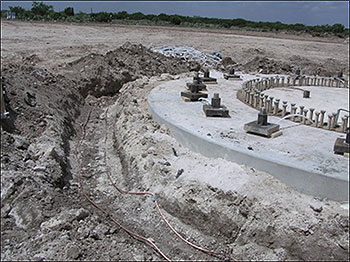
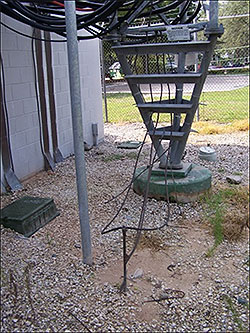
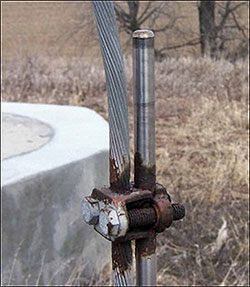
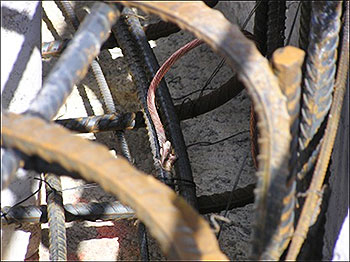
When the chemical composition of the soil is unknown (in the absence of soil testing), it is the user’s choice to stipulate tinning or bare. In most cases, bare copper is sufficient, although we recommend exceeding the rather minimal gauge requirements of the NEC. 4/0 AWG or larger is commonly found in industrial environments.
When soils are highly acidic, or alkaline, or suspected of being so, backfill material such as bentonite can greatly extend the life of bare copper. Further, bentonite retains water, thus can greatly increase contact area with the soil, thus reducing grounding resistance. Carbon-based backfills often contain other contaminants, such as sulfur and other elements which are harmful to copper and should be avoided.
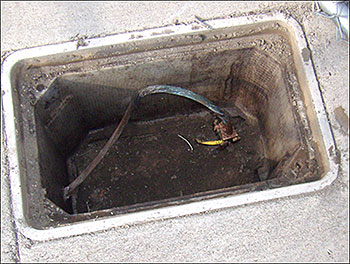

Above-ground Outdoor Construction
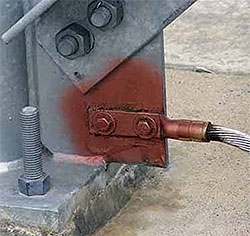
Figure 7. Tinned 4/0 copper conductor attached to a galvanized steel flange of a support column. Note the high pressure compression fitting and protective paint.
Outdoor air can act as an electrolyte because it contains a variety of components which can cause corrosion of any metal. Varying moisture levels, salt and other contaminants are just a few. In overhead, outdoor construction, copper runoff can cause staining of pavement materials. It’s one reason why older overhead telephone wiring (before plastic coverings) was usually tinned. In addition, copper runoff can be very corrosive to galvanized steel support structures, even when not in direct contact. In such cases, tinning of the conductors is recommended to prevent such conditions.
“Precipitation run-off from copper and copper alloys can attack galvanized parts (BS 6651:1999 and IEC 61024-1-2, section 5.2); therefore, bare copper conductors or copper bus bars shall not be installed above galvanized steel, such as a tower, unless the steel is protected against the precipitation run-off “ (IEC 61024-1-2, section 5.2, quoted in Motorola R56.)
Lastly, for connection to the main grounding bus, or any connection point, consider connectability. In a recent research project conducted by Powertech Labs, copper connections in mechanical connectors passed thermal cycling tests under IEC 61238-1, while the overwhelming majority of aluminum connections largely did not pass, irrespective of preparation. See Building Wire for more information on this study.
Further Reading
The general information in this document is a limited look at the complex subject of corrosion, and further investigation is encouraged. The following sources contain additional information on grounding and corrosion.
- IEEE Standard 142, “Green Book”, latest edition
- Copper Applications in Power Quality