High Strength Copper Steel for Rail Tank Cars to Bridges
Copper Applications in Metallurgy of Copper and Copper Alloys
Abstract | Introduction | Results | Summary | Bridge Application | Authors | References
Abstract
Development of higher strength-higher toughness steels for tank car applications has been a target for many years to improve the overall performance of railroad tank cars. Over the past ten years, three grades of low carbon copper-precipitation-hardened steels have been developed (NUCu-60, NUCu-70 and NUCu-100) in collaborative research between Northwestern University and Ispat-Inland Inc. The two lower-strength grades are produced by air-cooling after hot rolling. The NUCu-60 Grade (Supertough Cryogenic Steel) has yield stress of 415 MPa (60 ksi) and remarkable toughness at cryogenic temperatures; more than 350 J (264 ft-lbs) down to –79°C (–110°F). The NUCu-70 Grade has at least 485 MPa (70 ksi) yield strength. Composition of NUCu-100 Grade is the same as that of NUCu-70. The higher strength is achieved by quenching from the austenitizing temperature and aging. The mechanical properties as well as the corrosion resistance and welding properties of these steels are discussed. Finally, an update is provided on a recently built bridge using this alloy in Illinois.
Introduction 
At the present time most of the tank-car shells are fabricated from 50 ksi-yield strength TC128B carbon-manganese steel that contains more than 0.25% carbon and 1% manganese. This steel has a relatively high carbon equivalent weldability parameter. In addition the steel has marginal fracture toughness characteristics at low temperatures. A new more easily weldable, higher strength and higher fracture toughness steel is sought for tank-car application. A series of high strength steels (as described below) that satisfies these requirements was developed at Northwestern University. These are excellent candidates for substitution of TC128B steel in tank car shell applications. These steels have much lower carbon content. The strengthening is derived from copper precipitation on air-cooling from hot rolling. Ni is added to prevent hot-shortness during hot rolling. Nb and Ti are added to control grain size during hot rolling and welding. Since the NUCu steels are primarily ferritic, they don’t contain alloying to increase the hardenability. The initial investigations were done with laboratory heats. Seven 45.4-kg laboratory heats of the steel were melted at Ispat-Inland R&D Department by vacuum melting to work out the composition and processing conditions. Three more 135-kg laboratory heats were melted at US Steel Company Research Center. To evaluate commercial steel production, two 80,000-kg heats were produced at Oregon Steel Mills. One of the heats was used for rehabilitation of a bridge in Illinois. Slabs cast at Oregon Steel Mills were also successfully hot rolled at US Steel Corporation Gary Works. While some of the research results presented here were separately published previously1, 2, 3, 4, 5, this paper ties them together with previously unpublished results.
Higher steel strength makes possible the use of thinner sections to save weight. Significantly improved weldability over high carbon steels should simplify and decrease the cost of fabrication. The 60 and 70 ksi versions of the steel are used in the hot rolled condition thereby saving the cost of normalizing. High copper content gives significantly greater corrosion resistance, unpainted or painted, than usual weathering steels thus minimizing tank car maintenance costs. The NUCu steels appear to be a cost-effective alternative to the present steels used for tank car construction.
Results 
Mechanical Properties
NUCu-60, as shown in Table I, contains higher Ti which ties up the interstitials. The NUCu-60 steel heat was vacuum melted and hot-rolled into 0.5-inch-thick plates at Ispat Inland. The NUCu-70 and NUCu-100-grade steels were cast at Oregon Steel Mills and hot rolled at US Steel Company Gary Works. The composition is also given in Table I. While 70-80-ksi-yield stress was achieved in hot-rolled and air-cooled steel plates up to 2-inch thick, water quenching and aging were needed to reach 100-ksi-yield stress. This paper describes the properties of NUCu-70 and NUCu-100 steels that were cast at Oregon Steel Mills and then hot-rolled into 0.75 and 1-inch-thick plates at US Steel Company. The NUCu-70 steel was tested in (a) as-rolled and (b) as-rolled and normalized at 900°C. The NUCu-100 steel was austenitized at 900°C, water-quenched and then aged at 525°C for 1 hr.
Round tensile specimens with a gauge section of 50.8 mm (2 inches) (ASTM E 8 Standard ) and Charpy specimens (ASTM E 23 Standard) were machined in longitudinal direction from the quarter thickness of the plates and tested. Multiple specimens were tested with very little variation observed. The mechanical properties of the steels are listed in Table II. Table III shows Charpy absorbed impact energy of steels.
C | Mn | Si | Cu | Ni | Ti | Nb | |
NUCu-60 (Ispat-Inland) | 0.03 | 0.53 | 0.52 | 1.29 | 0.52 | 0.10 | 0.06 |
NUCu-70 and NUCu-100 (OSM/USS) | 0.06 | 0.78 | 0.38 | 1.35 | 0.84 | 0.03 | 0.38 |
Yield Stress MPa (ksi) | UTS MPa (ksi) | Elongation (%) | |
---|---|---|---|
NUCu-60 hot rolled | 413(60) | 551(80) | 27 |
NUCu-70-hot-rolled | 503 (73) | 567 (82) | 32 |
NUCu-70-hot-rolled-normalized | 461 (67) | 546 (79) | 36 |
NUCu-100 | 712 (103) | 780 (113) | 26 |
NUCu-60 Hot-Rolled (Ref) | NUCu-70 (Hot-Rolled) | NUCu-70 (Hot-Rolled, Normalized) | NUCu-100 | |
---|---|---|---|---|
24 (+75) | > 360 (>264) | |||
0 ( +32) | > 360 (>264) | 206 (151) | 257 (188) | 132 (97) |
-12 (+10) | > 360 (>264) | 202 (148) | 255 (187) | 115 (84) |
-23 (-10) | > 360 (>264) | 192 (141) | 242 (177) | 89 (65) |
-40 (-40) | > 360 (>264) | 161 (118) | 233 (171) | 64 (47) |
-62 (-80) | > 360 (>264) | |||
-79 (-110) | > 360 (>264) |
Impact fracture testing of NUCu-60 steel shows its remarkable dynamic fracture toughness; Charpy samples did not fracture down to -79°C (-110°F), they bent over in the Charpy apparatus as the hammer swung through.
The NUCu-70 steel samples tested in as hot-rolled condition had yield stress of 503 MPa (73 ksi) and UTS of 567 MPa (82 ksi). The elongation to failure is relatively high, 32% The Charpy absorbed fracture energy fracture is also high, 161 J (118 ft-lbs) at -40°C, this is much higher than required for construction or tank-car application. Normalizing this steel at 900°C increases the Charpy energy, however reduces the yield to 461MPa (67 ksi) and UTS to 546 MPa (79 ksi). NUCu-70 steel more than qualifies for use in tank-car construction in hot-rolled and air-cooled condition since the strength and Charpy absorbed impact energy significantly exceed requirements for such application.
When NUCu steel of the 70 ksi yield strength grade was quenched from 900°C and aged for 1 hr. at 525°C the yield stress was increased to 712 MPa (103 ksi) and the UTS to 780 MPa (113 ksi) with 26% elongation to failure. The Charpy absorbed fracture energy is lower than that for NUCu-70 steel, 64 J (47 ft-lb) at -40°C, an acceptable value for high-strength steel at this low temperature
Welding
Due to the very low carbon level and the absence of elements used to increase the hardenability such as chromium and molybdenum NUCu steels have very low welding carbon equivalents. Figure 1 shows the Graville Diagram predicting weldability. Here the carbon concentration is plotted versus carbon equivalent calculated as CE = C+(Mn+Si)/6 + (Ni+Cu)/15 + (Cr+Mo+V)/5. The Graville Diagram is divided into three zones. In Zone I welds produced under most welding conditions are not susceptible to cracking, in Zone II welding requires pre-heating and post-heating to prevent cracking and in Zone III the heat-affected-zone (HAZ) is extremely susceptible to cracking. As evident from Figure 1, NUCu steel having low carbon concentration and carbon equivalent is deep in Zone I and thus does not require pre-heat and post-heat for welding, TC128B tank-car steel with its higher carbon concentration and higher carbon equivalent falls into Zone II close to the border with Zone III indicating difficulties in welding and susceptibility of HAZ to cracking.
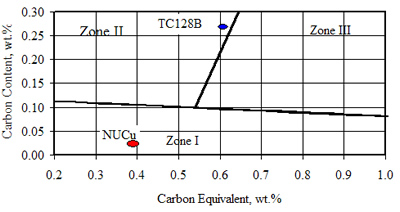
Previously welding of several different heats of NUCu-70 steel was evaluated without pre-heat or post-heat by a submerged arc (SAW) process and also by a manual process in a construction shop environment (Trinity Bridge and Arlington Construction Companies). Matching consumables were used. No brittle heat-affected zone was formed. Steel also was welded in a welding laboratory at Northwestern University without pre-heat or post-heat using LINCOLWELD LA100 wire and LINCOLNWELD 880M flux in SAW process. Two values of heat-input were used, 1.4 KJ/mm (35 kJ/in) and 3.9 KJ/mm (98 kJ/in). Table IV shows that the Charpy absorbed impact energies for welded specimens including the heat affected zone are remarkable high for “low” heat input and exceed the standard requirements for high heat input.
Heat Input kJ/mm (kJ/in) | Charpy Absorbed Impact Energy (J (ft-lbs)) at Testing Temperature, °C (°F): | |||
---|---|---|---|---|
24 (75) | -12 (10) | -23 (-10) | -40 (-40) | |
1.4 (35) | 241 (176) | 242 (177) | 224 (164) | 187 (137) |
3.9 (98) | 206 (151) | 70 (51) | 79 (58) | 52 (38) |
Duplicate G-BOP tests conducted at the U.S. Steel Research and Technology Center using a heat input of 1.4 KJ/mm (35 KJ/inch) and low hydrogen AWS E7018 and E9018 electrodes without pre-heat or post-heat did not show weld metal cracks in the welds or base plates.
Stupp Bridge Company, Bowling Green, Kentucky, recently performed a Procedure Qualification (PQR) SAW Test without pre-heat and post-heat using Lincoln LA85 electrodes and MIL800-HPNi flux. The heat input was 2.36 KJ/mm (60 KJ/inch). In fracture tests at -30°C(-22°F) the average Charpy absorbed impact energy was 124 J (91 ft-lb). The requirement by the American Welding Society Standard is 34 J (25 ft-lb) at this temperature.
Corrosion Resistance
Copper significantly improves the corrosion resistance of steel in marine and inland environments6, 7, and the high copper content in NUCu steel is effective in substantially reducing the weight loss in accelerated weathering tests.
Figure 2 compares the weight loss of NUCu steel to that for A36 steel and some weathering steels in SAE J2334 standard accelerated tests performed at Bethlehem Steel Corporation by Townsend7. The thickness loss of A36 steel was133% greater than that of NUCu steel. The thickness losses of A588 weathering steels and HPS70W A709 steel were 69% larger than that of NUCu steel. Using existing databases corrosion indexes have been established and the index for NUCu steel is far lower than that for any other structural steel6, 7, 8.
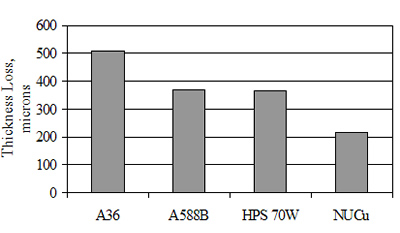
(Data from accelerated automotive SAE J2334 standard accelerated tests performed at Bethlehem Steel Corporation by Townsend7)
The same steel grades were coated with epoxy-based Carboguard 890 paint (Carboline Company), scratched and then tested in a salt-fog chamber (D1654-92 Standard9, 49.97 g/liter salt solution). The extent of corrosion was measured after exposure at 35°C for 3 weeks. Results of the tests are shown in the Figure 3. The widths of the corroded regions adjacent to the scratches were measured and are shown in Figure 4. Again NUCu steel demonstrates the best corrosion resistance; the corroded surfaces at the scratches of A36, A588 and HPS 70W A709 steels were 93%, 52% and 54% respectively wider than that of NUCu steel.
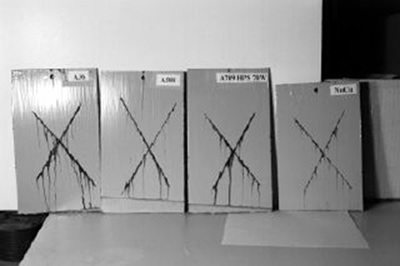
(from left to right: A36; A588; ASTM HPS 70W; NUCu steel)
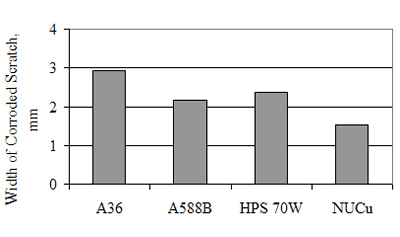
Summary 
The information presented in this paper shows that NUCu 70 in particular has advantages over TC128B steel presently used by the tank-car manufacturing industry. The higher strength should result in weight saving. The higher impact fracture toughness mitigates against brittle failure particularly at low temperatures. While the Cu and Ni alloying required increases steel cost, normalizing is not required; NU-Cu steel is used in the as hot rolled condition. The much better weldability as indicated by position on the Graville Diagram should significantly reduce fabrication costs. Pre-heat or post-heat may be eliminated. The better weathering and corrosion resistance is also a plus. If outstanding impact fracture resistance at very low temperatures is a factor, Supertough NUCu 60 is a candidate. For still higher strength applications NUCu 100 may be the alloy of choice.
Bridge Application 
The Illinois Department of Transportation (IDOT) recently announced the completion of a new bridge in Lake Villa, Lake County (Illinois), constructed with a groundbreaking type of high-performance steel developed by engineering researchers at Northwestern University.
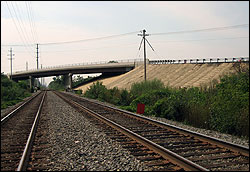
About 500 tons of the copper alloy steel, known as ASTM A 710 Grade B high-performance structural steel, was used in constructing the 430-foot span that carries the Illinois Rt. 83 over the Canadian National Railroad tracks. “IDOT is excited about the possibilities presented by this new type of cost-efficient, high-performance steel developed right here in Illinois,” said IDOT Secretary Timothy W. Martin. “Not only is this steel strong, tough and easy to fabricate, but it withstands the elements better than typical steel, meaning it doesn't have to be painted. This makes construction easier and will significantly reduce long-term maintenance costs.”
IDOT is in the process of applying to the American Society for Testing and Materials (ASTM) and the American Association of State Highway and Transportation Officials (AASHTO) to have this steel designated as standard for bridge construction. The only previous use was in the rehabilitation of the Poplar St. Bridge over the Mississippi River in the Metro East area.
The steel has a strength of 70,000 pounds per square inch (psi) compared with 50,000 psi in commonly used structural steel. It is also easy to weld, and tests have shown it has high-impact toughness at low temperatures. In addition, the high copper content gives the alloy much better resistance to atmospheric corrosion than other high-performance steels.
“We developed this steel nine years ago and application has been a long time in coming,” said Morris E. Fine, professor emeritus of materials science and engineering at Northwestern University, who developed the new alloy with his colleague Research Professor Semyon Vaynman and with key support from Northwestern's Infrastructure Technology Institute (ITI). “This steel is cost-effective because its processing is cheaper than competing structural steels of the same strength, its weathering resistance is best, and it's easier to weld.”
“We are delighted to see our steel used in this new bridge and hope that the steel will be used in other bridges in Illinois as well as in other states,” said Vaynman, research professor of materials science and engineering at Northwestern.
“For more than a half-century, Professor Fine has been one of the seminal leaders in materials science engineering worldwide,” said David Schulz, director of ITI. “The Infrastructure Technology Institute is pleased and proud to have supported his team's development of the high-strength steel employed in the Route 83 bridge. We look forward to continuing to help him 'push the envelope' of ever-stronger and more economical steels.”
The Lake Villa bridge was constructed by Dunnet Bay Co. with a contract value of $5.75 million. The bridge designer was Graef Schloemer and Associates of Chicago. The steel was produced by Mittal Steel USA in Coatesville (Pennsylvania), and fabricated at Industrial Steel Construction in Gary (Indiana). IDOT received federal funds to pay for the steel through the Federal Innovative Bridge Research Fund.
The project was supervised for IDOT by Resident Engineer Mario Biondolillo. Also playing a key role for IDOT on the project was Chris Hahin, the principal investigator and metallurgical engineer for the department. IDOT estimates not having to paint the steel saved $300,000. The new bridge replaced a structure dating from 1929. Construction was carried out in stages in order to keep traffic flowing on Rt. 83.
Authors 
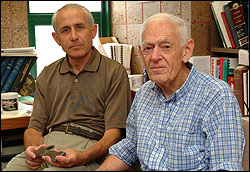
Prof. S. Vaynman and Prof. M. E. Fine: Department of Materials Science and Engineering, Northwestern University, 2220 Campus Drive, Evanston, IL 60208-3108.
S. P. Bhat: Ispat-Inland, Ispat Inland R&D Department, 3001 East Columbus Drive, East Chicago, IN 46312.
1. M. E. Fine et al., International Symposium on Low Carbon Steels for 90's (Cincinnati, OH, ASM International, 1993), 511.
2. S. Vaynman et al., Materials for the New Millennium, Proceedings of the Fourth Materials Engineering Conference (New York, NY, ASCE, 1996), 1551.
3. S. Vaynman, I. Uslander, and M. E. Fine, Proceedings of 39th Mechanical Working and Steel Processing Conference (Indianapolis, IN, ISS, 1997), 1183.
4. S. Vaynman, M. E. Fine, International Symposium on Steel for Fabricated Structures, (Cincinnati, OH, ASM International, 1999), p. 59.
5. S. Vaynman et al., Microalloyed Steels 2002 (Chicago, IL, ASM International, 2002), 43.
6. S. Vaynman et al., “Estimation of Atmospheric Corrosion of High Strength, Low-Alloy Steels”, Metall. Trans., 28A(1997), 1274-1276.
7. H. Townsend, retired from Bethlehem Steel Company, private communications.
8. ASTM G 101-01 Standard for Estimating the Atmospheric Corrosion Resistance of Low-Alloy Steels.
9. ASTM D 1654-92 Standard Test Method for Evaluation of Painted or Coated Specimens.
Also in this Issue:
- High Strength Copper Steel for Rail Tank Cars to Bridges