Aluminum Bronzes - Part I
Metallurgy of Copper & Copper Alloys
- Introduction
- Applications
- Aluminum Bronzes
- Effect of Alloying Elements
- Mechanical Properties
- Corrosion Resistance
- Freedom from Oxide Flaking
- Cavitation Erosion
Download this article in Acrobat PDF Format [536 KB]
Introduction
The aluminum bronzes are a family of copper-based alloys offering a combination of mechanical and chemical properties unmatched by any other alloy series. This feature often makes aluminum bronzes the first choice—and sometimes the only logical choice—for demanding applications. What are these attributes?
- Excellent strength, similar to that of low alloy steels
- Excellent corrosion resistance, especially in seawater and similar environments, where the alloys often outperform many stainless steels
- Favorable high temperature properties, for short or long term usage
- Good resistance to fatigue, ensuring a long service life
- Good resistance to creep, making the alloys useful at elevated temperatures
- Oxidation resistance, for exposure at elevated temperatures and in oxidizing environments
- Ease of casting and fabrication, when compared to many materials used for similar purposes
- High hardness and wear resistance, providing excellent bearing properties in arduous applications
- Ductility, which, like that for all copper alloys, is not diminished at low temperatures;
- Good weldability, making fabrication economical
- Readily machined, when compared with other high-duty alloys
- Low magnetic susceptibility, useful for many special applications, and
- Ready availability, in cast or wrought forms.
Applications
The aluminum bronzes comprise a wide range of compositions, and alloys can be chosen with a correspondingly wide range of properties to suit many types of duty. In fact, the mix of properties available is so varied that alloy selection needs to be carefully considered, and expert advice is always useful.
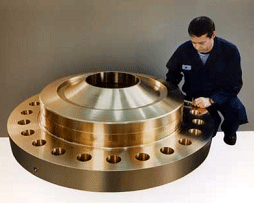
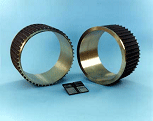
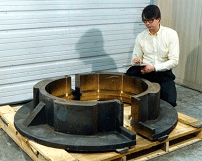
Where are all these properties best employed?
Simply put, aluminum bronzes are used where other materials might fail prematurely or would be more expensive to buy or fabricate. For example, the alloys find widespread applications in chemical, petrochemical and desalination plants; in marine, offshore and shipboard hardware and equipment (Photos 1-4); in power generation (Photo 5), aircraft, automotive and railway engineering; and in the iron and steel-making, electrical manufacturing and building industries (Photo 6).
These areas of application are best discussed with reference to the primary service property required of the alloy, allowing for the fact that it is normally a combination of several properties that finally governs the selection of a particular material. As to the choice of product form, it is worth noting that the excellent mechanical properties obtainable from both cast and wrought aluminum bronzes makes it possible in many applications to interchange the manufacturing method in order to achieve maximum economy.
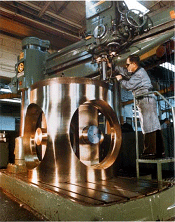
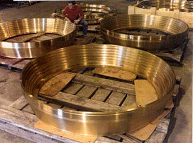
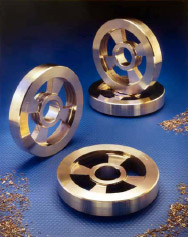
Aluminum Bronzes are Finding an Increasing Number of Applications
Table 1 Contains a list of typical products, both cast and wrought, manufactured from aluminum bronzes. It is by no means an exhaustive list as new applications are constantly being developed. Note that many applications are related to marine environments because of the outstanding performance of aluminum bronzes in seawater.
WROUGHT PRODUCTS | |
---|---|
Drop forgings | Chain |
Tubesheets | Impellers |
Tubes & Shells | Compressor blades |
Pressure vessels | Shafting |
Reaction & Distillation vessels | Gears |
Pipe work | Non-sparking tools |
Wear plates | Non-magnetic equipment |
Springs | Masonry fixings |
Bearings | Rod, bar & shapes |
Fasteners | Free hammer forgings |
Valve spindles | |
FOUNDRY PRODUCTS | |
Impellers | Bearings |
Propellers | Gear selector forks |
Shafts | Synchronizing rings |
Pumps & valves | Non-sparking tools |
Water cooled compressors | Glass moulds |
Tubesheets & other heat exchanger parts | Pipe fittings |
Channel covers | Rudders & Propeller brackets |
Gears & Gear blanks | Die-cast components |
Deep drawing dies | Continuous cast bar & shapes |
Pickling equipment | Centrifugal castings |
Rolling Mill equipment | |
Bushes |
In addition, aluminum bronzes are extensively used as metal-sprayed or weld-deposited surfacing materials, generally over steel substrates, in order to provide wear, corrosion and sparking resistance.
Back to TopEffect of Alloying Elements
In addition to aluminum, which ranges from 5% to 14% in these alloys, the alloying elements most commonly used in aluminum bronzes are nickel, iron, manganese, silicon and tin. The mechanical properties of aluminum bronze depend primarily on aluminum content; however, varying proportions of these secondary additions result in sub-classifications of the family, as described below.
The four principal types of aluminum bronzes are:
- The low alloy, single-phase (face-centered cubic) alpha alloys containing less than 8% aluminum. These alloys have a good ductility, both hot and cold, and are well suited for cold working into tube, sheet, strip and wire. Alloys of this type containing 3% iron are single-phase at compositions exceeding 9% aluminum.
- The more highly alloyed, two-phase (duplex) alloys containing from 8% to 11% aluminum and, usually, additions of iron and nickel, for higher strength. As aluminum content is increased to between 8% and 10%, the alloys are progressively strengthened by appearance of the harder body-centered cubic beta phase, which additionally makes the bronzes more suitable for hot working and casting. Even greater strength and hardness is developed in alloys containing more than 10% Al. Such alloys are favored for specialized applications requiring superior wear resistance.
The other alloying elements mentioned earlier also modify the structure and thereby increase strength and corrosion resistance: iron improves tensile strength and acts as a grain refiner; nickel improves yield (proof) stress and corrosion resistance and has a beneficial stabilizing effect on the metallurgical structure; manganese also performs a stabilizing function.
- The copper-aluminum-silicon alloys, or silicon-aluminum bronzes. These are mainly alpha-phase alloys and therefore have good strength and ductility: Alloys having silicon contents ranging up to about 2% and aluminum to about 6% are known as aluminum-silicon bronzes; these alloys are stronger than unmodified single-phase aluminum bronzes and can be cast and hot-worked more readily. Like other aluminum bronzes, they have a low magnetic permeability and excellent resistance to shock loading. Silicon also improves machinability. The alloys are available in wrought and cast forms.
- The copper-manganese-aluminum alloys, or manganese-aluminum bronzes. These alloys have good castability and were, in fact, developed primarily for the manufacture of propellers. Manganese, at about 13%, is the major alloying addition in a series of manganese-aluminum bronzes in which aluminum levels range between 8 and 9%. Although not so strong as other aluminum bronzes, the alloys' foundry properties are better. They also have good resistance to impingement and cavitation and can be heat treated to give low magnetic permeability. They have excellent weldability.
Mechanical Properties
Tensile Strength
Some aluminum bronzes exhibit strengths comparable to low alloy steels and many are stronger than most stainless steels. Furthermore, the alloys retain a substantial proportion of their strength at elevated temperature, and at low temperatures, they gain strength slightly while retaining ductility. Shear strength can be estimated as being two thirds of the tensile strength.
Yield (Proof) Strength
Yield (proof) strength is a more useful property than tensile strength since it is a measure of the stress needed to cause a measurable permanent (non-elastic) deformation, i.e., far lower than the stress needed to cause failure. However, yield strength is not quite so easy to measure as is tensile strength in this case because, unlike steels, copper alloys do not show a sudden "yield" deformation when stress is increased past a critical value, so "proof strength" is a more appropriate term. Values may be given with respect to various percentages of permanent deformation; in the U.S.A., for example, yield stress for most copper alloys is expressed as the stress corresponding to 0.5% extension under load, whereas for certain high-strength alloys such as C63020, it is given as the stress corresponding to a 0.2% strain offset to the linear (Hooke's Law) portion of the engineering stress-strain curve. Comparison of values therefore needs care.
Hardness
The hardness of aluminum bronzes increases with aluminum (and other alloy) content as well as with stresses caused through cold working. Some manganese- and manganese-nickel-aluminum bronzes exhibit martensitic transformations similar to those seen in steels, but while these reactions produce higher mechanical properties, they are not generally thought of as primary strengthening mechanisms.
Ductility
Most aluminum bronzes show ample ductility to provide adequate service life and to resist fatigue. Again, values attainable vary with alloy content and amount of prior cold work. Elongation figures decrease as the alloys get harder, the ranges shown in the table below reflect this.
Product Form | Tensile strength | Yield Strength, 0.5% Extension | Elongation | Hardness, HRB | ||
---|---|---|---|---|---|---|
ksi | MPa | Ksi | MPa | % | ||
Plate | 50-65 | 350-450 | 17-27 | 117-165 | 30 | 85 |
Sheet | 50-120 | 360-830 | 17-27 | 117-700 | 25-8 | 60-100 |
Strip | 50-145 | 360-1000 | 17-135* | 117-930* | 45-1 | 60-72** |
Bar | 75-100 | 520-690 | 35-50 | 240-350 | 92-80 | 85 |
Rod | 60-120 | 410-810 | 30-75 | 240-520 | 64-1 | 29-98 |
Wire | 60-140 | 410-960 | 67-1 | |||
Tube | 60 | 410 | 27 | 180 | 55 | 77 (HRF) |
Forgings | 80 | 540 | 40 | 260 | 30 | 78 |
*(0.2% offset) **(HR30T) Note: These are generalizations based on most common uses. A comprehensive list of properties for UNS-listed alloys can be found in the Properties section. |
Approx. alloy composition*: Alloy Type | Tensile Strength | 0.5% Yield Strength | Elongation | Hardness (Brinnell) | ||
---|---|---|---|---|---|---|
kips | N/mm2 | kips | N/mm2 | % | HB | |
9% Al, 3%Fe Aluminum Bronze |
80 | 550 | 27 | 190 | 35 | 125 |
10%Al, 5%Ni, 4%Fe, 1%Mn Nickel-Aluminum Bronze | 95 | 660 | 40 | 260 | 25 | 160 |
11%Al, 4%Ni, 4%Fe, Nickel Aluminum Bronze, heat treated | 120 | 830 | 70 | 470 | 10 | 230 |
18%Mn, 8%Al, 3%Fe, 2%Ni Manganese Bronze | 90 | 600 | 40 | 270 | 15 | 220 |
13%Al, 4%Fe (bearing material) | 250 | |||||
*Balance Cu. Note: These values are approximate for sand-cast specimens, and properties vary with composition, section thickness, casting conditions and other variables. Centrifugal castings will produce similar properties. Values for continuous castings will be higher and those for castings made in permanent molds (die castings) will be higher still. Mechanical and physical properties of UNS alloys can be found in the Properties section. |
Wear Resistance
From the standpoint of wear resistance, aluminum bronzes often provide excellent service in both cast and wrought forms. Metal-sprayed or welded overlay deposits of aluminum bronze on steel also provide effective wear-resistant surfaces. At the high end of the wear- and abrasion-resistance spectrum are special aluminum bronze alloys containing up to 14% aluminum, whose applications include dies for deep drawing and molds for die casting, casting of glass bottles and pressing of vinyl records. Such alloys are quite brittle and are exclusively used as overlays.
Bearing and Frictional Properties
Aluminum bronzes are used as bearing materials and heavy-duty guides where other materials would fail quickly. They thrive on heavy loads, shocks and harsh working environments and so are found in steel works, in agricultural, mining and earthmoving equipment, and as bridge bearings and other structural and architectural applications. In rotating applications, best results are usually achieved when running aluminum bronzes against hardened surfaces. When lubrication of sliding surfaces is less than ideal, aluminum bronzes are superior to ferrous materials. Both wrought and cast alloys are used. Permanent mold (also known as gravity or low-pressure die casting) provides an excellent production method for the quantity production of such low-friction items as selector forks for gearboxes. Additional information about bronze sleeve bearings can be found in the Industrial section.
Shock Resistance
Aluminum bronze alloys, and in particular the wrought products, have excellent resistance to shock provided, as always, that the material is sound, and undue stress concentrations are avoided in design.
Fatigue Strength
Aluminum bronzes possess exceptional resistance to fatigue, which is one of the most common causes of deterioration in marine engineering equipment. This property helps to give the alloys their excellent resistance to corrosion fatigue that makes them suitable for use as propellers and in pumps.
Damping Capacity
Aluminum Bronzes are twice as effective as steel in their ability to dampen vibrations.
Magnetic Permeability
Aluminum bronzes can be made with exceptionally low magnetic permeability and are therefore ideal for non-magnetic instrumentation, survey vessels, mine counter-measure craft and other marine parts where permeability must not exceed 1.05 H/m. The magnetic permeability of certain aluminum bronzes is often less than 1.01 H/m, whereas that of austenitic stainless steels can be higher than this value if excessive ferrite is present.
Non-Sparking Characteristics
Excellent non-sparking characteristics make aluminum bronzes suitable for the manufacture of tools and equipment used in the handling of explosives, in mines, petroleum and chemical plants, gas-handling equipment and similar applications.
Back to TopCorrosion Resistance
Aluminum bronzes can be used in environments that are far more aggressive than are tolerated by most other metals, including even copper and the brasses used for general purposes. They can provide heavy-duty service at higher temperatures, in seawater environments and in the presence of many chemicals and acids. Much useful work has been done to characterize the corrosion resistance of these alloys so that best use can be made of them.
Like many copper alloys, aluminum bronzes also resist biofouling in both fresh and saline waters. This property is useful in propellers and especially so in seawater piping systems aboard ships and offshore platforms where, for example, fire safety systems depend on fouling-free piping for maximum flow.
Aluminum Bronze alloys may be considered for service with the following chemicals, particularly where there is a combination of stress and erosion, but selection must take account of the anticipated temperature, concentration and other service conditions.
Acetic Acid | Carbolic Acid | Glucose | Sewage |
Acetic Anhydride | Carbon Dioxide and | Glycerin | Soaps |
Acetate Solvents | Carbonic Acid | Glycerol | Sodium Bisulphate |
Acetone | Carbon Tetrachloride | Hydrocarbon Gases | Sodium Carbonate |
Alcohols | Caustic Potash | Hydrochloric Acid | Sodium Chloride |
Aldehydes | Caustic Soda | Hydrofluoric Acid | Sodium Hypochlorite |
Aluminum Chloride | Chlorine (dry) | Hydrogen | Sodium Nitrate |
Aluminum Fluoride | Chloroform | Inert Gases | Sodium Silicate |
Aluminum Hydroxide | Citric Acid | Lactic Acid | Sodium Sulfate |
Aluminum Sulfate | Coal Tar | Magnesium Chloride | Sodium Sulfide |
Ammonia (dry) | Coal Tar Solvents | Mineral Oils | Sulfur |
Amyl Chloride | Copper Sulfate | Naphthenic Acids | Sulfuric Acid |
Asphalt | Esters | Nickel Sulfate | Sulfurous Acid |
Barium Chloride | Ethers | Nitrogen | (moist SO2) |
Benzole | Fats | Oxalic Acid | Tannic Acid |
Borax | Fatty Acids(Oleic, Palmytic, Stearic) |
Oxygen | Tartaric Acid |
Boric Acid | Paints | Trichlorethylene | |
Brine | Fluosilicic Acid | Petroleum products | Tri-Sodium Phosphate |
Bromine (dry) | Formaldehyde | Phosphoric Acid | Zinc Chloride |
Calcium Chloride | Formic Acid | Pickling solutions | Zinc Sulfate |
Calcium Hydroxide | Freon | Potassium Sulfate | |
Calcium Hypochlorite | Fuel Gases | Refrigeration Gases | |
Cane Sugar Liquors | Gelatin | Seawater |
Freedom from Oxide Flaking
The outstanding corrosion resistance of aluminum bronzes in marine and chemical processing environments is due to the formation of an intrinsic, thin but tough adherent film of aluminum oxide. This film is self-healing and, once formed, prevents further oxidation and consequently eliminates the exfoliation of oxides so often encountered with ferrous alloys. This property, combined with the alloys' corrosion resistance and creep and fatigue properties at elevated temperature makes aluminum bronzes ideal for high temperature service. The aluminum bronzes have excellent resistance to stress corrosion cracking and corrosion fatigue; in fact, some alloys are especially chosen for these attributes. They are also rarely, if at all, susceptible to pitting and are generally far more resistant to selective attack than brasses.
Because strength is comparable to many ferrous alloys, it is possible, without radical re-design, to substitute aluminum bronzes where even mild corrosion of ferrous components is a potential problem. This applies particularly in critical areas of plant operation such as pumps and valves. Table 5 gives a comparison of the resistance to corrosion of various ferrous and non-ferrous alloys.
Alloys | General Corrosion Rate | Crevice Corrosion | Erosion- Corrosion Resistance | |||
---|---|---|---|---|---|---|
mm/yr | mm/yr | mm/yr | mm/yr | ft/s | m/s | |
WROUGHT ALLOYS: | ||||||
Phosphorus deoxidized copper |
1.6 | 0.04 | 0.9 | <0.025 | 6 | 1.8 |
Admiralty brass | 2 | 0.05 | <2 | <0.051 | 10 | 3 |
Aluminum brass | 2 | 0.05 | 2 | 0.051 | 13 | 3.9 |
Naval brass | 2 | 0.05 | 6 | 0.15 | 10 | 3 |
High tensile brass | 7 | 0.18 | 29 | 0.74 | 10 | 3 |
90/10 copper-nickel | 1.6 | 0.04 | <1.6 | <0.04 | 12 | 3.7 |
70/30 copper-nickel | 0.9 | 0 023 | <0.9 | <0 023 | 15 | 4.6 |
5% aluminum bronze | 2.3 | 0.06 | <2.3 | <0.058 | 14 | 4.3 |
8% aluminum bronze | 2 | 0.05 | <2 | <0.051 | 14 | 4.3 |
9% aluminum bronze | 2.3 | 2.9 | 0.06 | 0.074 | 15 | 4.6 |
Nickel aluminum bronze | 2.9 | 0.074 | <20 | <0.5 | ||
Aluminum- silicon bronze | 2.9 | 0.074 | 2.9 | <0.074 | 8 | 2.4 |
17% Cr stainless steel | <0.9 | <0.023 | 200 | 5.1 | >30 | >9 |
Austenitic stainless steel 304 | <0.9 | <0.023 | 0.9 | 0.23 | >30 | >9 |
Austenitic stainless steel 316 | 0.9 | 0.023 | 0.4 | 0.1 | >30 | >9 |
Monel | 0.9 | 0.023 | 1.8 | 0.5 | >30 | >9 |
CAST ALLOYS: | ||||||
Leaded Red Brass | 1.6 | 0.04 | <1.6 | <0 04 | 12 | 3.7 |
Red Brass (Gunmetal) | 0.9 | 0.023 | <0.9 | <0.023 | 20 | 6.1 |
High tensile brass | 8.7 | 0.22 | 0.9 | 0.23 | 8 | 2.4 |
Aluminum bronze | 2.9 | 0.074 | <2.9 | <0.074 | 15 | 4.6 |
Nickel-aluminum bronze | 2.9 | 0.074 | 2 | <0.51 | 14 | 4.3 |
Manganese- aluminum bronzes | 2.1 | 0.053 | 140 | 3.6 | 14 | 4.3 |
Austenitic cast iron (AUS 202) | 2.7 | 0.069 | 0 | 0 | >20 | >6 |
Austenitic stainless steel 304 | 0.9 | <0.023 | 9 | 0.23 | >30 | >9 |
Austenitic stainless steel 316 | 0.9 | <0.023 | 4.5 | 0.11 | >30 | >9 |
3% or 4% Si Monel | 0.9 | 0.023 | 1.8 | 0.5 | >30 | >9 |
Notes: Self-corrosion rate: For general long-term use over several years, a reasonable design value is 0.2 mil (0.05 mm) per year, but, under ideal conditions for nickel-aluminum bronze in seawater, a black film slowly forms, which reduces the corrosion rate in accordance with an equation of the form: |
Corrosion rate = kt-0.2
Impingement resistance: a maximum of 14 ft/s (4.3 m/s) is an appropriate design value for aluminum bronzes used in pipe systems carrying clean flowing seawater.
When Crevice corrosion occurs in nickel aluminum bronze, it takes the form of selective phase de-alloying and is usually of little practical significance since it has only a minimal effect on the surface finish. Crevice corrosion of austenitic stainless steels 304 and 316, although shallower, takes the form of pitting with consequent serious deterioration of surface finish.
The data in Table 5 are taken from U.K. Defense Standard 01/2 Guide to Engineering Alloys Used in Naval Service: Data Sheets. The figures for general corrosion rate and crevice corrosion were determined using samples fully immersed beneath rafts in Langstone Harbor for one year. General corrosion results were provided by freely exposed specimens; crevice corrosion results by specimens held in Perspex jigs providing crevice conditions between the metal sample and the Perspex. The corrosion/erosion resistance tests were carried out using the Brownsdon and Bannister test, the specimens were fully immersed in natural sea water and supported at 140°F (60°C) to a submerged jet, 0.016 in (0.4 mm) diameter placed 0.04-0.08 in (1-2 mm) away, through which air was forced at high velocity. The minimum sea water velocity required to produce erosion-corrosion under service conditions was estimated from the minimum air jet velocity required to produce erosion-corrosion in a fourteen-day test, and on the basis of known service behavior of some of the materials.
Back to TopCavitation Erosion
Nickel-aluminum bronze has a greater resistance to cavitation erosion than cast steel, Monel alloys and the 400 and 300 series stainless steels. By the same token, it has excellent resistance to impingement attack by gas bubbles. These characteristics make it particularly suitable for propellers, pump impellers, casings and turbine runners, enabling long service lives and optimum operating efficiency. Although more resistant to impingement attack by abrasive substances than gray cast iron and gunmetal, the aluminum bronzes are more vulnerable in this regard than cast steel and stainless steels. Filtration is sometimes necessary, therefore, in the case of high-speed pumps requiring the otherwise good corrosion and cavitation-erosion resistance properties of aluminum bronze but which have to handle water badly contaminated by suspended solids such as sand or other abrasives.
Tables 6 and 7 present comparisons of cavitation erosion of various ferrous and non-ferrous alloys in fresh water and in 3% NaCl (salt) solution.
Material | Depth of Attack |
---|---|
Nickel-aluminum bronze | 0.01 mil (0.025 mm) in 7 hours |
Austenitic stainless steel 321 | 0.12 mil (0.305 mm) in 7 hours |
High-tensile brass | 0.11 mil (0.280 mm) in 6 hours |
Material | Cavitation-Erosion Rate | |
---|---|---|
in3/h | mm3/h | |
Nickel-aluminum bronze | 0.0037 | 0.6 |
Aluminum bronze | 0.0049 | 0.8 |
Manganese-aluminum bronze | 0.0092 | 1.5 |
High tensile brass | 0.0287 | 4.7 |
Gunmetal | 0.0299 | 4.9 |
Monel K500 (cold drawn) | 0.0171 | 2.8 |
Monel K500 (aged) | 0.0073 | 1.2 |
Austenitic stainless steel 321 | 0.0104 | 1.7 |
Austenitic stainless steel 316 | 0.0104 | 1.7 |
Cast martensitic stainless steel 420 | 0.0104 | 1.7 |
Cast austenitic stainless steel 347 | 0.0061 | 1.0 |
Spheroidal-graphite cast iron | 0.0079 | 1.3 |
Ni-resist iron | 0.0269 | 4.4 |
Also in this Issue:
- Aluminum Bronzes - Part II
- Aluminum Bronzes - Part I