Copper - Keeping Up Appearances
Copper Applications in Architecture
Since the beginning of the Bronze Age, almost 5000 years ago, bronze, an alloy of copper and tin, has been pre-eminent as the material for sculptors to immortalise their creations. The discovery that a mixture of copper and tin could be melted and then cast into moulds to produce both useful and artistic objects led to a prolonged period in time when bronze was treasured and often hoarded because of its unique properties.
Sculptures, in particular, were produced in bronze because they had the ability to retain their natural colour, even when outdoors. Bronze slowly takes on a pleasant appearance due to the formation of a patina, the name given to the corrosion product that forms on the surface of the bronze. How this patina is formed is quite complex and will not be considered here, except to note that the major constituent is called brochantite, a mixture of basic copper sulphates and copper carbonate. The patina is not a solid film, but is slightly porous.
There is now a considerable heritage of bronze sculptures in both the public and private domain that require periodic attention to ensure that their aesthetic appearance is not marred by the modern environment.
Indoor exposure of bronze does not present a problem, and there are many fine examples of sculptures that have aged gracefully with time and have developed an aesthetically pleasing patination. Art experts agree that it is imperative to retain this patination, which takes years to develop, and that it should not be destroyed by aggressive cleaning.
Outdoor exposure of bronze sculptures is invariably more aggressive than indoor exposure, and the degree of aggression is related to situation. Rural exposure is the least aggressive, urban exposure is more aggressive and industrial exposure is the most aggressive. This aggression shows itself in an increase in the rate of patination and also a change in the composition of the patination, and is related to the constituents of the atmosphere at the exposure site.
Long exposure outdoors in an aggressive environment can lead to too great a patination, resulting in some of the corrosion products being washed off and re-deposited as stripes on the sculpture. The shape of the sculpture determines how rainwater runs off the sculpture and hence where the stripes are formed. Although the overall patination is still acceptable, the stripes, and sometimes black spots, that are formed detract from the overall aesthetic appearance. Figures 1, 2 and 3 shows examples of striping and spotting.
![]() |
![]() |
![]() |
Figures 1, 2 and 3. Shows examples of striping and spotting. |
Curators and conservators of outdoor sculptures have an aesthetic dilemma. Patination of public sculptures has to be preserved to retain the beauty of the bronze, however the 'over-patination' is detrimental. Should it be cleaned and removed? If the excess patination is removed how is it stopped re-occurring?
Guides to the maintenance of outdoor bronzes have been suggested but there is no agreement between experts in different countries on the optimum cleaning and maintenance procedures that will retain the aesthetic appeal of the sculptures. Should sculptures be preserved or should the natural patina, which can be damaged and discoloured, be cleaned off in order that the bronze can regain its original, even patina?
On the basis that prevention is better than cure one solution is to provide protection that can be applied to the sculpture once an acceptable degree of patination has been reached. In some cases the patination might be artificially produced by chemical treatment to avoid the long times required for natural patination. If the protection prevents further patination, no deterioration in appearance will result. Such techniques are currently available.
Waxes and lacquer coatings have been used but have disadvantages. Waxes will last for about 1 year only, and then have to be re-applied, so although treatment is effective it has to be continually repeated; not a very satisfactory solution. The accessibility of some public sculptures also presents problems for such periodic treatments. Organic polymers such as epoxy or acrylic resins have also been used but break-down in sunlight after about 5 years, and turn yellow and embrittle with age. Both of these conditions are undesirable, yellowing affects appearance, and embrittlement results in the coating flaking-off, removing protection, and also detracting from the appearance of the sculpture.
Incralac® was specially developed under funding from what is now ICA, International Copper Association; it is very effective and has been available for many years. It is an acrylic resin to which benzotriazol has added to improve its long-term stability. Although effective, longer exposure (now up to 13 years), has shown that this proprietary coating is also subjected to darkening or blackening on exposed edges when used outdoors.
As preservation of historic and aesthetic bronze monuments presents problems for all European countries, the European Commission have funded a collaborative project, number EV5V-CT92-0107, on 'Environmental Protection and Conservation of the European Cultural Heritage' with several European partners and co-ordinated by the Fraunhofer Institut fòr Silicatforschung, Würzburg, Germany. The objective of the project was to develop a coating technique that would provide long-term protection, preserve the patination that had already developed, but which could be removed at some future date without damage to the underlying patination. The latter was important in that it would allow curators and conservators to change their conservation process if subsequently conservation policy changed and alternative techniques have to be adopted.
The base material used in this latest coating technique is a heteropolysiloxane, a so-called ORCOMER®. This is a corruption of ORganically MOdified Ceramic. The relationship between the constituents of the ORCOMER is shown in Figure 4. Effectively the new class of material combines the surface properties of the silicones, the toughness of the organic polymer coatings, and the hardness and thermal stability of ceramics. In practice the starting materials themselves are quite complex but what happens during the preparation of the important base solution for the coating is as follows.
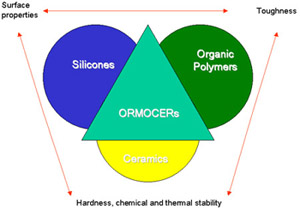
A non-cross-linkable organofunctional hydrosilicon (the so-called network modifier) is reacted with a cross-linkable organofunctional hydrosilicon (the network former). The network modifier has a general formula of:
R 1 p Si X 1 (4-p)
where
R 1 is an aryl group (an aromatic ring of C and H)
X 1 is an OH, Cl or alkoxyl group (a chain of C, H and O atoms)
And p is in the range 1 to 3
The collaborative project determined that a suitable compound is diphenylsilanediol.
The network former has a general formula of:
R 2 m (R 3Y) n Si X 2 (4-m-n)
where
R 2 is a complex aryl group
R 3 is a complex alkoxyl group
Y is polymerisable, that is its molecules are able to join together to form very large chainlike or network molecules.
X 2 is again a complex group of H, Cl, C and H
m and n are whole numbers
m + n = 1 to 3
Again, the collaborative project determined that suitable compounds are gamma-glycidoxypropyltrimethoxysilane and 3-metylyoxypropyltrimethoxysilane.
Because the formulae and names are somewhat daunting it is easier to talk about the constituents in terms of what they do, rather than use their chemical names, consequently they will be referred to as network formers and network modifiers. It is important to note that both the network former and the network modifier are Si containing which will ensure that silicone-like properties (non-wettability) are produced in the final coating, as well as silica-like properties (chemical and thermal stability). There are also organic constituents in them that ensure cross-linking and assist in the film forming properties of the coating.
The network former and the network modifier are reacted together at 80 to 85�C with water to form a clear liquid which can be further diluted with a suitable solvent (butoxyethanol) and used as the basis for spraying compositions. In this form it is known as GDiphenyl for convenience.
If a one-coat application is required, the GDiphenyl is diluted further and mixed with a solution of a stiffener, a suitable one being a copolymer of ethylene methacrylate and methyl methacrylate, known as Paraloid 72. The last step is to add a small quantity of a catalyst. A suitable catalyst has been found to be N-2-aminoethyl-3-aminopropyltriethoxysilane, known as DAMO. The solution is then sprayed onto the bronze surface and left to cure at room temperature. If the stiffener were not added the simple cold cured coating would be too soft, because there would be inadequate cross-linking of all possible molecules, and although this is an advantage in that the coating is pliable and does not crack, it is liable to be damaged by scratching. The catalyst is provided to initiate the cross-linking of the molecules during the cold curing of the coating after spraying. The curing at room temperature is simply the final cross-linking of the molecules at room temperature. As cross-linking precedes, the molecules join together and the larger they become the more difficult it is for them to move past each other, and the coating becomes stiffer and stiffer, in other words its viscosity increases dramatically. Eventually the once liquid film is transformed into an adherent solid coating on the bronze surface.
When applied to a bronze surface that has been degreased with acetone or cleaned with water a single layer will be about 3 micrometers thick and will dry in about 16 hours at room temperature. A second layer can be applied after about 4 hours to form a 6 micrometer thick coating.
If a two-coating technique is used the GDiphenyl is again diluted and mixed with the catalyst DAMO only. This mixture is sprayed onto the bronze surface and the coating dries in about 16 hours. On top of this first coat a solution of Paraloid 72 is applied as a second coat, giving an overall coating thickness of some 10 micrometers.
The coating of GDiphenyl with admixed stiffener, Paraloid 72, and catalyst, DAMO, when cured has a chemical structure conferred upon it by the chemical characteristics of the Si element that ensure good adhesion to metallic surfaces and also to mineral salts such as the patina. Their hydrophobic properties are also low, that is, they have low wetting by moisture, improving their weathering protection, and are chemically and thermally stable.
Figure 5 shows schematically the steps to a one coat, and two coat process.
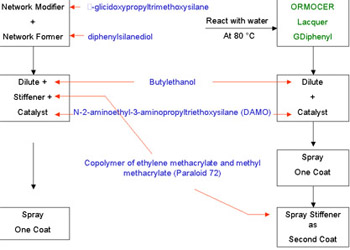
One over-riding factor of importance is that the GDiphenyl films with added stiffener produce coatings that are highly protective but still have a low degree of cross-linking, and this means that the coatings can be removed using a suitable organic solvent even after long periods of time.
The final coatings developed are clear, highly protective both from atmospheric attack and deposits of dirt, dust and organic deposits, have low wettability by water, are subtle and do not crack, are stable after long curing times, and are removable without damage to the underlying patina.
As part of the collaborative project many samples were coated and examined in order to determine the optimum compositions of the network former, modifier, stiffener and catalyst. Several pilot applications were carried out to observe coatings under natural conditions. Different countries adopted different strategies, one preserving the natural patina that had developed, and another using different cleaning techniques before applying the protective coating. The outdoor sculptures treated are to be re-examined with time to establish the long-term protection offered by the new coating technique.
This development will allow curators and conservators to decide on a conservation strategy using these coatings knowing that the sculptures they are at pains to protect are not damaged by the coatings, which can be removed subsequently, should this be required. Quite an achievement. The Fraunhofer Institut has now found one company to produce and distribute the new lacquer. In addition they co-operate with restorers and provide a coating service themselves.
The ability to freeze in time, the most attractive appearance of bronze sculptures, is a delight that we can all share and admire.
Innovations wishes to thank Dr. Hannelore R�misch of the Fraunhofer Institut f�r Silicatforschung for providing the information and illustrations contained in this article. The patent covering the innovation is US 5,756,158.
Also in this Issue:
- Copper - Super Slim Gas Seals
- High Tech House Runs on Copper
- Copper - Keeping Up Appearances
- Copper/Cobre 99 a Success