Herman Miller, Inc. is one of the worlds leading manufacturers of office, healthcare and home furniture. Founded in 1923, the Zeeland, Michigan-based company has grown steadily to become a $1.75 billion (sales) international market leader. The company is proud of its growth and profitability, having recently enjoyed some 14 quarters of record sales and net income.
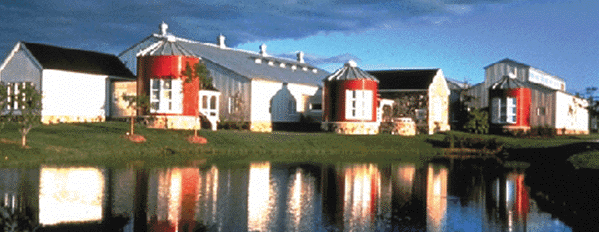
Herman Miller can point with equal pride to its broad-based environmental program, an important element of which is a comprehensive, company-wide effort to maximize energy conservation. The conservation program isnt just a token effort; the company has successfully reduced energy costs by more than $1 million annually since 1991 and its currently looking to reduce energy use in buildings by 30% over the next seven years. Herman Miller joined the EPA Green Lights Program a number of years ago, and in January 1999, Herman Miller became an Energy Star Buildings company, as well. This is a company that understands that saving energy can significantly improve profitability.
Which brings us to the subject of this article: saving energy-and lots of money-with high-efficiency, copper-based electrical equipment.
The Design Yard-A Model Facility
A unique cluster of the Herman Miller offices and studios they call the Design Yard is home to design and development teams for several of the companys product lines. Its affectionately referred to as "The Barn Yard" because it looks like a large farm, with buildings that blend into the surrounding countryside. The Design Yard was designed to be an environmentally friendly neighbor, a comfortable workplace and an attractive setting to display the companys products in an actual work environment.
The Design Yard is also a highly energy-efficient facility, thanks in part to a Herman Miller management team called the Green Building/Facility Design Group. (Yes, they really do have a team that worries about "green" buildings. That may be why the company has been ranked as one of the top three companies for environmental responsibility for the last three years by Fortune Magazine.) The group is made up of Herman Miller facilities managers and engineers, whose jobs are, in the companys words, "...to specify the most sustainable practices and designs for existing and new buildings." If you havent guessed by now, sustainability, energy efficiency and corporate "greenness" are taken very seriously at Herman Miller, Inc.
Economic Value Added- A Powerful Decision-making Tool
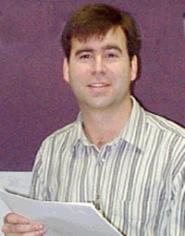
Energy Manager
Herman Miller Inc.
To help make project-related and purchasing decisions, the GB/FD Group relies on a performance measurement system called Economic Value Added (EVA). Simply put, EVA judges a projects performance in terms of long-term continuous improvements and the creation of economic value for the company. Its a powerful decision-making tool. Company managers use it because they know it works.
Mitch Boucher is one of those managers. Mitch is Herman Miller, Inc.s energy engineer. He supports and coordinates energy purchasing and conservation projects and supports facilities managers in each of the companys manufacturing sites. Herman Miller currently has three million square feet of facilities under roof in North America alone. Mitch holds a BSEE degree from Michigan State. He cut his energy-saving teeth at Edison Sault Electric, so he understands energy conservation from both the utilities and users viewpoints. Mitch explains EVA this way: "The EVA of a project is a combination of the income and balance sheet and how each of these are affected by the projects economics. We get to finance a project according to our internal borrowing rates and apply any benefits that accrue to our income statement. The procedure allows us to take credit for benefits such as tax savings, reduced inventory and lower operating expenses.
EVA helps us to look at a project in terms of the net operating profit after taxes, or NOPAT. If we can borrow money for a project, pay interest, receive all the depreciation and such, pay taxes on the income released or generated and show a positive NOPAT, then we should go ahead with the project because it is growing the business and adding economic value to the corporation."
New Transformer Specified
Mitch is also chairman of the energy subgroup of Herman Millers Environmental Quality Action Team and co-chair of the Sustainable Facilities Team. In 1998, these teams helped the company lay plans for a 21,000-sq ft (2,100-sq m) addition to the Design Yard to house the companys executive leadership team and provide workspace for corporate support staff. The new space would require a power source, so the energy teams drew up specifications for a new 750-kVA transformer.
Their RFQ yielded seven candidate transformers: four standard-efficiency models, representing three suppliers, with prices ranging from $10,100 to $13,700, and three high-efficiency models, from two suppliers, costing between $10,548 and $15,490.
When requesting quotes for the new transformer, the group took the unusual but very sensible step of requesting bidders to provide load and no-load losses along with the usual price and delivery information. As expected, the standard models claimed no-load losses around 1600 VA and full-load losses in the 8000-VA range. The high-efficiency models claimed no-load losses around 1000 VA and full-load losses around 6700 VA (see table). The engineers assumed their new transformer would operate continuously throughout the year but would operate under full load for only a single shift, or 2800 hours per year.
Here are the numbers:
Assumptions:
Transformer rating: | 750 kVA |
Number of shifts loaded: | 1 (2800 h/y) |
Energy cost: | $0.053/kWh |
The Total 15-Year Operating Cost is calculated as: | |
Operating Cost (in $) = | [(NLL x 8760 x 0.053) + (FLL x 2800 x 0.053)] x 15 |
Where: | |
NLL = No load losses (kVA) | |
FLL = Full load losses (kVA) | |
Estimated full load hours per year (based on one shift operation) = 2800 | |
Total hours per year = 8760 | |
Note: The simplified table below does not account for taxes, depreciation or the time value of money |
Evaluation:
Plugging the bidders cost and operating data and the estimated duty cycle numbers into an EVA analysis, the teams came up with purchase recommendations based on a 15-year total owned cost (TOC).
Option | Transformer Manufacturer | Purchase Price | No-Load Losses, VA | Full-Load Losses, VA | One-Year, Operating Cost | 15-Year Operating Cost | Total 15-Year Owning Cost |
---|---|---|---|---|---|---|---|
Standard Efficiency #1 | G | $13,700 | 1780 | 8013 | $2,016 | $30,233 | $43,933 |
Standard Efficiency #2 | G | $10,194 | 1647 | 9507 | $2,176 | $30,233 | $43,933 |
Standard Efficiency #3 | B | $10,795 | 1573 | 7289 | $1,812 | $27,180 | $37,975 |
Standard Efficiency #4 | C | $10,100 | 1647 | 9507 | $2,176 | $32,633 | $42,733 |
High Efficiency #1 | G | $15,490 | 1107 | 6503 | $1,479 | $22,185 | $37,675 |
High Efficiency #2 | C | $10,845 | 1018 | 6769 | $1,477 | $22,157 | $33,002 |
High Efficiency #3 | C | $10,548 | 1018 | 6769 | $1,477 | $22,157 | $32,705 |
A life cycle cost analysis should take into account all associated costs and savings, when they occur, and using the time value of money, convert them into a present value. Herman Millers purchasing department has derived simplified figures that take into account their future value of money, taxes, cost of borrowing, overheads, etc. As a general rule for smaller projects like this one, the company applies a factor of 60% to the cost-reduction benefits (in the form of lower operating costs), and a factor of 11% to the incremental purchase price, which represents their capitalized carrying cost. (Both these factors will be different for another purchaser.) These percentages, expressed as decimals, are used to calculate the transformers Economic Value Added (EVA):
EVA = | [(Low-First-Cost Transformer 1-year Operating Cost) (Best-Choice Transformer 1-year Operating Cost) x (0.6)] [(Best-Choice Transformer Purchase Price) (Low-First-Cost Transformer Purchase Price) x (0.11)] |
In this case, the EVA turned out to be a favorable +$370.12.
Results of the Total-Owned-Cost analysis were even more positive. Purchasing the lowest TOC transformer instead of the lowest first-cost transformer yielded an estimated return on investment of 156%. Looked at another way, the simple payback period for purchasing the lowest TOC transformer was only seven months!
With a total 15-year owned cost of $32,705, the best choice is unquestionably the copper-wound, high electrical efficiency transformer designated "High Efficiency #3." The difference in 15-year total owned costs between the best-choice transformer and the lowest-first-cost model (Standard Efficiency #4) is estimated to be more than $10,000, almost equal to the purchase price. In fact, the high-efficiency transformer will literally pay for itself in energy cost savings.
The lesson learned is clear: pay a little more up front for a high-efficiency transformer and save a bundle over the life of the unit, or save a few dollars on a low-first-cost standard efficiency transformer and continue to spend a lot more money on wasted electric power for years to come.
As for the environmental benefits, the subject thats so very important to Herman Miller, Inc.: high electrical energy efficiency means lower energy usage, lower fossil fuel consumption and lower greenhouse gas emissions. For Zeeland, Michigans environmentally friendly furniture maker, the new transformer is a win-win situation.
More than Transformers
The economic benefits of energy-efficient equipment such as the transformer described here extend to other copper-intensive devices, as well. Tops on the list are high-efficiency electric motors, especially integral-horsepower motors that operate at high duty cycles. High-efficiency motors typically claim between two and three percent higher efficiency than standard motors, and thats a lot. Like the high-efficiency transformer installed by Herman Miller, their improved efficiency enables the motors to pay for themselves, often in a matter of months.
Copper busbars and upsized power cables are energy-savers, too. Because of their lower I 2R losses compared with NEC®-minimum cable sizes, the larger-sized busbars or cables are guaranteed to save moneyand coppers superior connectability ensures that joints will be trouble-free.
Herman Miller, Inc. agrees: "Our electricians tell me that Herman Miller is standardized on copper," says Mitch Boucher. "We always use copper wire for the lower losses and better fault handling capability it provides. For example, secondary feeders into the buildings two 600-A service panels are 500-kcmil copper instead of aluminum."
"Copper also helps us ensure power quality. Our (480 V:120/208 V) secondary transformers for office workstations and telecommunications are of the isolation type, copper-wound. Secondary workstation and telecom circuits are also all-copper with separate (not shared) full-size neutrals for each circuit. The primary cables are 4/0 copper, EPR 133% insulation, with a concentric copper neutral."
High-efficiency copper equipment, reliable, energy-saving copper electrical circuits and an environmentally friendly company. It all adds up to a sound bottom line.
Herman Miller Inc.
The Herman Miller Company is one of the worlds leading manufacturers of office, residential and health care furniture and services. Founded 75 years ago in Zeeland, Michigan, the company now employs over 7,500 men and women and has subsidiaries, licensees, sales offices and dealerships in over 40 countries.
The company is best known for its innovative designs. The worlds first open-plan office furniture system was introduced by Herman Miller in 1968. This and many other Herman Miller designs are displayed in museums throughout the world. The company has also developed a unique management philosophy centered on employee participation. A performance measurement and compensation system called Economic Value Added (EVA) links operating and financial performance to incentive compensation for every employee, shifting focus from the balance sheet to short- and long-term continuous improvements that create economic value. The EVA calculations included in this article describe only one application of this broad-based management tool.
Herman Miller is equally well recognized for its dedication to preserving and nurturing the natural environment. As they put it: "Our business is part of the environment, so our environment must be part of our business." Among other awards, Herman Miller has been repeatedly cited by Fortune Magazine as one of Americas most environmentally responsible companies.
The company implements its commitment to the environment through a number of action teams, one of which is the Green Building/Facility Design Group described in the accompanying article. CDA is pleased that the managers and engineers who make up the Green Building/Facility Design Group recognize the value of high-efficiency copper-based transformers in reducing their companys energy consumption.