- Introduction
- Supply, Production, Distribution
- Structure, Properties
- Machinability
- Corrosion Resistance
- Design Freedom
- Summary
Introduction
This paper is intended as a brief primer on Free-Cutting Brass, UNS C36000. Free-Cutting Brass, which many people know by it's traditional name, CDA Alloy 360, is the most important commercial copper alloy, surpassing all but copper itself in terms of annual consumption. Exact quantities are difficult to calculate, but over 600 million pounds of Free-Cutting Brass are consumed in the U.S. each year.
Despite this large usage, brass is underutilized as an automatic screw machine feedstock. Perhaps ten times more leaded steel is used than Free-Cutting Brass. In general industrial products, and brass screw machine parts are scarce enough today in automotive vehicles to be listed as an endangered species.
Are the properties of leaded steel uniquely needed when making screw-machine parts? Is leaded steel so cheap that brass can only be justified for a small number of specialty products? Or, as some suspect, is steel specified more out of tradition than actual need... or simply in error based on off-the-shelf cost considerations that neglect actual net cost? CDA surveyed engineers, designers, purchasing agents and automatic screw machine operators to find the answers. To our surprise, we learned that:
- Tradition dominates material selection, especially in the automotive industry. Of 25 screw machine parts randomly selected by one automaker, 23 had always been specified in leaded steel, yet no one could explain why;
- Most designers, engineers and purchasing agents are convinced brass is too expensive for simple products. Reason: brass's raw materials costs appear to be more than twice as high as steel (although few are aware that finished brass parts cost less);
- Some designers think brass's mechanical properties are inadequate, even though leaded steel is relatively weak and can't be heat treated;
Extra cost for corrosion protection (plating) is taken for granted.
In short, CDA found that while most automotive designers and engineers know a little bit about Free-Cutting Brass, few individuals surveyed know enough about the material to consider specifying it for automotive products. Clearly, the brass industry is facing an information gap. Here, then, is some basic information about Free-Cutting Brass: how it is made, what it's properties are and what advantages it offers to automotive designers.
Back to TopSupply, Production, Distribution
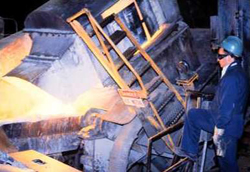
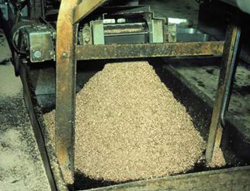
Supply
Most Free-Cutting Brass is produced domestically at seven major U.S. brass mills. There are also a number of smaller mills and three captive shops. Brass imports account for about eight percent of domestic consumption, but they nearly equal exports on a tonnage basis. Bottom line: the U.S. is comfortably self-sufficient in Alloy C36000.
While some domestic mills specialize in a select number of alloys, and others offer a large variety of compositions, all brass rod mills in the USA produce Free-Cutting Brass. Some mills concentrate on rod and bar products while others supply rods and bars as well as wire, shapes and custom extrusions. Customers obviously benefit from this large, diversified market.
Production
The production of Free-Cutting Brass begins by melting the proper composition (nominally 61.5% copper, 35.40/o zinc and 3.1% lead) in induction furnaces, Figure 1. Melt stock consists of scrap copper, ingot and scrap zinc and lead, plus brass scrap and turnings. Scrap and turnings are very important raw materials. More than one-half of all Free-Cutting Brass is recycled, which is not surprising since the average screw machine part generates more than it' finished weight in chips, Figure 2. The large volume of recycled brass insures continuity of supply. The turnings are also an important quality buffer. With more than one-half of the metal in the system re-circulating continuously as clean turnings of a single alloy, the composition, properties and quality of American-made brass tend to remain uniform. An added benefit is that re-melted brass turnings consume a lot less energy than it takes to mine, smelt and refine copper, zinc and lead.
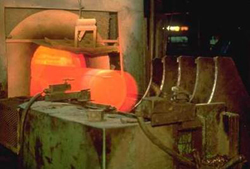
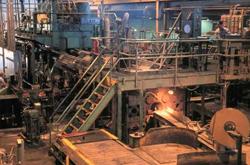
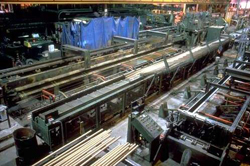
With almost all Free-Cuffing Brass destined for automatic screw machine production, uniformity is extremely important. American brass mills are deservedly well-known for the control systems that assure the needed quality. Alloy composition is maintained within limits that astound foreign producers. Product soundness, dimensions, shape, straightness and mechanical properties conform to established standards, including SAE J463 Wrought Copper and Copper Alloys, ASTM B248 (plate, sheet and rolled bar), ASTM B249 (rod, bar and shapes), ASTM B250 (wire) and ASTM B251 (pipe and tubes).
Distribution
Brass is distributed to screw machine houses through metal service centers or, for large customers, directly from the brass mills. Commercial arrangements negotiated between the mill and the machine shop can include provision for credit against cost to recycle the brass turnings. This lets the customer realize an advantageous net material cost, and makes for better control over raw materials costs. Unfortunately, not all of the people who buy screw machine products - including automotive purchasing agents - appreciate the importance of these everyday commercial practices that are the basis for brass's truly low cost.
Back to TopStructure, Properties
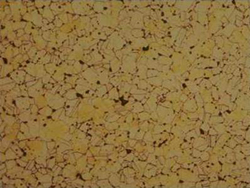
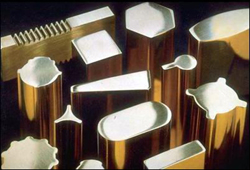
Free-Cutting Brass is almost always supplied in the half-hard (HO2) temper for screw machine applications, although soft annealed (060) and Hard (HO4) tempers are also available for special-purpose applications. Most screw machine feedstock is sold in round and hexagonal rod in sizes ranging from 12 to 38 mm (to 1 1/2 in). Smaller and larger-diameter rods, as well as octagonal rod, square and rectangular bar, flats and a wide variety of standard and custom shapes are also available, Figure 6. Domestically produced products must conform with the requirements of ASTM B 16.
Many designers are surprised to learn that in the half-hard condition, C36000's properties are roughly comparable with steel. Actually, brass's strength falls in a range between hot rolled and hot-rolled and cold reduced AISI 12L14 leaded steel. The properties data in Table 1 show that specifying hard C36000 in place of cold-drawn leaded steel entails a sacrifice of only about 10% in yield strength. Notice the two sets of mechanical properties for brass: the lower values represent the specification minimums as given in ASTM B 16; the higher set represents typical or nominal values.
Yield Strength | Tensile Strength | % Elongation | Shear Strength | |||||
---|---|---|---|---|---|---|---|---|
Material Diameter | Condition | Minimum Specs. | Typical or Nominal | Minimum Specs. | Typical or Nominal | Minimum Specs. | Typical or Nominal | Typical or Nominal |
in | Ksi | Ksi | Ksi | Ksi | Ksi | |||
mm | MPa | MPa | MPa | MPa | Mpa | |||
UNS C36000, Rod | ||||||||
< 1.0 | Soft | 20 | 22 | 48 | 50 | 15 | 36 | 30 |
< 25.4 | 138 | 152 | 331 | 345 | 207 | |||
1.0-2.0 | Soft | 18 | 21 | 44 | 48 | 20 | 32 | 29 |
25.4-50.8 | 124 | 145 | 303 | 331 | 200 | |||
> 2.0 | Soft | 15 | 19 | 40 | 45 | 25 | 36 | 28 |
> 50.8 | 103 | 131 | 276 | 310 | 193 | |||
< 0.5 | Half Hard | 25 | 42 | 57 | 65 | 7 | 15 | 38 |
< 12.7 | 172 | 290 | 393 | 448 | 262 | |||
0.5-1.0 | Half Hard | 25 | 42 | 55 | 60 | 10 | 23 | 34 |
12.7-25.4 | 172 | 290 | 379 | 414 | 234 | |||
1.0 - 2.0 | Half Hard | 20 | 37 | 50 | 54 | 15 | 31 | 32 |
25.4-50.8 | 138 | 255 | 345 | 372 | 221 | |||
> 2.0 | Half Hard | 15 | 28 | 45 | 50 | 20 | 35 | 30 |
> 50.8 | 103 | 193 | 310 | 345 | 207 | |||
0.125-0.188 | Hard | 45 | 58 | 80 | 85 | 7 | 47 | |
3.2-4.8 | 310 | 400 | 551 | 586 | 324 | |||
> 0.188 | Hard | 35 | 52 | 70 | 75 | 4 | 9 | 42 |
> 4.8-7.9 | 241 | 358 | 482 | 517 | 290 | |||
AISI/SAE 12L14, Bar | ||||||||
0.125-1.250 | Hot Rolled | 34 | 57 | 22 | ||||
20-30 | 230 | 390 | ||||||
0.125-1.250 | Cold Reduced | 60 | 78 | 10 | ||||
20-30 | 410 | 540 |
On the basis of strength alone, brass can safely be substituted for leaded steel in the majority of common screw machine products. Such products have modest to intermediate strength requirements (AISI 12L14 is not heat-treatable, for example).
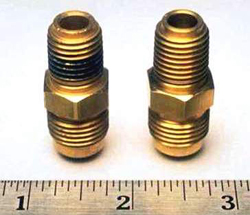
Machinability
The most important feature of C36000 is, of course, its unexcelled machinability. No material of comparable strength machines faster and produces better surface finishes than Free-Cutting Brass. Brass's two-phase structure tends to form broken chips instead of continuous coils, which would interfere with high speed machining. Lead acts synergistically with the alpha-beta structure, causing chips to shatter into tiny fragments. Lead also provides some internal lubrication against the surface of the cutting tool.
Maximum recommended form-tool and single-point cutting speeds for Free-Cutting Brass are between 300 and 1,000 sfm (surface feet per minute) with high speed steel tooling and between 500 and 1,600 sfm with carbide. Corresponding maximum speeds for leaded steel range between 200 and 300 sfm (about 10% higher in proprietary resulfurized, rephosphorized, tellurium- or selenium-treated grades). Screw-machine operators tend not to run their equipment at maximum speed for either brass or steel and therefore don't take full advantage of brass's high-speed capability, but the difference between these "handbook" machinabilities for brass and steel shows what could be accomplished, if pursued. In fact, Free-Cutting Brass's machinability far surpasses the speed capacities of today's fastest commercial machine tools. Major breakthroughs are still a few years into the future, but ultra-high speed machining at up to 18,000 sfm (5,500 meters per minute) has already been demonstrated on a pilot scale in Europe.
Brass's high machinability also means measurably better surface finishes than can be achieved with leaded steel, even at brass's faster cutting speeds and higher feed rates. Dimensional control is simpler with Free-Cutting Brass because of substantially reduced tool wear. Fewer out-of-tolerance parts mean lower rejection rates and lower net production costs.
Back to TopCorrosion Resistance
When exposed to the atmosphere, brass tends to form a protective tarnish film that impedes corrosion beyond a few micrometers into the metal surface. The tarnish will deepen in color from bronze to dark brown, and may eventually take on the green color of a patina in some environments. The important point is that brass's corrosion rate in normal atmospheric conditions is low and self-limiting, and the corrosion products that do form are not objectionable.
In addition to atmospheric corrosion resistance, brass also withstands exposure to a wide range of water compositions, including automotive coolant solutions. Brass is generally inert to organic liquids and gases, although it should not be used in mineral acids or acid salts. Alkaline salts are less objectionable.
Brass is susceptible to three types of corrosion. These include stress-corrosion cracking, which can arise in ammoniacal environments, amines, mercury compounds and nitrite solutions. Sulfides will promote pitting attack of copper and copper alloys, especially under alternating aerobic and anaerobic (sulfiding) conditions such as might be caused by episodic exposure to polluted seawater. Brasses are perhaps the least susceptible copper alloys to sulfide pitting. Also, road salt solutions contaminated with sulfide-laden exhaust emissions do not appear to affect brass. Brass can, immersed in acidic and mildly basic waters, corrode by dezincification, but this also has not been a problem in automotive applications. (For service in such environments brass compositions are modified by small additives of alloying elements that inhibit dezincification.)
For additional information on corrosion and copper alloys see the Copper Alloy Corrosion Database.
Automotive screw machine parts of steel are normally plated with either zinc or cadmium. Chromate conversion coatings, over the electroplate, are also common. This practice has been favored by automotive designers for many years, but it has three serious disadvantages. First, largely because of stringent environmental regulations, plating has become very expensive. It now costs about 180 per pound of product for zinc/chromate, 240 for cadmium, more still for electroless nickel and zinc-iron. Second, threads, recesses and deep holes are extremely difficult to plate uniformly. This leads to uneven protection and poor performance.
Third and most important, plated parts have a limited lifetime. This means the functional value of the electroplated surface is eventually lost, while the decorative value of freshly plated fittings soon gives way to telltale rust stains.
Brass, of course, doesn't require electroplating to withstand common automotive environments. However, if plating is desired or required, brass does accept decorative or protective electroplating very easily. A variety of durable and economic lacquers are also available to display the natural beauty of the metal itself.
Back to TopDesign Freedom
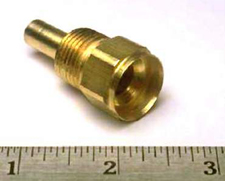
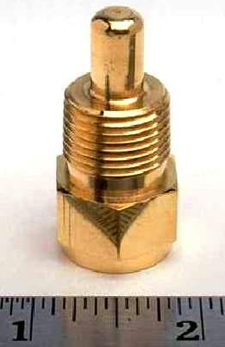
Brass lets the designer specify deep blind holes without concern for tool breakage and high rejection rates. Figure 8 shows an automotive sensor housing that, because it is now made from brass, doesn't require electroplating to protect the deep recess.
Brass also accepts fine detail and excellent surface finishes without extracting a cost penalty for slow cutting speeds and expensive tooling. Figure 9 provides a good example.
Brass can simplify designs, and simpler designs can lower costs while improving product quality. Both Figure 10 and Figure 10a show high-pressure hydraulic fittings once made from steel. They were assembled from two machined pieces because chips wouldn't clear from the deep trepanned recess between the hose nipple and the outer clamping shell. One solution was to make the steel part from several components, brazed or resistance welded together. An innovative parts designer, who happened to have some screw machine experience, now makes the parts in one piece using Free-Cuffing Brass. Only brass allows the design freedom that makes a part like this possible.
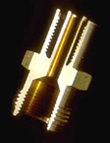
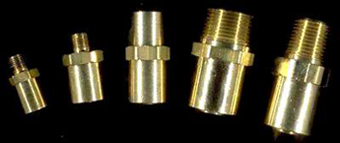
Finally, the availability of Free-Cutting Brass in a large variety of geometric shapes can often eliminate machining operations entirely. In addition to a few standard shapes, a number of custom shapes are also shown in Figure 6.
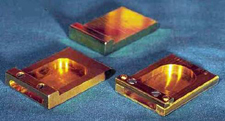
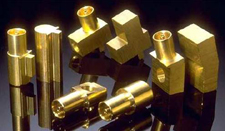
Custom shapes can be extremely cost-effective, and production volumes need not be high to amortize the surprisingly modest die costs. Figure 11, a simple fuse adapter, illustrates how using a profiled extrusion did away with the need for several components, a number of machining steps and one assembly operation. This reduced the product cost without affecting quality or function. The automotive fluid connectors shown in Figure 12 are also made from custom shapes. The custom shapes make it possible to produce a complex part as one piece, with a reduced amount of machining, and eliminating the need for secondary assembly operations. Additional benefits of the design in brass were the elimination of some hose clamps, due to improved routing of the flexible hose and far superior corrosion resistance.
Summary
Here are the important points to bear in mind when considering Free-Cutting Brass for screw machine products:
- Brass is widely available and in plentiful supply. The U.S. is self-sufficient in the alloy;
- Brass' quality is assured by adherence to numerous standards;
- Brass' mechanical properties in service are adequate for the majority of parts produced on automatic screw machines;
- Brass' extremely high machinability translates into lower product costs, compared with leaded steel;
- Brass' close dimensional control and high surface finishes will be reflected in higher product quality;
- Brass' natural corrosion resistance eliminates the need for expensive electroplating. Customers perceive and appreciate the quality inherent in solid brass components; and
- Brass gives the designer freedom to conceive parts that would not be economical in steel.