- Plenty of Bad Suggestions
- Searching for Clues
- Finally, a Real Expert
- Solution Relies on Copper
- Grounding and Network Signal Noise
CNC equipment is commonplace in tool & die shops, so to gain a competitive edge McAfee began networking its equipment almost eight years ago, when networks were still considered cutting-edge stuff in the tool & die business. Networking its equipment enables McAfee to store more than 20,000 computer-aided design/computer-assisted manufacturing (CAD/CAM) programs centrally, making them instantly accessible to the CNC machine operators. Networking also provides more efficient machine-time utilization, better administrative control and lower overhead costs.
That"s when the trouble started.
Little things went wrong at first, but they got worse and more expensive over the next four years, especially whenever thunderstorms passed nearby.
"I used to call them "gremlins" or "sunspots" because our problems were very sporadic," recalls John Stiles III, McAfee"s senior programmer and the man who sold management on the benefits of networking. "We had so many "little" symptoms that finding the exact cause of the problem was difficult."
In fact, the problems were anything but little when you added them up:
- Communication to a CNC machine would stop in mid-program or never start in the first place. So much for better machine control.
- CRT screens would flicker or distort. An annoying problem, maybe, but a sign of more trouble to come.
- Characters in programs would be missing or altered.
- Ports on the computer side of the server box would quit working. No port, no communication; no communication, no production.
- Communications boards in the CNC machines"e; computers would burn out and have to be replaced. Boards aren"t cheap; these costs added up quickly.
- An RS-232 cable resting against a particular machine would cause other machines not to work. Supporting the cable with a piece of string made the machines work. It was a Rube Goldberg sort of solution. Many service technicians thought Mr. Stiles was wasting his time. "They thought I was crazy," said Stiles. "I was told my quick fix with the string was impossible, but it was just one of many steps I took in a process of elimination to find the problem, and at least it worked for the time being."
Plenty of Bad Suggestions
The company added or changed several CNC machines over the next four years. With each change on the shop floor, each machine"s ability to communicate would change. Networking problems continued, but neither their cause nor a solution was in sight. Scores of experienced technicians from OEMs plus equipment repairmen and networking software suppliers offered solutions. Among their dozens of "Try this, let me know if it works"-type of suggestions were:
- Reset the ports on the computer side of the serve box to re-establish a signal.
- Reboot the computer to re-establish communication.
- Disconnect the ground on the RS-232 cable on the computer side.
This was, in fact, the way the original network was configured, incorrectly, following the network technician"s instructions. - Change to shielded hoods on the machines. Shielded hoods were supposed to eliminate problems due to electromagnetic interference (EMI) and radio frequency interference (RFI), two known causes of data errors. The change cost money but had no effect.
- Change to double-shielded cable, but disconnect the ground leads to the shielding.
- Change pinouts on communications cables from hardware handshake to software handshake protocols.
- Pour water down the hole around the ground rods located next to each machine.
This one requires some explaining. Supplemental ground rods for individual pieces of equipment are somewhat unique to the machine tool industry. No one would think of driving a separate ground rod for each computer in an office, but the practice is widespread in machine shops. In fact, the practice was recommended by 10 out of 15 CNC machine tool OEMs surveyed in a recent study conducted for the Electric Power Research Institute (EPRI). Three of the fifteen OEMs surveyed even said that failure to install the rods would void their equipment"s warranty. Supplemental ground rods are permitted under the National Electrical Code ® (NEC), but they should only be installed, if at all, after a careful analysis of the building"s entire electrical, grounding and lightning protection systems. Installing supplemental ground rods at individual CNC machines is not a good idea. OEM installation manuals specifically do not recommend it. Supplemental ground rods, especially those that are allowed to "float," may actually decrease reliability and increase the risk of damage to the machines" electronic circuitry. - Disconnect the RS-232 cables at the machine side during thunderstorms.
- Disconnect the RS-232 cables at the machine side between each use.
An experienced technician advised against this fix on the grounds that it would create an antenna, allegedly making noise problems worse. - Float the ground leads for each machine"s control cable. Strange as it sounds, the idea of floating (disconnecting) control cable grounds at one end of the cable is still argued in the machine tool industry. Some OEMs maintain that doing so reduces small ground current loops at power frequencies, but the open circuit voltages thus generated can couple from shields to data conductors inside the cable, thereby actually making the situation worse. It is good practice to ground all cable shields at both ends of the cable using proper 360 degree terminations.
- Float the ground for the machine itself, i.e., isolate the supplemental grounding electrodes at each machine from the building"s equipment grounding circuit.
THIS SUGGESTION IS NOT ONLY DANGEROUS, IT IS A VIOLATION OF THE NEC AND FOLLOWING IT WOULD BE ILLEGAL! UNFORTUNATELY, THE PRACTICE OF DISCONNECTING GROUNDS IS QUITE COMMON IN CNC MACHINE SHOPS.
Disconnecting machine grounds from the building"s equipment grounding system is an example of what John Stiles calls the "folklore" surrounding the installation of CNC equipment. For the record, CNC machine OEMs never recommend disconnecting ground connections at the machines, but many installers, technicians and repairmen cling to the belief that this illegal practice is helpful. They apparently don"t appreciate that CNC machine tools are computer-driven devices and that they should be treated as "sensitive electronic equipment" according to the recommended practices in IEEE Std. 1100 (The Emerald Book).
Fortunately, McAfee Tool & Die didn"t follow this suggestion.
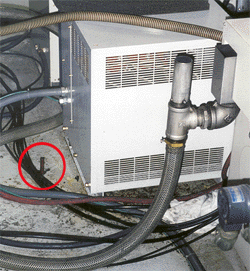
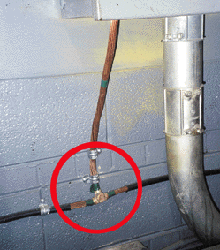
Searching for Clues
By January 1998, six of McAfee"s twelve CNC machines were disconnected from the network due to the many problems experienced. Now things really went downhill. Although the company had only lost one 16-port terminal server in four years, it lost three more in the first three months of 1998. For awhile, the shop was reduced to operating from punched paper tapes and sharing one old computer to control its machines.
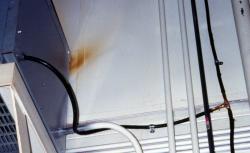
Then a clue surfaced. While the new computer system didn"t solve the problems, its software did have the ability to identify unknown data entering the computer from the CNC machines and write it to a file. Within a month, the computer had generated thousands of such files, all originating from specific machines. The system still worked reasonably well despite the incoming noise, but Stiles waited, knowing that something would have to give sooner or later.
It happened during the next thunderstorm, which took out communications boards in two machines and one COM port on the computer. The programmer was vindicated: the problem did not lie in the computer system but in the CNC machines themselves. Back to Top
Finally, a Real Expert
Suspecting that poor grounds were the true source of McAfee"s networking difficulties, Ohio Edison recommended the company contact PowerEdge Technologies, Inc, a consulting organization that specializes in grounding problems. Stiles called them, and PowerEdge sent Tim Cookson, its senior electrical engineer.
Cookson began his survey by measuring the ground rod resistance at each CNC machine. The results were revealing:
"We"ve done half a dozen machine shops in the Akron area over the years," recalls Cookson," and every one of them had problems like the ones we found at McAfee. Many of the people who install CNC machines don"t understand that these things are computers and computers need good grounding."
A new, bonded, grounding electrode conductor connection at McAfee Tool & Die prior to backfilling. PowerEdge Technologies specified #4/0 AWG copper for external grounding electrode conductors. The 10-ft grounding electrode and all conductors were buried at least two feet below the surface to ensure good ground contact. the all-copper system"s 7 ohms ground resistance helps ensure reliable computer communications.
PowerEdge Technologies recommends that installations housing sensitive electronics have a ground resistance to earth less than 10 ohms; none of McAfee"s CNC machines met that criterion, and one measured a startling 570 ohms! To make matters worse, neutral-to-ground potentials at the various machines measured between 33.2 V and 50 V. OEMs recommend that neutral-to-ground potentials be less than 2 V. "RS-232 systems operate between 8 V and 12 V." Observes John Stiles, "With the readings we had, I"m surprised the system ever worked at all!"
Interestingly, two of the three machines with the highest ground resistance readings, Mitsubishi Machining Center #2 and EDM Machine #5, were the only ones to have both their communications circuit boards and the COM ports on the server computer destroyed during the previous thunderstorm. That was a strong tip-off that the problem lay in the installed grounding system.
Back to TopSolution Relies on Copper
"The electrical system in McAfee"s shop just wasn"t capable of supporting today"s sensitive electronic equipment," says Cookson. "The system had one, old primary ground rod, and its resistance was high. Ground resistance at all those unnecessary supplemental rods next to the CNC machines was too high, and some were very high. There were ground loop currents everywhere. On top of that, much of the building"s interior wiring was aluminum, and many connections had corroded over the years."
"We brought the company"s electrical and grounding systems back to basics. We set up the building steel as a reference, then bonded each CNC machine and all electrical equipment panels to it using #6 AWG copper and exothermic-type connections. We replaced all of the old aluminum with copper cable and copper connectors. Outside, we drove three new 3/4-inch X 10-ft ground rods in a triangular pattern at the main service entrance, burying them and their ground electrode conductors two feet below grade to ensure good contact and low resistance. For electrode conductors we used #4/0 AWG copper, bonding everything with exothermic connectors. In fact, in all of our jobs, we use nothing but copper."
The new system has a ground resistance of only 7 ohms, and the ground system noise on the communications cables is below 1.5 V. John Stiles is more than satisfied. "Before Power Edge came in, I was getting nothing but bad advice and I was running out of ideas. When Tim Cookson first looked at our shop, he walked around with a grin on his face like he"d seen it all before, and when he said "Do this and it will work" instead of "Try this and let me know," I knew he could help us."
"Since we installed the new copper grounding system we haven"t had any problems with our CNC and CAD/CAM networks. Poor grounding was the problem all along, but it took us four years to realize it. We"re now so confident that our system is reliable that this year we replaced our shared network with a high-speed switched network, giving us even better efficiency. We want to stay one step ahead of the competition!"
Back to TopGrounding and Network Signal Noise
Computers are highly sensitive to signal noise, which is defined as spurious voltage fluctuations, usually of variable and unknown magnitude and frequency. RS-232 circuits operate between 6 VDC and 12 VDC, and while this potential seems relatively generous, it is not uncommon for signal noise to be of the same magnitude or even larger. At McAfee Tool & Die Inc., signal noise levels ranged between 15V and 17V on the communications cables.
Logic circuits are even more sensitive to noise, since in most modern computer systems, the difference in potential between a "0" (the "signal reference potential") and a "1" data bit can be less than 1 V. Data errors can arise when the signal reference potentials at two connected computers are different, as can occur when the computers are connected to separate grounding electrodes having different groundresistances's.
The problems experienced by McAfee Tool & Die Inc. are a textbook example of what can happen when sensitive electronic equipment is improperly grounded. Problems arise when ground loop currents are induced in the grounding conductors linking various pieces of equipment. For example, consider the situation pictured below.
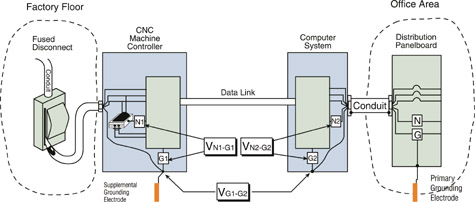
A supplemental electrode attached to a CNC machine. In this arrangement, the machine cabinet, as well as cable trays and other electrical equipment, are also properly bonded to the ground bus at the service entrance switch (the first disconnect). This practice is permitted under the NEC, but it can cause problems due to the formation of ground loop currents.
(Illustration adapted from Power Quality Considerations for CNC Machines: Grounding, Copyright 1997, Electric Power Research Institute. BR-107170. Reprinted with permission.)
The CNC equipment is properly grounded through a "green wire" (not shown) and through the conduits and raceways, to the ground bus/neutral bus junction at the service entrance panel, and from there to the grounding electrode(s) located outside the building. Grounding connections are also made from the neutral-ground bond at the service entrance panel to a metal water pipe and to the building steel. The left of the figure shows a supplemental grounding electrode installed at the CNC machine and connected to the machine cabinet, as originally configured at McAfee Tool & Die. This arrangement is permitted under the NEC, which is concerned mainly about safety, but it is not recommended under IEEE Std. 142 (The Green Book), Grounding of Industrial and Commercial Power Systems, and IEEE Std. 1100 (The Emerald Book), Powering and Grounding of Sensitive Electronic Equipment.
Any differences in the ground resistance of the main and supplemental grounding electrodes can drive ground loop currents circulating through the ground and grounding connectors connecting machines with other elements in the electrical and/or data systems. The grounding shield surrounding data cables connecting CNC machines and the central computer are one such return path. Current flowing in this path as a result of ground loops constitutes a noise signal that can disrupt data communications. This is precisely what happened at McAfee Tool & Die before the supplemental electrodes were disconnected and a proper grounding system was installed.
Back to TopThe Principals
John C. Stiles III is a senior programmer at McAfee Tool & Die Inc. When he joined McAfee in 1990, computer networks were rarely used in the tool and die industry. John was instrumental in networking his company"s Unix-based CAD/CAM workstations in 1992 and its CNC machines in 1994. In 1998, he oversaw the grounding system installation that allowed for the integration of both networks.
Tim Cookson, CPQ, PAE, is a senior electrical engineer with PowerEdge Technologies, Inc. In addition to a degree in electronics from the University of Akron and a BSEE from LaSalle University, Tim is certified as an electrical contractor and as a power quality professional. He also holds a Professional Administrator/Electrical license in the state of Washington. Besides conducting power quality surveys and designing proper grounding systems (as he did for McAfee Tool & Die), Tim develops computer/network site planning documents and project management services and performs power quality and power management surveys.
McAfee Tool & Die Inc. is a full-service tool and die shop/manufacturing facility located in Uniontown, Ohio. In addition to its conventional and CNC machining work, the company operates metal-stamping presses and plastic injection molding equipment for prototyping and pre-production trials of its dies and tooling, as well as full-scale production for customers in automotive, aerospace and medical technology fields. McAfee Tool & Die has been recognized in the trade literature for its willingness to adopt new technologies such as the networking of design and manufacturing operations described in this article. For additional information about McAfee Tool & Die, call (330) 896-9555, fax (330) 896-9549 or visit the company"s Web page at: www.McafeeTool.com.
PowerEdge Technologies, Inc. is a Canton, Ohio-based consulting and engineering firm specializing in power quality issues, including power quality and power management surveys, harmonic assessments, grounding and electrical system testing, operating environment assessments and site planning services for sensitive electronic equipment. The company also provides educational services to industrial, trade and educational organizations. For further information about PowerEdge Technologies and its services, call (330) 494-7314, fax (330) 494-7750 or visit their web site at: www.poweredgetech.com.