April 12, 2006
FOR IMMEDIATE RELEASE
NEW YORK, NY— A practical die-cast copper rotor for electric motors has been the "holy grail" for motor manufacturers for many years. Last year, Siemens AG, Munich, Germany, optimized the revolutionary rotor design and recently, introduced three new product lines to the North American market through its U.S. operating company, Siemens Energy & Automation, Inc. The company claims its unique die-cast copper rotor design is one of the key elements that enable its Ultra Efficient motors to exceed NEMA Premium® standards.
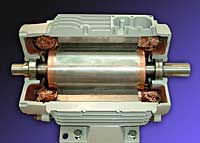
Click here for a high-resolution version of this photo.
The new, copper rotor technology is the result of several years of research and development by the Copper Development Association (USA) and the International Copper Association, both headquartered in New York City. Dr. John Cowie, CDA project manager of the research program, offered congratulations to Siemens on successfully bringing the new technology to the U.S. market. He notes that Siemens has been an important partner in determining the economic feasibility and profitability of commercializing the copper die-casting technology. "Siemens has raised the bar on electrical motor efficiency, and we look forward to more manufacturers adopting the technology. The use of die-cast copper rotors reduces energy requirements, allows motors to run cooler, extends motor life and reduces overall weight and/or size."
In addition to Siemens, Germany's SEW Eurodrive currently offers their DTE and DVE series of high-efficiency motors with copper rotors. FAVI S.A., Hallencourt, France, is producing die-cast copper rotors for use by other motor manufacturers, including ITT/Grundfos in Europe. They are also working with Electrolux and Whirlpool Europe on appliance motors and with Embraco in Brazil on compressor applications. Cowie says at least one U.S.-based OEM and several motor manufacturers are poised to enter the North American market, too.
Siemens' three new product lines include general purpose die-cast aluminum, general purpose cast iron and severe duty cast iron frame motors for use in a wide variety of industrial applications, including a definite purpose version, exceeding the demanding requirements of IEEE Standard 841.
Siemens achieved superior efficiency in its new motors by combining the inherently low resistive (I²R) losses of high-conductivity copper squirrel cages with optimized rotor and stator designs. Other improvements include a redesigned cooling system, antifriction bearings, polyurea-based grease, dynamically balanced rotors and precision-machined mating surfaces for reduced vibration. Specially designed insulation enables the motors to meet NEMA standard MG1-2003 for variable speed (inverter duty) operation. John Caroff, Siemens marketing manager for low-voltage motors, said these Siemens innovations will provide significant energy and cost savings to the U.S. industrial sector where motor-driven equipment accounts for 64 percent of the country's electricity consumption.
According to Siemens, the new lines of motors are available up to 20 horsepower. Over the coming months, the aluminum-frame line will be expanded to 30 hp and the cast-iron frame line to 400 hp.
Additional information on the new Siemens motors can be found at: www.sea.siemens.com. Information on the die-cast copper motor rotor technology is on the CDA website at: www.copper.org.
###