Download PDF Version [582 Kb]
- Efficiency, Reliability, Quality
- "Multi-beneficial" Equipment Saves Dollars
- First Cost and Value Engineering Can Mean False Savings
- Premium Efficiency Motors: The Big Energy Savers
- More Good Ideas
- Comprehensive Energy Program
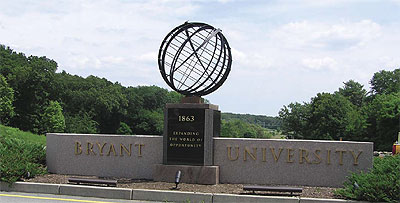
Bryant University is an interesting success story in American higher education. The university began as the Providence, Rhode Island, branch of a chain of small business colleges in 1863, teaching basic office skills to returning Civil War veterans — and a few enterprising women. Over the succeeding 100-plus years, it has evolved into a multi-disciplined institution offering undergraduate and graduate degrees in accounting, computer information systems, finance, management and marketing, among other business-oriented subjects. In 1970, the school relocated to a modern, suburban campus in nearby Smithfield (Figure 1) serving some 3,000 students.
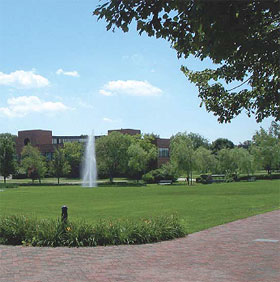
What does all this have to do with copper? Plenty, because copper means high electrical efficiency, and Bryant University, like many educational institutions today, faces the challenge of providing its students with top-notch facilities while keeping a tight lid on costs – energy costs, to be precise. At Bryant, key facilities include a full array of the latest generation computer and communications equipment (Figure 2). The energy needed to operate that equipment, combined with even larger demands from lighting, security, safety and HVAC systems, makes for sizeable energy bills. Worse yet, local utility rates are more than 35% higher than the national average.1
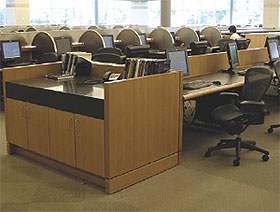
Bill Gilmore is Bryant University’s assistant director of facilities, operations and services. He has the job of reducing Bryant’s energy costs without cutting services, and he’s been quite successful at it. “Energy efficiency has saved my energy budget,” says Gilmore. At one time, it also saved his paycheck: when he joined the staff in 1988, his salary was funded by the reductions in energy costs he managed to make. That isn’t the case anymore, because, as Gilmore has clearly demonstrated, energy costs can be reduced substantially even in a facility that has continuously been enlarged and upgraded.
Back to TopEfficiency, Reliability, Quality
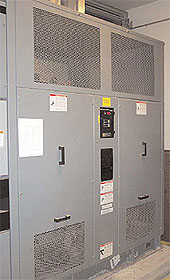
Gilmore has a big job: (a) saving his employer money; (b) providing reliable power to the school’s extensive computer network and its security and safety systems; and, for good measure, (c) making certain the power delivered is of the highest possible quality so all that sensitive electronic equipment functions properly. Ironically, computers and other equipment operating on switched-mode power supplies are strong sources of harmonic distortions. If not kept in check, harmonics can seriously degrade power quality, damage equipment and create a fire hazard.
Copper helps makes Gilmore’s job easier. In fact, he insists that copper is used exclusively on the campus. “Aluminum stops at the meter!” he says, with the kind of conviction gained from years of experience.
As one example, Gilmore points to the twin, dry-type 750-kVA transformers at the electrical service entrance in Bryant’s George F. Bello Center for Information and Technology (Figure 3). The 12,470V-480/277Y transformers were installed in 2001 as part of a continuing upgrade to the campus electrical system. Gilmore wrote the equipment specifications for that upgrade, and the transformers, like all others on campus, are 100% copper-wound. “I’ve had too much experience with what can happen to aluminum,” he says, “and that’s why I specify copper all the time. Since 1988, when we got rid of aluminum, we have not had a major electrical outage on campus.”
Back to TopMulti-beneficial Equipment Saves Dollars
Gilmore also insists that all distribution transformers in the Bello Center and elsewhere on campus are K-13 rated, because the electrical system has a high harmonic content. That includes dormitories, since every student is issued a laptop upon admission. Most transformers, particularly those serving sensitive circuits, are also shielded against electrostatic interference.
Gilmore believes that equipment should offer multiple benefits. For example, copper-wound transformers provide high efficiency, high reliability and high power quality for a single initial investment. He applies the same thinking to motors.
Back to TopFirst Cost and Value Engineering Can Mean False Savings
But getting his cost-saving message across wasn’t always easy. “The concept of avoided cost was, initially, the most difficult selling job I had,” says Gilmore, “but management understood the concept, and it has been one of the most important driving forces in the way we specify and run our system. If I can install a better transformer now, I know that we’ll have fewer problems and lower maintenance costs in the future. First cost is irrelevant! Reliability and operating efficiency reduce life-cycle costs. They avoid costs and save money for years, and that’s what really counts. Life-cycle cost is true cost, and that’s especially important with a declining work force allocation.
“We’ve also learned not to apply value engineering to electrical systems,” says Gilmore. Value engineering (also called value analysis) is a methodology developed during World War II that attempts to place a worth on a particular function, conceive multiple alternatives to fulfill that function, and then select the alternative that offers the lowest overall cost. It has been applied to commercial products, military systems and even highways, to name just a few examples. However, questions can arise due to the subjective reasoning that inevitably must be applied during a VE analysis. What fair level of cost, for example, can be placed on the reliability of a university’s electrical system, especially in view of the importance of safety, fire-protection and security systems?
“Value Engineering may have it’s place,” allows Gilmore, “but it is not an asset to facilities engineers. The reason for having carefully written specifications is to avoid repeating problems encountered in the past, not cutting costs up front. You can’t cheapen an electrical system and expect to save money in the long run.”
Back to TopPremium Efficiency Motors: The Big Energy Savers
Electric motors consume the lion’s share of energy at Bryant. Nationwide, motors use 23% of all the electric power the country generates. Keeping Bryant’s computers cool (and all those students comfortable) requires a large HVAC system, which, along with other mechanical services, is where the motors are.
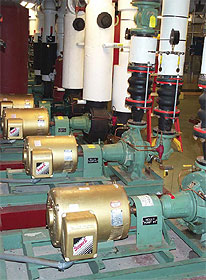
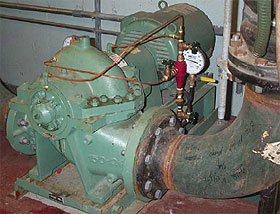
That wasn’t always the case. When Bryant opened its Smithfield campus, the National Energy Policy Act of 1992 (which mandates minimum motor efficiencies, among a lot of other things) was still decades in the future. EPAct ’92 (updated in 2005), as it is known, specifies that all motors of certain types sold in the USA after October 24, 1997, meet or exceed nominal efficiency levels listed in the National Electrical Manufacturers Association (NEMA) publication: MG 1-1993, Table 12.10. EPAct covers motors from 1–200 hp, 3600, 1800 and 1200 rpm, horizontal, T-frame, single speed, 460 V, NEMA design B. The efficiencies of EPAct-conforming motors are generally between one and four percentage points higher than the so-called standard-efficiency motors sold prior to 1997.
In 2001, NEMA published even more stringent energy efficiency requirements under the registered NEMA Premium® standard. Efficiencies of NEMA Premium motors are between one and two percentage points higher than those of equivalent-size EPAct motors, and the standard covers a broader range of sizes, up to 500 hp.2 Both EPAct and NEMA Premium motors gain their improved efficiency largely from the fact that they contain up to 20% more copper than other motors. More copper means lower resistive losses and higher efficiency — plus cooler operation for longer life and higher reliability.
Do those few percentage points justify the small price premium that NEMA Premium motors can (but don’t always) command? Absolutely! A motor operating full-time at full load consumes power equivalent to between 10 and 25 times the motor’s purchase cost per year. At that rate, it doesn’t take long for small savings to add up to big returns. All of Bryant University’s motors meet NEMA Premium efficiency standards, the only exceptions being special-purpose models, which aren’t included in the standard. Here are a few representative examples:
Hot- and cold-water circulation pumps in the Bello Center are driven by four 25-hp ODP motors (Figure 4). The motors were installed in 1988 and replaced standard-efficiency units dating to 1970. The new motors, with 94.1% efficiency at 100% power accrued savings to Bryant University of $679 each, annually, and thus, paid for themselves in only 1.5 years.
Another good example is a 40-hp ODP motor that drives water pumps on the condenser located in the university’s Wellness Center (Figure 5). It meets the NEMA Premium efficiency requirement, 94.5% for this horsepower rating. Since being placed in service when the bearings of an existing standard-efficiency motor failed, the motor has saved the school $1,059 and 10.3 MWh/y since its installation versus the standard-efficiency motor it replaced. Again, the payback was only 1.5 years.
Gilmore decided to replace the old motor’s bearings anyway and place the unit in storage as a spare since it is a long lead-time item. (He was glad he did, when, a few years later, the new motor’s bearings failed due to a maintenance glitch.)
“I reinstalled the old motor because we needed the service,” he recalls, “but as soon as the premium-efficiency one came back from the shop, I put it back on line. Can you imagine the money that old motor would have cost to run at 10 cents a kilowatt-hour? Its lower efficiency cost us $80 for the first month alone, or nearly enough to pay for the reinstallation.”
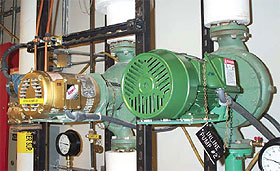
We could go on, since there are dozens of other premium motors in service at Bryant. But you get the idea: replace inefficient standard-efficiency motors with NEMA Premium (or equivalent) motors and the dollars saved will not only offset the cost of the new motors quickly, they will continue to accumulate as long as the motors are in service. The higher the motors’ duty cycles and the higher the utility rate, the shorter will be the payback and the bigger the savings.
More Good Ideas
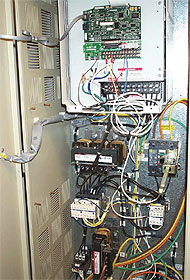
A few other improvements made by Gilmore and Greg Gurney, the university’s facilities engineer, include installation of variable frequency drives and line reactors on HVAC blower motors with variable torque loads larger than 7.5 hp to adjust speed according to demand (Figure 7). “Value Engineering wanted us to install constant air volume drives, which are cheaper but run at one speed regardless of demand,” says Gurney. “Variable air volume (VAV) drives add to initial cost, but they allow us to use only as much power as needed. Just like premium-efficiency motors, VAVs save big money in the long run, especially when combined with the better motors.
“We employ a few other energy-saving tricks, like making ice for our chillers at night, when chiller demand and utility rates are lower, then using that ice for cooling during the day. Our chillers were made in China, and there are monitors on them that report performance directly to Shanghai via the Internet. When something isn’t right, we receive instructions for a fix immediately, 24/7. We monitor our blowers, too.
“We also resized some motors to save energy,” adds Gurney. “We ran current checks on all fans and pumps under full load, and if full-load current was below 70%, we looked at downsizing the motor. We did find two places where we could indeed go from a 10-hp motor to a 7.5-hp model.”
Back to TopComprehensive Energy Program
Bryant University is a fine institution of learning for its students. But the foresight its leaders showed in formulating and executing a comprehensive energy program provides an example by which others can learn, as well. Energy consumption and unnecessary costs can be reduced. All it takes is good planning and knowledgeable people — plus enough copper in the right places — to make it work.
MotorMaster+
- Are you facing a motor repair-or-replace decision?
- Do new motors have to pay for themselves in less than two years?
- Are you planning an energy conservation program?
- Do you just want to reduce your electrical energy costs?
Find answers to these and many other questions with MotorMaster+
MotorMaster+ is a management tool for selecting energy- efficient electric motors. It enables users to compare more than 20,000 commercially available motors on the basis of their nameplate energy-efficiency ratings, purchase price and operating parameters. Version 4.0 of the software contains enhanced motor inventory management tools, maintenance log tracking, company-wide efficiency analysis, savings evaluation, energy accounting, and environmental reporting capabilities - in short, almost everything an engineer, facilities manager or purchasing agent needs to make dollars-and-sense decisions about electric motors. MotorMaster+ software is available by request at AMO Tools Help Desk.
Let’s say a 15-year-old, standard efficiency, 460-V, 20-hp, HVAC fan motor burns out (probably not the first time). You know that:
- It operates at 75% load, 24/7, for 50 weeks per year, an 8000 h/y duty cycle.
- Its nameplate efficiency is 88.3%.
- Electric power costs you $0.075/kWh.
- The repair shop estimates it’ll cost you $536 for yet one more rewind, but rewinding will reduce efficiency by 1%.
- A new NEMA Premium motor will cost you $623 after a 56% dealer discount.
- The new motor has a NEMA nominal nameplate efficiency of 93.3%, and, because it’ll run cooler than the old burned-out motor, it’ll probably last at least 10 years before rewinding.
- Your company’s accountant won’t let you buy new capital equipment unless it can pay for itself in less than two years.
Should you rewind the old motor or spring for the NEMA Premium model?
Plug the above data into MotorMaster 4.0 and you instantly learn that:
- The new NEMA Premium motor will save you 5,142 kWh per year.
- You’ll save $406 per year in energy costs after installing the new motor (and every year thereafter).
- The new NEMA Premium motor will pay for itself in 2½ months, giving an after-tax, benefit-to-cost ratio higher than 25.
You smile and ask to see that accountant.
The Principals
William (Bill) Gilmore is assistant director of facilities, operations and services at Bryant University, Smithfield, Rhode Island. By helping formulate and then applying the university’s energy management program, he has succeeded in reducing energy consumption significantly. The costs avoided provide funds that benefit students and the university at large. Mr. Gilmore can be reached at 401-232-6425, bgilmore@bryant.edu.
Greg Gurney is Bryant University’s facilities engineer. A graduate of the Massachusetts Maritime Academy with more than a decade of shipboard experience, Mr. Gurney has learned, in the words of his management, how to make things work. Mr. Gurney can be reached at 401-232-6912, ggurney@bryant.edu.